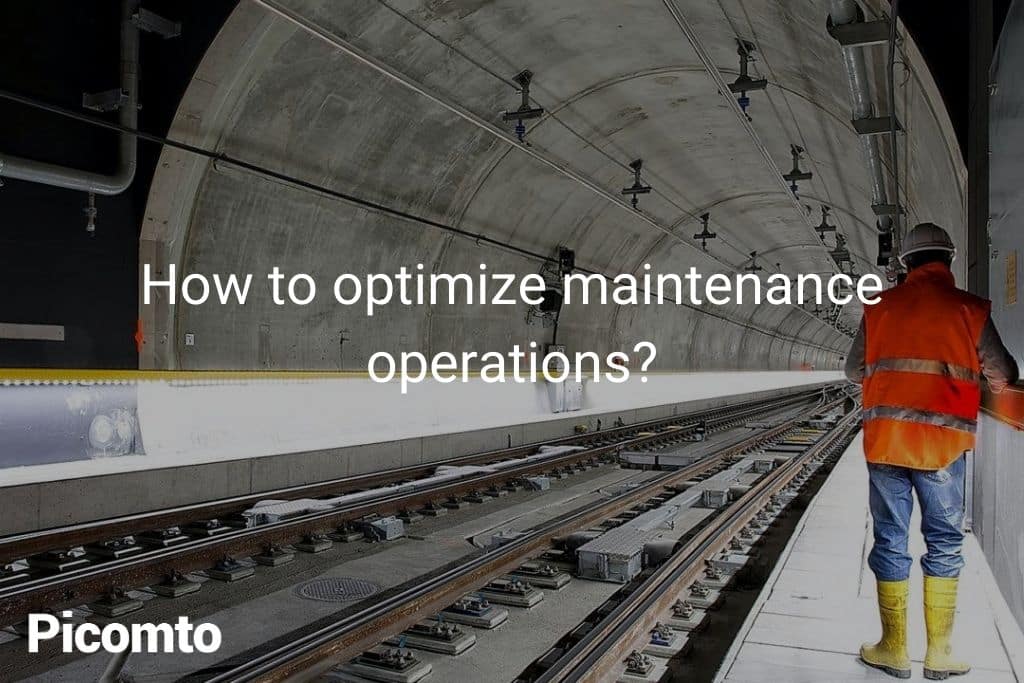
Until recently, industrial maintenance was perceived only as an obligation, a burden for companies and exclusively a source of expenditure. Maintenance operations have a cost, but when they are intelligently organized and managed, they also contribute to value creation. Improving them therefore allows the company to be more efficient and better equipped to compete. The optimization of maintenance is achieved through:
- The implementation of a strategy adapted to the specificities of the company
- Improving procedures and channels for exchanges between stakeholders: managers, operators, maintenance technicians, etc.
Adopt appropriate strategies
We no longer wait for incidents to occur before acting. Preventive maintenance has already been part of the methods in use in companies for some time.
To preserve the operational capabilities of the machines and their value, priority is given to programmed interventions according to well-defined criteria (number of operating hours, number of revolutions, number of parts produced, etc.), reducing “the probability of failure or deterioration in the functioning of an asset” (AFNOR). Regular and proactive maintenance operations reduce the risk of breakdowns and their consequences, particularly in financial terms, stopping part of the production because a piece of equipment is down. This obviously represents a significant cost for the company.
In this context, integrating solutions for remote maintenance of industrial machines allows maintenance teams to intervene more quickly and efficiently, even without being physically present, thus minimizing downtime and associated costs.
Among the maintenance methods appreciated in the industry, there is also TPM (total productive maintenance or total productive maintenance). This is, in fact, a Japanese evolution of maintenance procedures that began in the United States in the automotive sector.
She’s betting on:
- The efficiency of maintenance operations: devoting the necessary time, resources and organization to them)
- Continuity of production: it must not be penalized by interventions
- The entire approach: taking into account all aspects of maintenance and involving all stakeholders, including operators.
Anticipation and cooperation are therefore the two major characteristics of the TPM, which aims to optimize the efficiency of the means of production.
Improve communication between stakeholders
Communication is vital in any organization. In the field of industrial maintenance, it is essential. if it is fluid, it allows considerable time and money to be saved in both curative and preventive operations.
Indeed, only precious minutes – even hours – of production lost when, in the event of a failure observed on a machine, information must circulate between the operator, his direct manager (the workshop manager) and the maintenance department, which must then find a technician who must prepare himself and proceed to repair or replace parts. This type of outdated organization is, in addition to being slow and costly, a source of disinterest and demotivation for the maintenance technician. The collection of information must therefore be facilitated, which also implies the use of reliable, easily accessible and constantly updated media; the digitization of documents, including maintenance sheets and reports, is part of this logic of improving communication and exchanges between the company’s stakeholders.
Picomto is the solution for digitizing maintenance procedures and checklists. Contact us to know more.