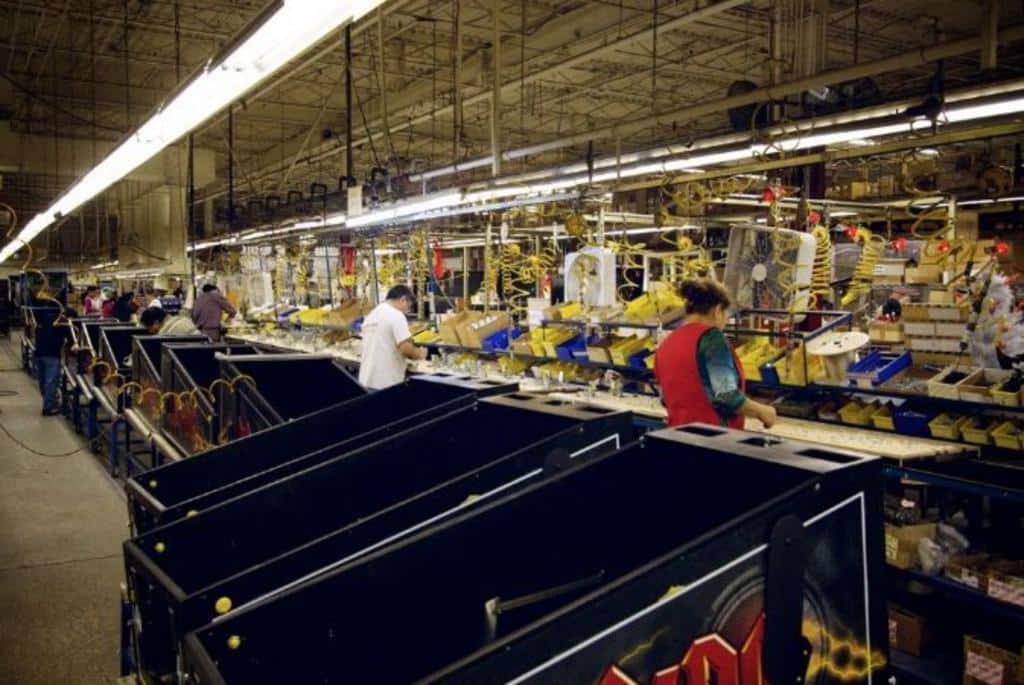
In der Industrie führen Fehler, ob menschlich oder mechanisch, zu Produktfehlern. Letztendlich ist es also die Qualität der Produktion, die sich negativ auf den Grad der Kundenzufriedenheit auswirkt.
Ein globales System im Dienste der Produktionsqualität
Die Fehlerbeseitigung ist eine der Prioritäten eines jeden Unternehmens, wenn es seine Qualitätsziele erreichen will. Die Implementierung eines QMS (Qualitätsmanagementsystem) entspricht genau dieser Logik. Diese Organisation muss jedoch wirklich an die Besonderheiten des Unternehmens angepasst werden, um eine echte Effizienz bieten zu können. Das gleiche QMS-Modell kann für ein Unternehmen perfekt funktionieren und ist überhaupt nicht kompatibel mit einem anderen.
Das QMS umfasst alle menschlichen und materiellen Komponenten, die die Produktionsqualität und die Kundenzufriedenheit beeinflussen können. Es erfordert daher eine starke Beteiligung der Mitarbeiter und eine effektive Führung. Auch dieses System kann nicht profitabel sein, wenn es nicht mit systemorientiertem Management sowie prozess- und faktenbasierten Ansätzen zur Verbesserung der Entscheidungsfindung kombiniert wird. Schließlich vervollständigen die Konzentration auf den Kunden und die Sicherstellung, dass die Beziehungen zu den Lieferanten für beide Parteien von Vorteil sind, die Liste der Elemente, die den Erfolg des QMS bestimmen.
Handeln Sie stromaufwärts, indem Sie verhindern, dass ein Fehler auftritt.
Das Auftreten eines Fehlers zum einen ist fast unvermeidlich, wenn kein absolut zuverlässiger (robuster) Prozess vorhanden ist, um ihn zu verhindern.
Der Poka Yoké ist ein Anti-Fehler-System oder „Codierer“, das entwickelt wurde, um diese Anomalien in der Branche zu verhindern. Es nimmt Änderungen am Produktionsprozess, am Arbeitsplatz und an den Produktionsmitteln vor, um Fehler zu vermeiden. In der Industrie gibt es verschiedene Formen von Poka Yoké-Geräten, wie z.B. die Schaffung von Asymmetrien in Halterungen oder Schablonen, die den Bediener zwingen, das Teil richtig zu platzieren, oder die Installation eines Alarms, wenn eine Anlaufbedingung nicht erfüllt ist.
Die FMECA (Failure Mode, Effects and Criticality Analysis) ihrerseits ermöglicht es, Verbesserungsmaßnahmen zu priorisieren, indem sie eine Kritikalitätsordnung definiert (Produkt aus der Wahrscheinlichkeit des Auftretens eines Unfalls und der Schwere seiner Auswirkungen). Es besteht darin, durch einen Brainstorming-Prozess, an dem alle Abteilungen des Unternehmens beteiligt sind, die Fehler zu identifizieren, die in jeder Phase der Produktion auftreten können, und vorbeugende Maßnahmen zu ihrer Vermeidung festzulegen.
Ein ebenso kollaborativer Ansatz, die 8D-Methode empfiehlt die Einrichtung von 8-Schritte-Blättern, um die Ursachen von Fehlern zu beheben:
- Definieren Sie die Arbeitsgruppe,
- beschreiben Sie das Problem,
- definieren Sie sofortige Korrekturmaßnahmen,
- bestimmen Sie die tatsächlichen Ursachen des Problems,
- bestimmen Sie Korrekturmaßnahmen,
- implementieren und validieren Sie Korrekturmaßnahmen,
- bestimmen Sie vorbeugende Maßnahmen
- gratulieren Sie der Arbeitsgruppe (die 8. „D“: sagen Sie danke).
Eine weitere Qualitätsmethode, das Ishikawa-Diagramm, basiert auf einer grafischen Darstellung der Ursachen, die zu einem Effekt führen. Diagramm in Form von Fischknochen, es ist um 5 Zweige gegliedert (im Fachjargon Industrie 5M genannt): das Material, die Ausrüstung, die Methode, die Arbeit und die Umwelt. Das resultierende Diagramm platziert die direktesten Ursachen näher an der Mittelkante, um sie hervorzuheben.
Verbesserung der Produktion durch effizientere Instandhaltung
Ohne leistungsstarke Maschinen ist eine nachhaltige Produktion nicht möglich. Dazu sind Wartungsarbeiten unerlässlich. Es reicht nicht mehr aus, Fehlfunktionen und Ausfälle von Maschinen zu verhindern, um sie in Funktion zu halten. Ziel ist es auch, die Leistung zu steigern. Auf diesem Prinzip basiert die Total Productive Maintenance (TPM), ein Ansatz, der durch eine stärkere Beteiligung der Betreiber gekennzeichnet ist.
Es ist in der Tat ein Ansatz, der diejenigen, die direkt mit den Maschinen arbeiten, einlädt, zu ihrer Wartung beizutragen, denn sie kennen sie am besten. Total Productive Maintenance fordert den Geist der Initiative und Analyse des Bedieners auf, um die Leistung der Produktionswerkzeuge zu verbessern.
Erkennt er einen Mangel an der Maschine, weiß er, wie man ihn behebt oder kann er an der Lösung mitwirken, muss er vom Zuhören seiner Vorgesetzten profitieren können. Letztendlich profitiert das Unternehmen als Ganzes von dieser vom TPM empfohlenen Art von Feedback.
Leave A Comment