Is operational efficiency a major challenge for your industry? In 2024, 67% of industrial companies still struggle to optimize their paper-based processes. McKinsey reveals that improved operational efficiency increases productivity by 25%.
Are your teams wasting time searching for the right work procedures? According to Deloitte, paper-based instructions cause 45% of downtime. Fortunately, solutions like Picomto are transforming this reality. Our clients reduce their errors by 65% through the digitalization of their standard operating procedures.
The key? An intuitive platform that allows you to create, share, and update your procedures in real-time. Teams instantly access the right instructions, even while mobile. Operational efficiency thus becomes a concrete and measurable reality.
Key takeaways:
- Operational efficiency can increase productivity by up to 25%
- Digitalization reduces downtime by 30% on average
- 73% of companies prioritize mobile solutions
- The average ROI for digitalization projects is 18 months
- 92% of operators prefer digital instructions
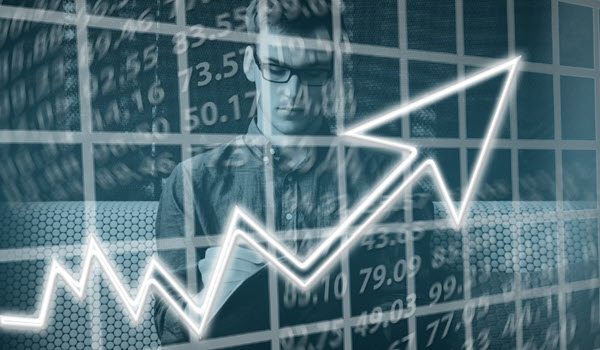
1. The Fundamentals of Operational Efficiency
Operational efficiency has become a strategic imperative for all industrial companies. In a competitive environment, it ensures faster production, better quality at lower costs, while strengthening competitiveness and innovation capacity.
According to McKinsey, operational efficiency can reduce maintenance costs by 10-40%. These results, supported by digitalization and data analysis, reflect a true cultural change.
Beyond the numbers, the goal is to make the best use of resources, maintain production quality, and generate sustainable return on investment.
1.1. Definition and Current Challenges
Operational efficiency aims to maximize the performance of all your industrial processes. It extends to every step, from production to maintenance, and is a priority for 67% of industrialists (Deloitte). This approach reduces waste, streamlines workflows, and improves competitiveness.
- Identify and eliminate waste
Start by analyzing your processes to identify low value-added activities, downtime, or sources of errors. By targeting these points, you quickly optimize your operations.
- Standardize procedures
Creating clear and updated instructions allows teams to follow common standards. This reduces error risks and improves result consistency.
- Leverage digital technology
Digitalization offers better visibility and real-time monitoring of your indicators. By utilizing precise data, you make faster and more reliable decisions, strengthening your operational agility.
- Involve teams
The involvement of operators and managers is essential. By promoting a culture of continuous improvement, each employee contributes to operational excellence.
1.2. Impact on Industrial Performance
The benefits are clear: each operator saves an average of 2.5 hours per day, while digitalization of procedures reduces errors by 85%.
Digital work instructions, always accessible and up-to-date, play a key role in this change.
- Productivity gains
By digitalizing your processes, you eliminate redundant tasks, optimize operations, and improve work flow.
- Quality improvement
Standardized, easily accessible instructions ensure reliable and consistent execution, drastically reducing errors and non-conformities.
Digitalization Serving Operational Efficiency
According to Gartner, 75% of industrial companies will be digitalized by 2025. This digital transition is radically transforming our working methods. Digital tools are thus becoming essential to remain competitive.
2.1. The Importance of Digital Work Instructions
Digital work instructions are at the heart of operational efficiency. Studies show that 90% of errors are avoided through visual procedures. With Picomto, creating and sharing these instructions becomes simple and fast.
- Reduce errors
Visual and standardized instructtions ensure consistent task execution, considerably limiting non-conformities.
- Simplify updates
Thanks to a digital tool, procedure updates are instantaneous, ensuring your teams always have the most recent information.
2.2. Process Automation for Maintenance
Moreover, digital work instructions are at the heart of operational efficiency. Studies show that 90% of errors are avoided through visual procedures. With Picomto, creating and sharing these instructions becomes simple and fast.
- Reduce errors
Visual and standardized instructions ensure consistent task execution, considerably limiting non-conformities.
- Simplify updates
Thanks to a digital tool, procedure updates are instantaneous, ensuring your teams always have the most recent information.
How to Improve Your Operational Efficiency?
Digital transformation is disrupting traditional performance improvement methods. Indeed, the global operational efficiency market will reach $40.6 billion by 2025. This rapid evolution requires constant adaptation from companies.
3.1. Best Practices in Industry 4.0
Process standardization reduces variability and improves operational reliability. The use of visual tools, like Picomto, facilitates operator training and accelerates skill development.
- Standardize for greater consistency
Uniform procedures ensure regular and predictable execution, increasing overall quality.
- Train with visual supports
Digital instructions, clear and illustrated, promote quick understanding, decrease errors, and improve productivity.
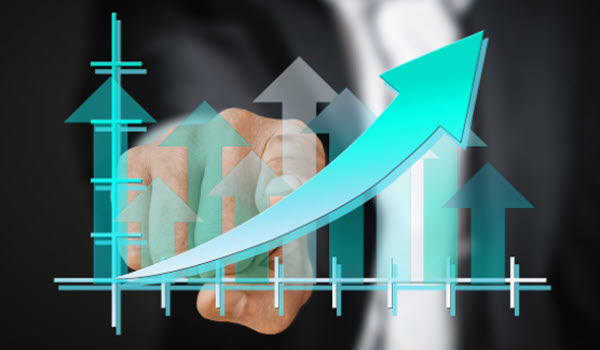
3.2. Visual Management of Procedures
Visual management facilitates instruction understanding and reduces operational errors by 85%. Operators, guided by clear digital instructions, gain autonomy and efficiency.
- Quality improvement
Structured visual instructions ensure more reliable and consistent execution, strengthening production quality.
- Team autonomy
With intuitive digital tools, each operator has a clear and updated guide, thus reducing dependence on supervisors and trainers.
4. Measuring and Optimizing Operational Efficiency
To achieve operational excellence, precise performance measurement is crucial. Companies typically achieve a return on investment of 2 to 5 times their initial investment within 18 months.
This positive impact results from better organization, waste reduction, and process optimization.
4.1. Essential KPIs to Monitor
- Overall Equipment Effectiveness (OEE): Key indicator for evaluating availability, performance, and quality. Digital solutions increase equipment availability by 25%.
- Defect rate: Allows measuring quality and quickly identifying areas for improvement.
- Cycle time: An essential indicator for identifying bottlenecks and streamlining production.
- Inventory levels: Regular monitoring helps reduce capital tied up and improve flexibility.
4.2. Continuous Process Improvement
Continuous improvement saves an average of 15% per year. Thanks to digitalization, data collection and analysis are simpler. Indeed, this allows teams to base their decisions on concrete facts.
Key points
- Automated data collection: Reliable information, gathered in real-time.
- Precise analyses: Clear dashboards to quickly identify areas for improvement.
- Informed decisions: Choices based on evidence, not assumptions.
5. Experience Feedback and Real-world examples
Digital transformation successes are multiplying in industry. For example, Curium reduced its training time by 50%. Pharmaceutical companies optimize their processes through digital instructions.
Explore the Curium case in detail → https://www.picomto.com/clients/curium1/
Conclusion
Operational efficiency is now establishing itself as an essential competitive advantage in industry.
By adopting digital solutions such as Picomto, companies modernize their processes and achieve tangible results: more reactivity, fewer errors, and better profitability. Investment in these tools then becomes an obvious strategic choice to ensure sustainable growth.
FAQ
Q: What is operational efficiency?
A: It’s a company’s ability to produce with minimum resources while maintaining quality.
Q: How to measure operational efficiency ?
A: Essential KPIs are overall equipment effectiveness, unit cost, and quality rate.
Q: What are the main obstacles to operational efficiency ?
A: Obsolete procedures, lack of training, and resistance to change often hinder transformation.
Q: Which digital tools improve operational efficiency ?
A: MES solutions, CMMS, digital instructions, and dashboards, offering real-time monitoring and standardization.
Q: How to involve teams ?
A: Communicate clearly, train regularly, value ideas, provide intuitive tools, establish an improvement culture.
Q: Is digitalization accessible to SMEs ?
A: Yes, scalable, affordable, and evolving solutions, adapted to needs, offering similar gains to large companies.
Q: How to integrate operational efficiency into global strategy ?
A: Align objectives, define relevant KPIs, involve management, spread approach, rely on data to guide decisions.
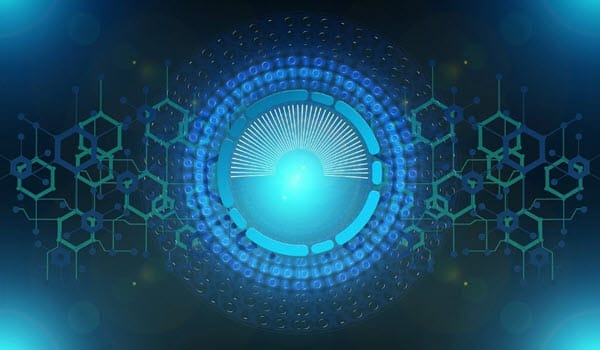
Leave A Comment