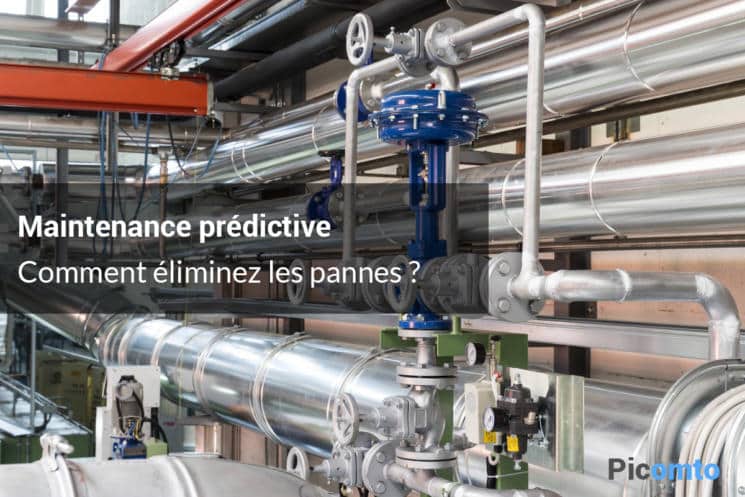
Disposer d’une usine avec zéro panne est l’idéal de tout industriel. Pour l’atteindre, la stratégie de maintenance privilégiée est celle dite prédictive. Allant plus loin que celles curative et même préventive, la maintenance prédictive repose sur une surveillance permanente des machines rendue possible par les nouvelles technologies, notamment celles relevant de l’IIOT. Il s’agit de prévoir et d’anticiper les pannes et défaillances en s’appuyant sur la récolte d’un maximum de données et d’en assurer l’analyse au service de la prise de décision. L’usine du futur mise grandement sur cette maintenance prédictive.
Maintenance prédictive : aller au-delà des maintenances curative et préventive
Les machines ne sont pas éternelles, leurs composantes non plus. Ces dernières finissent inéluctablement par s’user au bout d’un certain nombre d’heures de fonctionnement, de tours ou de passages. Elles doivent donc être remplacées aux moments opportuns pour que les équipements dont elles font partie ne soient pas endommagés et ne perdent pas de leurs performances. De celles-ci dépend la compétitivité de l’entreprise.
Alors que, par le passé, on avait plutôt tendance à intervenir lorsque les pannes survenaient, cette méthode de maintenance curative a progressivement cédé du terrain par rapport à une approche préventive. Il s’agissait alors de planifier des actions de maintenance à intervalles réguliers, en fonction des délais moyens prévus avant la survenue de défaillances.
Si la maintenance préventive a encore sa place dans bien des secteurs et avec des types de machines spécifiques, on lui préfère souvent la maintenance prédictive, qui pousse la logique du « mieux vaut prévenir que guérir » encore plus loin. Elle consiste à assurer une surveillance permanente des équipements, notamment à travers des capteurs placés dans ou sur ses différentes composantes, dans le but de détecter les signes annonciateurs de pannes.
Le principal intérêt que présente la maintenance prédictive est qu’elle promet de réduire significativement les arrêts de production non planifiés, surtout lorsque les techniques utilisés sont non-invasives (capteurs qui ne sont pas placés à l’intérieur des machines et ne nécessitent donc pas d’en interrompre le fonctionnement). Ce qui constitue un gage d’amélioration de la productivité.
Quels moyens mis en œuvre pour la maintenance prédictive ?
Les données sont au centre de la maintenance prédictive. C’est leur recueil et leur analyse qui permettent de planifier les interventions et de faire en sorte que la production demeure la plus fluide possible.
Ces informations capitales sont obtenues grâce à des capteurs et les valeurs récoltées sont continuellement comparées à des données de référence pour savoir si les comportements des composantes et des machines sont considérées comme normaux ou, au contraire, sont annonciateurs de pannes.
En identifiant les signes avant-coureurs des pannes industrielles, la maintenance prédictive permet d’agir en amont et d’éviter des arrêts coûteux et non planifiés.
La maintenance prédictive fait ainsi appel à divers outils, dont la GMAO (gestion de la maintenance assistée par ordinateur), les logiciels de supervision et la commande numérique.
Au niveau matériel, les capteurs permettant la collecte de données sont, eux aussi, de natures variées. On retrouve ainsi des instruments de mesure acoustique utilisant les ultrasons et capables de détecter les défauts mécaniques, électriques ou d’étanchéité, les capteurs relevant de la thermographie (surveillance des niveaux de température) ou encore les capteurs d’analyse vibratoire (analyse des vibrations générées, par exemple, par les défauts de serrages ou de courroies).
Ces systèmes produisent donc des quantités considérables de données, ce qui rend leur exploitation délicate. C’est là que les outils apportés par l’IIOT (L’Internet Industriel des Objets) apportent des solutions en faisant remonter les informations des capteurs vers des plateformes de type cloud. Ils permettent également de simplifier la mise en place d’un réseau au sein duquel les moyens de production sont interconnectés et peuvent même communiquer entre eux.
Picomto est une solution de digitalisation d’instructions de travail et développe également un interrupteur connecté intelligent Check2Start pour améliorer l’efficacité de votre parc machine. N’hésitez pas à nous contacter pour en savoir plus sur nos solutions.
Laisser un commentaire