Food industry
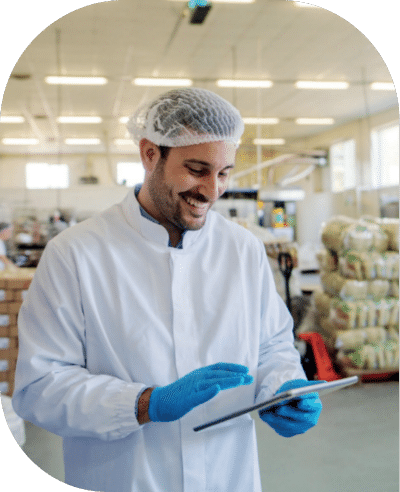
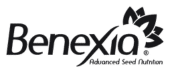
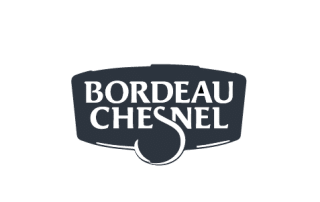
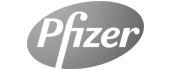
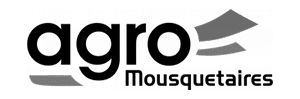
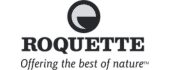
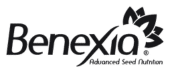
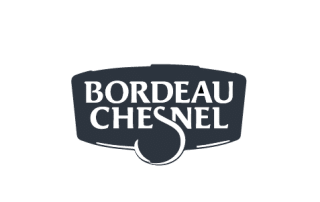
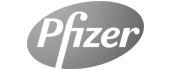
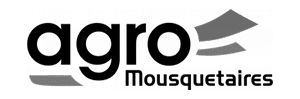
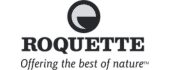
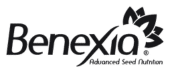
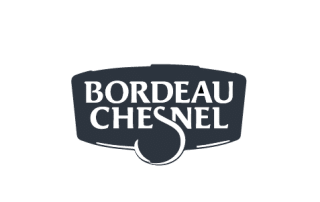
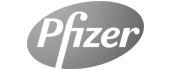
Improve the availability and reliability of your equipment
Apply the strictest standards, whatever the size of your structure and environment. Make safety rules reliable, even at the highest level.
Picomto revolutionizes the digitization of maintenance procedures and routines in the food industry by providing a platform for creating, storing and sharing interactive guides. This improves operational efficiency by providing visual instructions and precise information, thus promoting compliance with safety and quality standards.
The editor guides the operator step-by-step through simple troubleshooting. Thanks to its interface, users can quickly access visual and textual step-by-step instructions, making it easy to solve technical problems efficiently and independently.
Picomto supports maintainers in level 2 to 4 maintenance operations. This enables technicians to follow complex procedures in a structured and precise way, improving the efficiency and reliability of maintenance operations.
he platform visualizes cleaning operations in real time, providing live dashboards and reports that display the current status of maintenance operations. This provides visibility of tasks in progress, enabling informed decision-making to optimize the performance of maintenance activities.
By automatically recording procedures followed, intervention times and results obtained, the solution collects information to trace maintenance operations carried out. These data enable complete traceability of maintenance activities, promoting continuous improvement and compliance with quality standards.
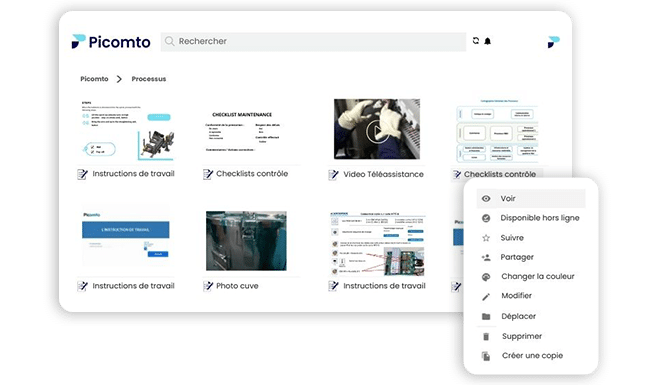
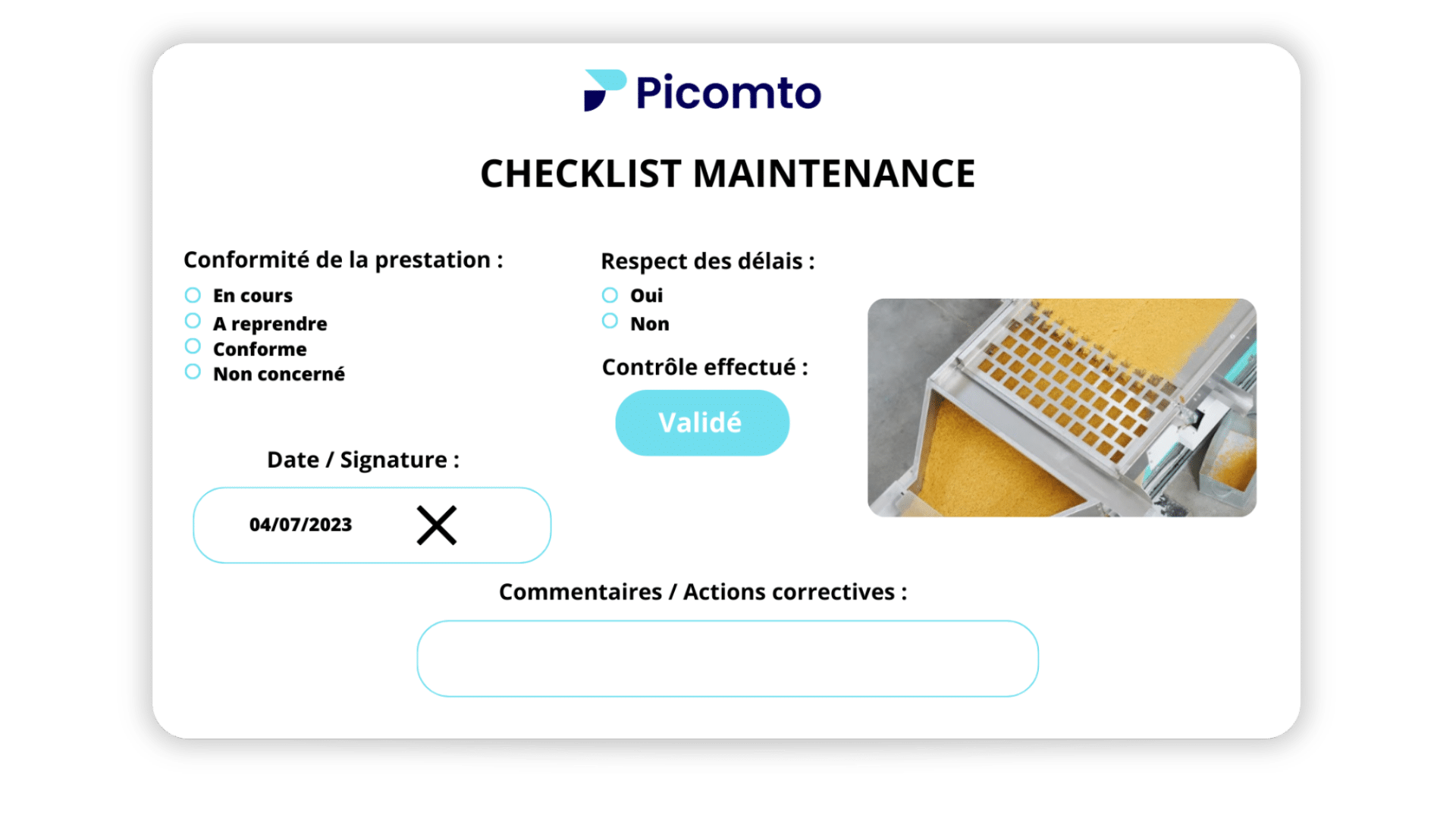
Operation
Constant reminder of the importance of current procedures and food hygiene rules
Track human operations in real time, manage the risk of human error and secure batch compliance.
Picomto makes Standard Operating Procedures (SOPs) more accessible. SOPs are presented with clear instructions, images and embedded videos, making them easier for staff to understand and execute. This approach improves standards compliance, productivity and quality of operations.
Let your experts suggest updates to operating procedures. Picomto capitalizes on know-how by enabling companies to organize essential knowledge and procedures within their organization. This platform provides a centralized means of accessing accumulated expertise, promoting the efficient reuse and transmission of skills.
With Picomto, the simplification, digitization and automation of controls are made possible by interactive, customizable checklists, which can be easily completed on mobile devices. This approach optimizes control efficiency by eliminating manual processes and offering centralized management of control data.
Intervention reporting is automated to simplify the process. Once an intervention has been completed, the data collected during the operation is automatically used to generate a detailed report, avoiding tedious manual tasks and guaranteeing instant, accurate documentation of activities in the field.
Reporting anomalies with Picomto is simplified thanks to its reporting functionality. Users can easily create reports including descriptions, images and relevant information on anomalies. These reports can be generated instantaneously and forwarded to managers for immediate action, promoting rapid response to problems.
Optimizing continuous processes with Picomto is made easy thanks to the dynamic creation and updating of procedures. Employees can quickly adapt and improve processes based on feedback, promoting operational efficiency and continuous innovation within the organization.
Picomto offers real-time metrics for efficient production optimization. By providing live data on performance and processes, it enables potential problems to be identified quickly and adjustments made in real time to maximize operational efficiency.
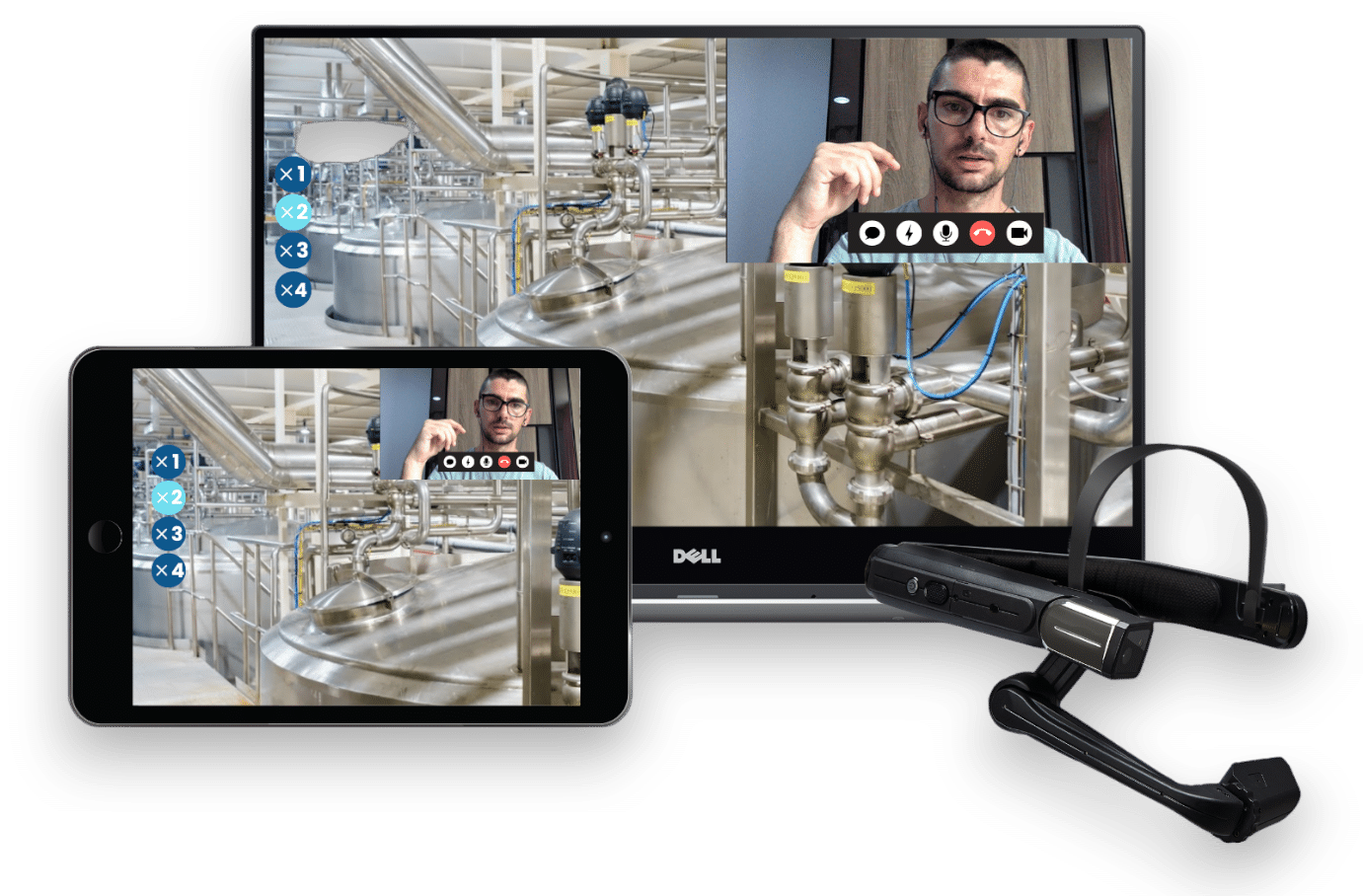
Smart collaboration
Streamline exchanges between employees
Teleport your experts remotely to PCs, connected glasses and Android tablets with a secure, intuitive expert solution.
Thanks to the Picomto platform, operators can ask questions, report problems or seek advice from the experts instantly. This enables them to obtain fast, accurate answers in real time, promoting a better understanding of the tasks at hand and avoiding unnecessary travel.
Experts have valuable expertise and specialized knowledge. Picomto enables operators to access this knowledge directly via the platform. Experts can share specific instructions, recommendations and advice for complex or critical tasks. This improves the quality of operations and enables any problems to be resolved quickly.
With Picomto, you can document and standardize procedures and work instructions. This ensures that all operators follow the same procedures, facilitating communication and collaboration. Operators can refer to detailed instructions and explanatory videos to perform assigned tasks correctly, reducing errors and variations.
With remote maintenance made possible by the Hololens augmented reality system, operators can send messages, photos or videos to describe a problem or ask for help, and experts can respond instantly. This helps solve problems faster, avoid production delays and maintain an efficient workflow.
Frequently asked questions, solutions, operating procedures and processes can be recorded in a knowledge base accessible to anyone, anywhere, anytime. This creates a valuable resource for new recruits, enabling faster training and better assimilation of best practices.
Newcomer training
Store the know-how of outgoing operators
Facilitate knowledge transfer between incoming and outgoing operators and experts by digitizing operational know-how.
You can document in detail the procedures and work instructions used by outgoing operators. You can create step-by-step guides, including descriptions, images, videos and other visual resources to illustrate best practices and specific knowledge. This enables outgoing operators’ know-how to be captured accurately and comprehensively.
Picomto offers a knowledge base function, enabling you to store all important information concerning procedures, best practices, tips and recommendations. This knowledge base is accessible to your entire team, and can be configured according to profiles, enabling outgoing operators to preserve and share their know-how in a centralized, organized way.
Picomto makes it possible to integrate videos and images into procedure documentation. Outgoing operators can create explanatory videos demonstrating best practices, or images showing specific steps in the process. These visual resources are effective ways of conveying outgoing operators’ know-how in a practical and easily understandable way.
When new operators join your team, Picomto facilitates their training and apprenticeship by making all documented resources and stored knowledge available to them. New operators can consult documentation, access videos and images, and quickly familiarize themselves with established procedures and best practices. This enables the know-how of outgoing operators to be transferred efficiently to new recruits.
Picomto offers a user-friendly interface and an advanced search function. This enables your team to find relevant information in the knowledge base quickly and easily. Outgoing operators can add keywords, tags or categories to make it easier to search and access the specific knowledge they have accumulated over time.
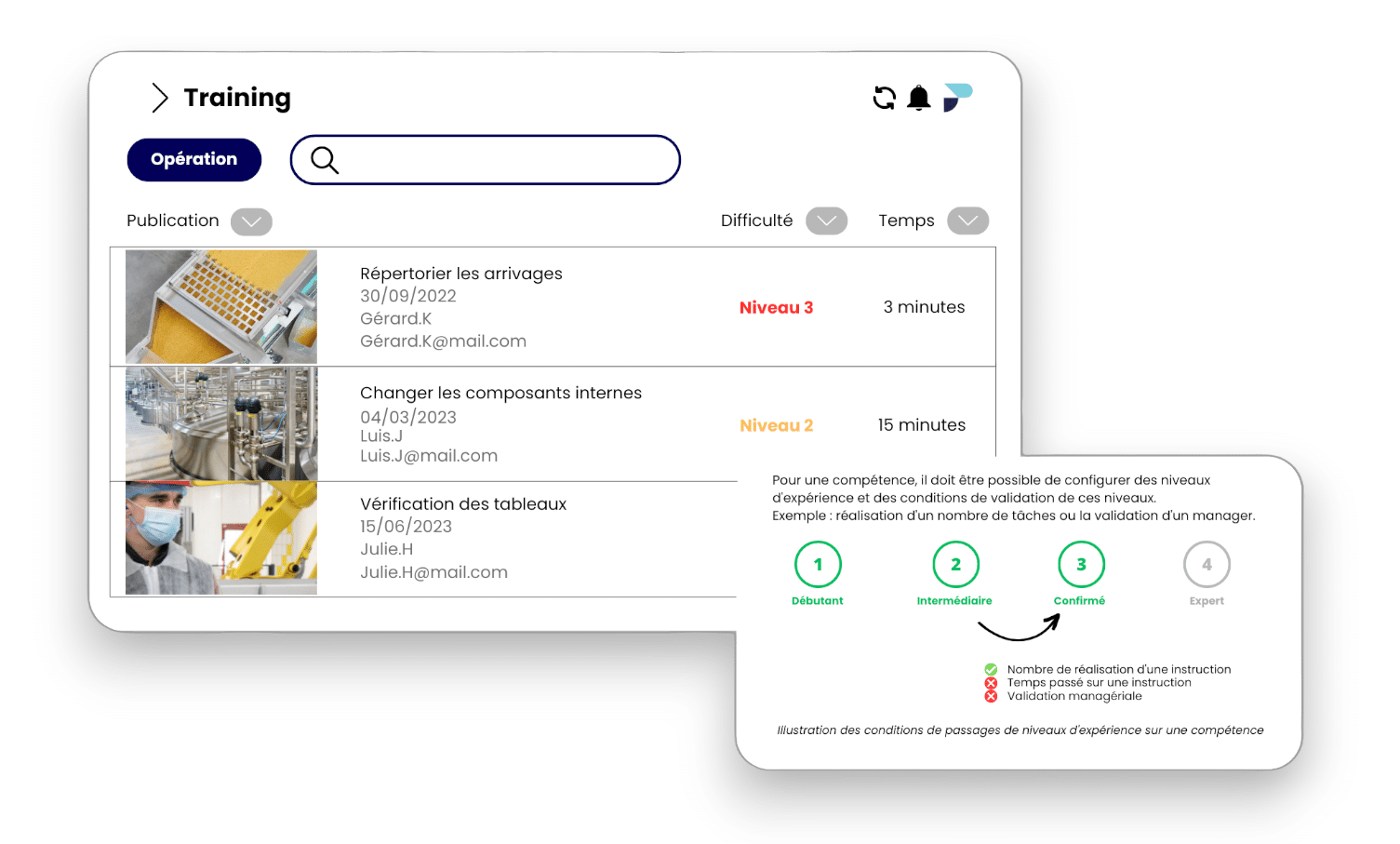
100% FDA 21 CFR Part 11 / GxP compliant solution
Want to find out more?
Download our guide to switching to digital work instructions in the food industry.
We offer you a small booklet to help you digitize your agri-food processes.