What if a simple breakdown could bring your entire production to a standstill? Unplanned downtimes are not only costly but also jeopardize customer satisfaction and your company’s competitiveness. Fortunately, solutions exist.
Adopting the right maintenance strategy can make all the difference. Whether it’s corrective, preventive, or predictive maintenance, each method has its advantages and meets specific needs. This guide will help you explore the different types of maintenance and choose the one that best aligns with your industrial goals. With the right practices, you can minimize breakdowns, optimize costs, and enhance the reliability of your equipment.
Key Takeaways:
- 75% reduction in failures with preventive maintenance.
- 30% cost savings through predictive maintenance.
- 25% reduction in overall expenses with an optimized maintenance strategy.
- 40% efficiency gain through digitalization.
1. What is Industrial Maintenance ?
Industrial maintenance is essential for the smooth operation of modern businesses. It encompasses a wide range of technical actions aimed at keeping equipment operational and preventing malfunctions.
But what are the fundamental principles governing this discipline? Let’s examine them in detail.
1.1. The Fundamentals of Maintenance
Industrial maintenance includes various tasks such as repairs, inspections, and routine adjustments. These interventions are designed to keep equipment in optimal working condition. A well-maintained machine is less prone to failures and performs better over the long term.
Additionally, maintenance helps reduce operating costs by preventing expensive production downtimes.
For instance, replacing a worn-out part before it breaks is far more cost-effective than dealing with prolonged production stoppages. Thus, maintenance is not merely an expense but a strategic investment for any organization.
1.2. Maintenance Objectives
Industrial maintenance goes beyond emergency repairs. In reality, its objectives are diverse and impact multiple aspects of industrial performance:
- Ensuring operator safety: Properly maintained equipment reduces the risk of accidents caused by faulty machines.
- Maximizing machine availability: Reducing production interruptions leads to higher productivity.
- Optimizing production costs: Every euro invested in a well-thought-out strategy can yield up to €3 in savings by avoiding costly repairs and unexpected breakdowns. These savings can be reinvested in continuous process improvements.
2. What Are the Main Types of Maintenance?
Industrial maintenance relies on different approaches tailored to various needs and situations. Each type of maintenance has unique characteristics and benefits, making it essential to understand them to select the most effective strategy.
2.1. Corrective Maintenance
Corrective maintenance is the most reactive method. It is performed only after a breakdown or malfunction occurs.
Its primary goal is to restore equipment functionality as quickly as possible to minimize downtime. However, while common, this approach can lead to high costs, especially in cases of critical or unexpected failures.
Applications of Corrective Maintenance:
Corrective maintenance is ideal when the affected equipment is not critical or when repairs are simple and cost-effective.
It is also suitable when preventive maintenance costs exceed those of corrective intervention. However, to mitigate the impact of failures, strategic planning is crucial. This can include maintaining spare part inventories or training technicians for rapid repairs.
2.2. Preventive Maintenance
Unlike corrective maintenance, preventive maintenance takes a proactive approach. It aims to anticipate failures by scheduling regular interventions based on a predefined preventive maintenance plan. This method is particularly effective in preventing major breakdowns, reducing failures by 75% when properly implemented.
Organizing Preventive Maintenance:
A structured organization is key to a successful preventive maintenance plan. This includes conducting regular inspections and analyzing parameters such as the mean time between failures.
Using a CMMS (Computerized Maintenance Management System) optimizes this process. These tools streamline planning and ensure all necessary interventions are carried out on time.
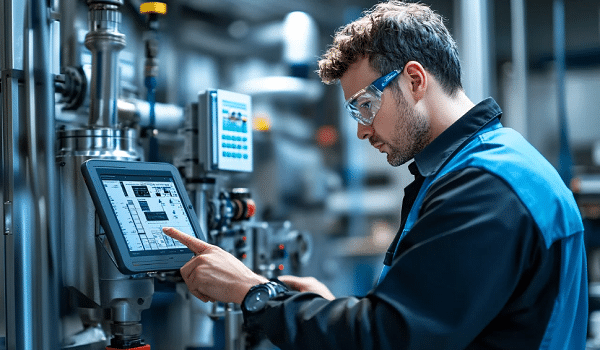
2.3. Predictive Maintenance
Predictive maintenance relies on real-time data analysis to detect anomalies before they lead to failures. This approach, widely used in Industry 4.0, leverages advanced technologies such as artificial intelligence, IoT sensors, and vibration analysis.
Benefits of Predictive Maintenance: This method stands out for its efficiency and ability to cut maintenance costs by 30% while increasing equipment availability. For example, an IoT sensor can monitor a motor’s temperature and signal overheating before it results in a costly breakdown. This enables timely intervention and prevents unplanned downtime.
3. Implementing Maintenance Strategies
Effective maintenance implementation requires methodical planning and strategic decision-making. It must consider your equipment’s specifics, objectives, and available resources.
3.1. Selection Criteria
Choosing the right type of maintenance depends on several key factors:
- Equipment criticality: Machines essential to production require preventive or predictive maintenance to avoid costly interruptions.
- Available budget: Preventive or predictive maintenance may have higher initial costs, but their long-term benefits are significant.
- Company objectives: Reducing downtime, improving productivity, and optimizing costs should guide your overall strategy.
3.2. Planning Interventions
Rigorous planning is crucial for maximizing maintenance efficiency. It optimizes resource use and minimizes unexpected downtime. With modern tools like CMMS, interventions can be scheduled at the right time, based on real equipment needs.
Additionally, good planning ensures balanced task distribution among maintenance teams, preventing workload overloads. Key performance indicators (KPIs) such as failure rates or average repair times should be monitored to refine planning.
3.3. On-Site Execution
The effectiveness of interventions depends on proper execution. Standardizing procedures using clear and precise work instructions reduces errors.
Digital tools, such as mobile applications or connected tablets, facilitate on-site work. They allow real-time tracking of interventions, quick access to equipment data, and accurate logging of completed tasks. This traceability is crucial for performance analysis.
4. Digitalization of Maintenance
Digitalization has revolutionized the way companies manage their maintenance operations. By integrating innovative technologies, organizations can now optimize their processes, reduce costs, and enhance overall efficiency.
Let’s explore the benefits of this transformation and its key enablers.
4.1. Why Digitalize Your Operations?
In the era of Industry 4.0, digitalization has become a cornerstone of maintenance management. Digital tools such as management software and mobile applications help save time on interventions, improve traceability, and accelerate decision-making.
By leveraging centralized data accessible in real time, maintenance managers can quickly identify priorities and coordinate teams more efficiently. This reduces human errors and ensures continuity in equipment management.
4.2. Real-Time Data Analysis
One of the major advantages of digitalization lies in real-time data analysis. IoT sensors, combined with artificial intelligence systems, collect valuable insights on equipment performance. These data points include temperature, vibrations, and wear levels of machines.
This technology not only predicts failures but also optimizes maintenance cycles by scheduling interventions at the right moment. For instance, a sensor can detect a minor anomaly before it escalates into a critical issue, thus preventing costly production downtime.
4.3. Picomto: Your Partner for Digitalized Maintenance
Picomto is an innovative solution dedicated to the digitalization of industrial processes, particularly in maintenance.
With advanced features, Picomto enables companies to create, share, and track digital work instructions accessible in real time from any device.
The benefits are numerous: reduced human errors, improved traceability, and optimized team performance.
By integrating Picomto into your maintenance strategy, you modernize your operations and ensure greater reliability of your equipment.
Conclusion
Maintenance is not just an expense—it is a strategic investment to ensure the sustainability of your production.
By combining the right types of maintenance, planning interventions effectively, and leveraging modern technologies, you can not only reduce costs but also significantly enhance your equipment’s performance.
Moreover, digitalization is an essential lever to simplify processes and reinforce traceability. With tools like Picomto, you gain access to an innovative solution to transform your maintenance operations and drive your company toward operational excellence.
Need personalized advice?
Contact our experts today to modernize your maintenance management and optimize your operations!
FAQ
Q: What are the five types of maintenance?
A: Corrective (repair), preventive (scheduled), predictive (anticipatory), proactive (improvement), and condition-based (monitoring).
Q: What are the different types of corrective maintenance?
A: Palliative maintenance (temporary fix) and curative maintenance (permanent repair).
Q: What is the difference between preventive and corrective maintenance?
A: Preventive maintenance anticipates failures based on a schedule, while corrective maintenance repairs after a failure occurs.
Q: What is the best type of maintenance?
A: A combination of preventive and predictive maintenance offers the best cost-effectiveness for critical equipment.
Q: What is the purpose of maintenance?
A: To ensure equipment availability, optimize costs, and guarantee operator safety.
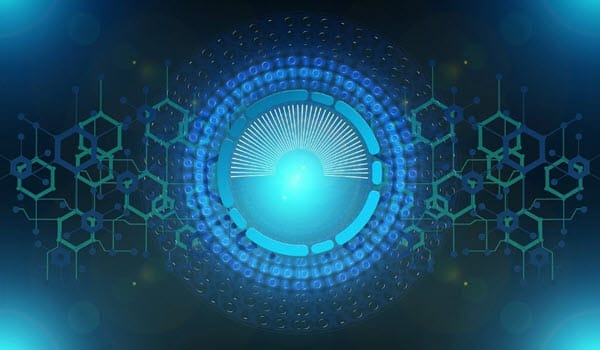
Leave A Comment