Votre entreprise industrielle fait-elle face à des défis de performance ? Cherchez-vous à optimiser vos processus de manière durable ? L’excellence opérationnelle représente aujourd’hui la clé de la transformation industrielle.
Elle repose avant tout sur l’Optimisation des processus industriels, qui permet de gagner en efficacité, en qualité et en réactivité face aux exigences du marché.
En effet, selon une étude McKinsey, les entreprises qui adoptent cette approche augmentent leur productivité de 20 à 40%.
Pour réussir cette transformation, vous devez comprendre les fondamentaux et maîtriser les outils adaptés. Dans ce guide complet, nous vous accompagnons pas à pas vers l’excellence opérationnelle.
Points Clés à Retenir concernant l’excellence opérationnelle :
- L’excellence opérationnelle transforme durablement la performance industrielle
- Le Lean, le Six Sigma et le Kaizen sont les piliers méthodologiques essentiels
- La digitalisation amplifie les résultats de l’excellence opérationnelle
- L’engagement des équipes est le facteur clé de succès
- Des résultats mesurables : +30% de productivité en moyenne
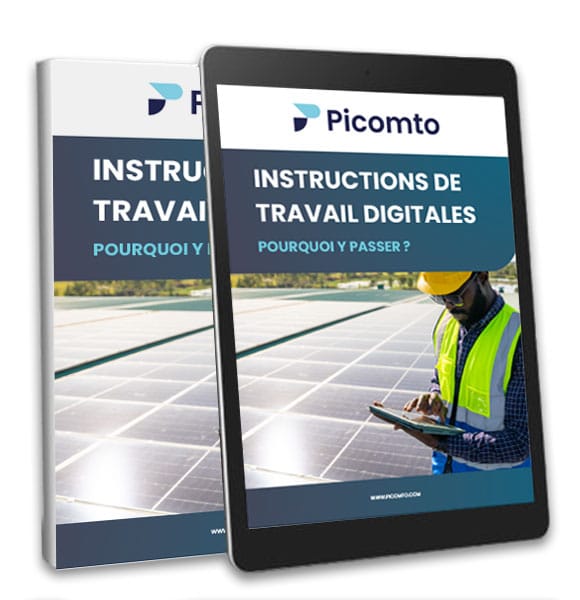
voyages évités chaque semaine
gagnés chaque année
1. Qu’est-ce que l’Excellence Opérationnelle et pourquoi est-elle cruciale aujourd’hui ?
Depuis plus de trois décennies, l’Excellence Opérationnelle transforme radicalement la performance industrielle. Elle combine des méthodologies éprouvées avec les outils digitaux modernes pour optimiser les processus et maximiser la création de valeur.
1.1. Comment définir l’Excellence Opérationnelle dans l’industrie moderne ?
L’Excellence Opérationnelle repose sur l’amélioration continue des processus industriels. Elle vise à éliminer les gaspillages et à optimiser la création de valeur.
Des entreprises de renom ont adopté cette approche avec succès :
- Toyota : Pionnier de cette démarche, Toyota a développé le Toyota Production System (TPS), qui repose sur des principes tels que le « Juste-à-temps » et le « Jidoka » pour améliorer l’efficacité et la qualité de la production.
- Schneider Electric : En mettant en œuvre des initiatives d’Excellence Opérationnelle, Schneider Electric a réussi à réduire ses coûts d’exploitation jusqu’à 30 %, notamment grâce à l’optimisation de ses actifs électriques et à l’amélioration de l’efficacité de ses systèmes.
1.2. Quels sont les enjeux de l’Excellence Opérationnelle pour votre entreprise ?
À l’ère de l’Industrie 4.0, l’Excellence Opérationnelle devient incontournable pour rester compétitif. Les bénéfices sont tangibles :
- Réduction des coûts : Les entreprises adoptant cette démarche constatent une diminution des coûts opérationnels de 15 à 25 %.
- Amélioration de la qualité : Une augmentation de la qualité des produits et services de l’ordre de 30 % est fréquemment observée.
- Satisfaction client accrue : La satisfaction des clients s’améliore de 20 %, grâce à des produits de meilleure qualité et à des délais de livraison optimisés.
2. Quelles sont les méthodologies clés de l’Excellence Opérationnelle ?
Ces approches visent toutes à améliorer les processus, réduire les coûts et augmenter la satisfaction client. Chacune apporte sa contribution unique à l’Excellence Opérationnelle.
2.1. Comment le Lean Management révolutionne-t-il les processus industriels ?
Le Lean Management se concentre sur l’élimination systématique des gaspillages dans les processus. En identifiant et supprimant les activités sans valeur ajoutée, il optimise la production et la qualité. Selon une étude de Deloitte, l’adoption du Lean permet une réduction des coûts de 15 à 20 % et une amélioration de la productivité de 30 %.
2.2. Que peut apporter le Six Sigma à votre démarche d’amélioration ?
Le Six Sigma vise à réduire la variabilité des processus grâce à une approche statistique rigoureuse. Cette méthodologie garantit une qualité constante et prévisible.
General Electric a économisé 12 milliards de dollars en cinq ans grâce à l’implémentation du Six Sigma sous la direction de Jack Welch . De son côté, Motorola a réduit ses défauts de 99,7 % en adoptant cette méthode.
2.3. Comment le Kaizen transforme-t-il la culture d’entreprise ?
Le Kaizen instaure une culture d’amélioration continue à tous les niveaux de l’organisation. Cette philosophie japonaise mobilise l’intelligence collective et les outils d’amélioration continue pour réaliser des améliorations progressives mais durables. En impliquant chaque employé dans l’amélioration des processus, le Kaizen favorise une culture d’entreprise positive et proactive.
3. Quelles sont les étapes clés du déploiement ?
Pour réussir la mise en œuvre de l’Excellence Opérationnelle, il est essentiel de suivre une démarche méthodique :
- Diagnostic approfondi : Évaluez l’état actuel de vos processus pour identifier les points faibles et les opportunités d’amélioration.
- Définition d’objectifs SMART : Établissez des objectifs Spécifiques, Mesurables, Atteignables, Réalistes et Temporellement définis pour orienter vos actions.
- Élaboration d’un plan d’action détaillé : Planifiez les initiatives à mettre en place, en précisant les ressources nécessaires et les échéances.
- Mise en œuvre et suivi : Déployez les actions prévues, en assurant un suivi régulier pour mesurer les progrès et ajuster les stratégies si nécessaire.
Les entreprises qui adoptent cette approche structurée constatent des améliorations significatives, avec des gains de performance pouvant atteindre 30 % supplémentaires.
3.1. Comment obtenir l’adhésion des équipes ?
L’engagement des collaborateurs est déterminant pour le succès de la transformation. Voici quelques leviers pour favoriser leur implication :
- Communication transparente : Informez régulièrement les équipes sur les objectifs, les avancées et les bénéfices attendus.
- Formation continue : Proposez des sessions de formation pour développer les compétences nécessaires à la mise en œuvre des nouvelles pratiques.
- Implication dans le processus : Encouragez la participation active des employés en sollicitant leurs idées et en valorisant leurs contributions.
Par exemple, Michelin a organisé des initiatives telles que la « Digital Week » pour sensibiliser et former ses collaborateurs aux outils digitaux, favorisant ainsi une adoption réussie.
3.2. Quels sont les outils indispensables à maîtriser ?
Les outils digitaux jouent un rôle clé dans l’Excellence Opérationnelle. Parmi eux :
- Instructions de travail digitales : Standardisez les procédures et facilitez leur mise à jour grâce à des supports numériques interactifs.
- Formulaires intelligents : Collectez et analysez les données en temps réel pour une prise de décision éclairée.
- Tableaux de bord dynamiques : Suivez les indicateurs de performance et identifiez rapidement les écarts à corriger.
Des solutions comme Picomto permettent de centraliser ces outils, offrant une interface intuitive pour optimiser les processus et renforcer la qualité.
4. Comment le digital transforme-t-il l’Excellence Opérationnelle ?
La transformation digitale démultiplie les bénéfices de l’excellence opérationnelle. Les nouvelles technologies créent de nouvelles opportunités.
4.1. Quels sont les apports de l’Industrie 4.0 ?
L’Industrie 4.0 connecte les machines, les processus et les opérateurs en temps réel, facilitant une prise de décision rapide et une adaptabilité accrue.
Cette interconnexion repose sur l’intégration des technologies de l’information (IT) et des technologies opérationnelles (OT), rationalisant le flux de données et améliorant l’efficacité globale.
Les avantages clés incluent :
- Suivi en temps réel : Les capteurs IoT et l’analyse de l’IA permettent une surveillance continue des opérations, réduisant les temps d’arrêt et les coûts d’inventaire.
- Maintenance prédictive : L’analyse des données permet d’anticiper les défaillances, optimisant ainsi la maintenance et prolongeant la durée de vie des équipements.
- Amélioration de la productivité : L’intégration des systèmes permet une meilleure allocation des ressources et une augmentation de la productivité.
4.2. Comment les instructions de travail digitales révolutionnent-elles les processus ?
Les instructions de travail numériques standardisent les meilleures pratiques, réduisent les erreurs et accélèrent la formation des opérateurs. Elles offrent une accessibilité et une mise à jour facilitées, garantissant que les employés disposent toujours des informations les plus récentes.
Les bénéfices incluent :
- Réduction des erreurs : Des consignes visuelles et standardisées assurent une exécution cohérente des tâches, limitant considérablement les non-conformités.
- Formation accélérée : Les instructions numériques facilitent l’apprentissage, réduisant le temps de formation et augmentant la qualité du travail.
- Accessibilité améliorée : Les procédures sont accessibles et tenues à jour partout où les employés travaillent, améliorant ainsi la flexibilité et la réactivité.
5. Quels sont les pièges à éviter dans votre démarche ?
L’excellence opérationnelle comporte des défis spécifiques. La connaissance des pièges courants améliore vos chances de succès.
5.1. Quelles sont les erreurs courantes et comment les prévenir ?
Certaines erreurs récurrentes peuvent compromettre vos initiatives d’Excellence Opérationnelle.
Voici les plus fréquentes et les moyens de les éviter :
- Manque d’engagement de la direction : Une implication insuffisante des dirigeants peut entraîner une perte de motivation des équipes. Assurez-vous que la direction soutient activement la démarche et communique clairement les objectifs.
- Objectifs flous ou mal définis : Des objectifs vagues rendent difficile l’évaluation des progrès. Utilisez la méthode SMART pour définir des objectifs Spécifiques, Mesurables, Atteignables, Réalistes et Temporellement définis.
- Communication inefficace : Une mauvaise communication peut créer des malentendus et des résistances au changement. Établissez un plan de communication clair et assurez-vous que les informations circulent efficacement à tous les niveaux de l’organisation.
- Formation inadéquate des équipes : Des employés non formés peuvent mal appliquer les nouvelles procédures. Investissez dans la formation continue pour garantir que chacun comprend et maîtrise les outils et méthodes mis en place.
- Multiplication excessive des indicateurs : Trop d’indicateurs peuvent diluer l’attention et compliquer le pilotage. Concentrez-vous sur un nombre restreint de KPIs pertinents alignés sur vos objectifs stratégiques.
5.2. Comment mesurer le succès de votre démarche ?
La mesure régulière de la performance est essentielle pour ajuster votre stratégie et assurer le succès de votre démarche d’Excellence Opérationnelle.
Voici comment procéder :
- Définir des KPIs pertinents : Choisissez des indicateurs clés de performance adaptés à vos objectifs. Par exemple :
-
- Taux de rendement global (TRG) : Mesure l’efficacité de vos équipements.
-
- Délai moyen de traitement : Évalue la rapidité de vos processus.
-
- Taux de satisfaction client : Indique la qualité perçue de vos services ou produits.
- Mettre en place des tableaux de bord : Utilisez des outils de visualisation pour suivre vos KPIs en temps réel et faciliter la prise de décision.
- Analyser régulièrement les données : Planifiez des revues périodiques pour interpréter les résultats, identifier les écarts et mettre en œuvre des actions correctives.
- Impliquer les équipes : Partagez les résultats avec vos collaborateurs pour les engager dans une démarche d’amélioration continue.
En suivant ces étapes, vous pourrez non seulement éviter les pièges courants mais aussi instaurer une culture de performance durable au sein de votre organisation.
Conclusion
L’excellence opérationnelle transforme durablement la performance industrielle. La combinaison des méthodologies éprouvées et des outils digitaux crée un avantage compétitif décisif. Picomto accompagne votre transformation avec des solutions digitales innovantes. Nos experts vous guident à chaque étape.
Commencez votre transformation vers l’excellence opérationnelle !
FAQ
Q: Comment définir l’excellence opérationnelle ?
R: L’excellence opérationnelle est une démarche d’optimisation continue des processus, méthodes et outils pour maximiser la performance globale.
Q: Quels sont les outils d’excellence opérationnelle ?
R: Les principaux outils sont le VSM, le 5S, le SMED, les instructions de travail digitales et les tableaux de bord KPI.
Q: Quelles sont les méthodes d’excellence opérationnelle ?
R: Les méthodes essentielles sont le Lean Management, le Six Sigma, le Kaizen et le management visuel.
Q: C’est quoi la performance opérationnelle ?
R: La performance opérationnelle mesure l’efficacité des processus à travers la productivité, la qualité et les coûts.
Q: Quels sont les outils du lean ?
R: Le Lean utilise le 5S, le Kanban, le PDCA, le Poka-Yoke et le management visuel.
Q: Combien de temps faut-il pour voir des résultats ?
R: Les premiers résultats apparaissent après 3-6 mois avec une mise en œuvre structurée.
Q: Quel est le rôle du digital dans l’excellence opérationnelle ?
R: Le digital automatise les processus et facilite le partage d’informations en temps réel.
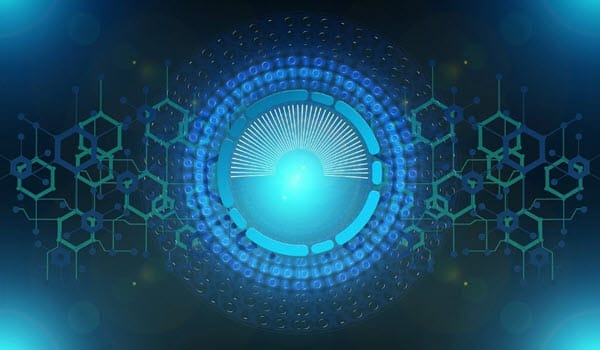
Merci pour cet article très complet sur l’excellence opérationnelle ! J’apprécie particulièrement la façon dont vous avez expliqué les outils pratiques et les fondements qui la sous-tendent. Cela m’a donné de nouvelles perspectives pour améliorer l’efficacité au sein de mon équipe. Hâte de lire plus sur ce sujet !
Cet article sur l’excellence opérationnelle est vraiment éclairant ! J’ai particulièrement apprécié les exemples pratiques des outils mentionnés. Cela aide à mieux comprendre comment appliquer ces concepts dans un contexte réel. Merci pour ce partage utile !
Merci pour cet article éclairant sur l’excellence opérationnelle ! J’apprécie particulièrement la façon dont vous avez abordé les différents outils. Cela m’encourage à appliquer ces concepts dans mon propre travail. Hâte de lire vos prochains billets sur ce sujet !
Merci pour cet article éclairant ! J’apprécie la clarté des définitions et la présentation des outils liés à l’excellence opérationnelle. Cela apporte une vraie valeur ajoutée pour ceux d’entre nous cherchant à optimiser nos processus. Hâte de lire plus sur les cas pratiques de mise en œuvre !
Merci pour ce guide complet sur l’excellence opérationnelle ! Les conseils pratiques et les études de cas sont vraiment utiles pour améliorer la performance industrielle. J’ai particulièrement apprécié la section sur l’implication des employés. Hâte d’appliquer ces stratégies dans mon entreprise !
Merci pour cet article instructif sur l’excellence opérationnelle ! J’ai particulièrement apprécié les exemples concrets que vous avez partagés. Cela m’a donné de nouvelles idées pour améliorer la performance dans notre usine. Hâte de lire vos prochains articles !