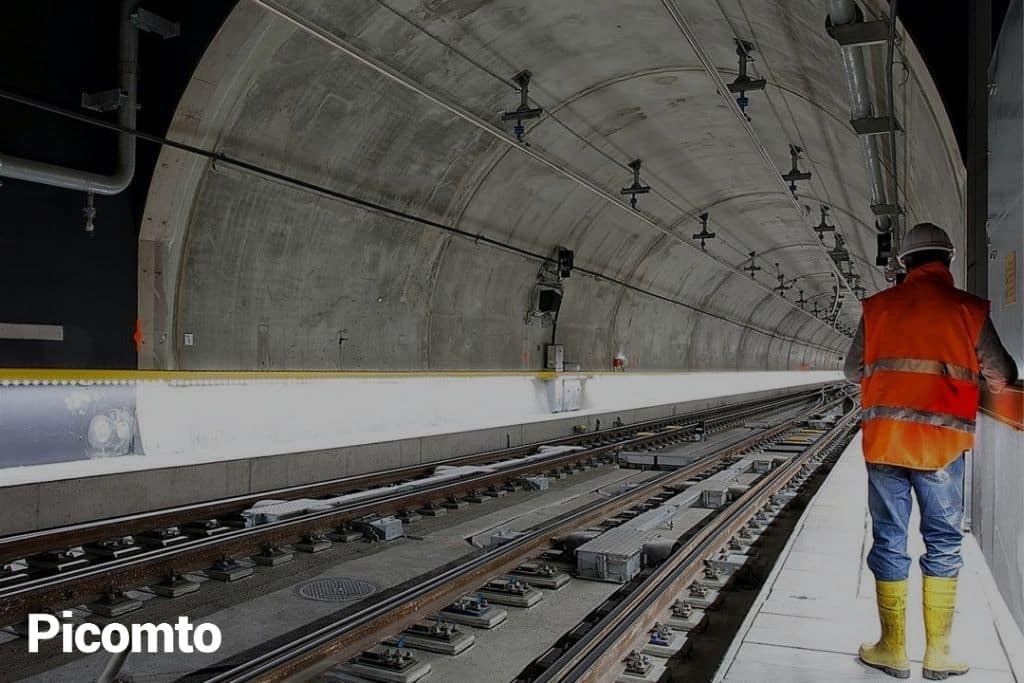
Bis vor kurzem wurde die industrielle Instandhaltung nur als Verpflichtung, Belastung für die Unternehmen und ausschließlich als Kostenquelle wahrgenommen. Instandhaltungsarbeiten sind kostenintensiv, aber wenn sie intelligent organisiert und verwaltet werden, tragen sie auch zur Wertschöpfung bei. Ihre Verbesserung ermöglicht es dem Unternehmen daher, effizienter und wettbewerbsfähiger zu sein. Die Optimierung der Instandhaltung wird erreicht durch:
- Die Umsetzung einer Strategie, die an die Besonderheiten des Unternehmens angepasst ist.
- Verbesserung der Verfahren und Kanäle für den Austausch zwischen den Beteiligten: Manager, Betreiber, Wartungstechniker usw.
Anwendung geeigneter Strategien
Wir warten nicht mehr darauf, dass Vorfälle auftreten, bevor wir handeln. Die vorbeugende Instandhaltung ist bereits seit einiger Zeit Teil der in Unternehmen eingesetzten Methoden.
Um die Betriebsfähigkeit der Maschinen und ihren Wert zu erhalten, werden programmierte Eingriffe nach genau definierten Kriterien (Anzahl der Betriebsstunden, Anzahl der Umdrehungen, Anzahl der produzierten Teile usw.) bevorzugt, wodurch die „Ausfallwahrscheinlichkeit oder Verschlechterung der Funktionsfähigkeit eines Vermögenswertes“ (AFNOR) reduziert wird. Regelmäßige und proaktive Wartungsarbeiten reduzieren das Risiko von Ausfällen und deren Folgen, insbesondere in finanzieller Hinsicht. Wenn ein Teil der Produktion eingestellt wird, weil ein Gerät ausgefallen ist, stellt dies natürlich einen erheblichen Kostenfaktor für das Unternehmen dar.
Unter den in der Branche geschätzten Instandhaltungsmethoden gibt es auch TPM (Total Productive Maintenance). Dies ist in der Tat eine japanische Entwicklung der Instandhaltungsverfahren, die in den Vereinigten Staaten im Automobilsektor begann.
Sie setzt auf:
✓ Die Effizienz von Instandhaltungsmaßnahmen: die erforderliche Zeit, Ressourcen und Organisation dafür aufwenden).
✓ Kontinuität der Produktion: Sie sollte nicht durch Interventionen bestraft werden.
✓ Der gesamte Ansatz: unter Berücksichtigung aller Aspekte der Instandhaltung und unter Einbeziehung aller Beteiligten, einschließlich der Betreiber.
Antizipation und Kooperation sind daher die beiden Hauptmerkmale des TPM, das darauf abzielt, die Effizienz der Produktionsmittel zu optimieren.
Verbesserung der Kommunikation zwischen den Beteiligten
Kommunikation ist in jedem Unternehmen von entscheidender Bedeutung. Im Bereich der industriellen Instandhaltung ist sie insofern unerlässlich, als sie, wenn sie flüssig ist, sowohl bei kurativen als auch bei präventiven Maßnahmen erhebliche Zeit- und Kosteneinsparungen ermöglicht.
Tatsächlich gehen nur kostbare Minuten – sogar Stunden – der Produktion verloren, wenn im Falle eines an einer Maschine beobachteten Ausfalls Informationen zwischen dem Bediener, seinem direkten Leiter (dem Werkstattleiter) und der Instandhaltungsabteilung zirkulieren müssen, die dann einen Techniker finden muss, der sich vorbereiten und mit der Reparatur oder dem Austausch von Teilen beginnen muss. Diese Art von veralteter Organisation ist nicht nur langsam und kostspielig, sondern auch eine Quelle des Desinteresses und der Demotivation für den Wartungstechniker. Die Digitalisierung von Dokumenten, einschließlich Wartungsblätter und Berichte, ist Teil dieser Logik der Verbesserung der Kommunikation und des Austauschs zwischen den Interessengruppen des Unternehmens.
Picomto ist die Lösung zur Digitalisierung von Instandhaltungsverfahren und Feldinformationsaufzeichnungen.