Lorsqu’il est arrivé dans l’industrie, le Lean tel qu’il était pratiqué à l’époque était très prometteur. Les améliorations qu’il apportait dans plusieurs secteurs des entreprises permettaient d’atteindre des niveaux de productivité et de qualité très intéressants, mais ce modèle a quelque peu perdu de sa superbe au fil des années. Non pas qu’il soit devenu foncièrement désuet, mais c’est surtout que, bien souvent, dans sa mise en œuvre, il n’a pas suivi les évolutions générées par l’intégration des nouveaux outils digitaux et méthodes de production, de management et de communication.
En d’autres termes, l’environnement interne comme celui externe au sein desquels vivent les entreprises industrielles ont connu de profondes mutations avec la dématérialisation et de la numérisation tous azimuts. Une tendance de la transformation digitale à laquelle le Lean a dû s’adapter, d’où la naissance du Lean Digital. De quoi s’agit-il et qu’implique son intégration ?
Ebook
Prêt à intégrer le Lean Digital dans votre entreprise ?
Découvrez nos solutions pour optimiser vos processus grâce à la digitalisation.
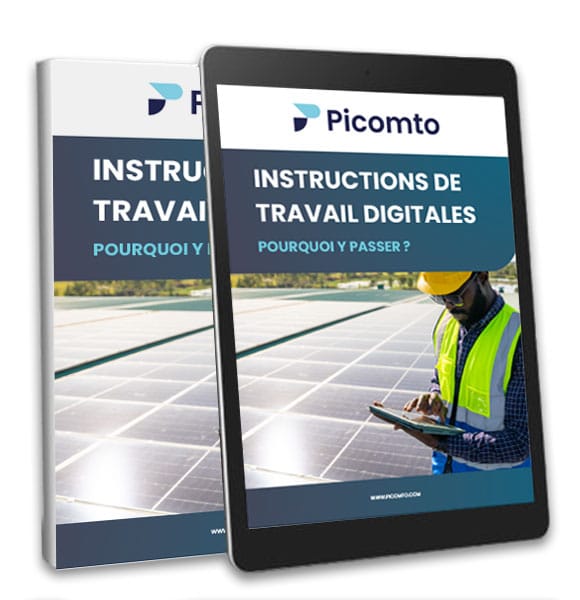
voyages évités chaque semaine
gagnés chaque année
1. Quelles différences entre le lean management traditionnel et digital ?
1.1. La naissance du Lean Digital
Le Lean Management traditionnel est une méthode de gestion et d’organisation du travail. Son objectif principal est d’améliorer les performances d’une entreprise.
Développée dans les années 1960 par Taiichi Ono pour Toyota, cette méthode a connu un grand succès en réduisant les activités non rentables.
Cependant, le Lean traditionnel peut être mal adapté aux nouvelles entreprises digitales. En effet, il ne s’ajuste pas toujours aux outils digitaux modernes ni aux nouvelles méthodes de production, de management et de communication.
Pour s’adapter aux mutations de la quatrième révolution industrielle, le Lean traditionnel a évolué vers le Lean Digital.
1.2. Les bases du lean manufacturing en quelques mots
L’efficacité du Lean Management sur la productivité dans les usines est bien établie. En résumé, cette méthodologie vise à améliorer la performance en se concentrant sur deux axes : l’élimination du gaspillage (temps, énergie, pannes, superflu) et l’amélioration continue des processus.
Avant tout, le Lean est une culture centrée sur l’humain. Pour atteindre ses objectifs et améliorer les conditions de travail des employés tout en apportant une valeur ajoutée au client, le Lean Manufacturing repose sur plusieurs fondements.
Voici cinq éléments jugés particulièrement importants :
- Le Challenge : Porté par le lean manager, ce défi aide les équipes à comprendre les enjeux de l’entreprise et à s’engager sur une vision à long terme.
- Le Respect : Cette règle d’or favorise la créativité des employés. Écouter et communiquer en toute transparence lors des rituels est primordial.
- Le Kaizen : Signifiant « changement pour le meilleur », le Kaizen encourage chaque membre de l’équipe à identifier et améliorer les processus quotidiennement.
- Les Gemba Walks : Ces « tours de terrain » permettent aux managers d’observer directement le fonctionnement sur place, facilitant ainsi la détection des problèmes.
- Le Travail d’Équipe : C’est la pierre angulaire des projets et des processus d’amélioration continue. L’évolution, l’apprentissage et l’amélioration se font ensemble.
1.3. Le lean digital
Le Lean Digital intègre des outils numériques avancés pour identifier les problèmes de production. Cela inclut la détection des gaspillages, la surproduction, et les rebuts machines.
Grâce à la modélisation numérique des flux, des équipements et des sites de production, ainsi qu’à l’exploitation du Big Data, le Lean Digital adopte une large gamme d’outils innovants. Ces outils permettent de simuler des flux, de créer des scénarios tests, de réaliser une planification digitale, et d’effectuer des évaluations financières virtuelles.
En conclusion, le Lean Digital optimise la chaîne de valeur de production. Il intègre des technologies modernes tout en respectant les principes du Lean traditionnel. Cette évolution est cruciale pour faire face aux défis actuels du secteur.
Améliorez vos processus avec le Lean Digital. Participez à notre webinar pour découvrir comment la digitalisation peut transformer votre relation-client.
2. Le digital pour l’amélioration continue des processus
Dans l’industrie d’aujourd’hui, le suivi du fonctionnement des machines n’a plus rien à voir avec ce qu’il était dans un passé pourtant relativement récent (de l’ordre de quelques années).
Le Big Data s’est largement répandu, amenant les entreprises à brasser des quantités massives de données et à les exploiter pour réaliser différentes démarches tels que la maintenance productive totale (TPM (Maintenance Productive Totale)), grâce à l’analyse poussée desdites données. Les pannes sont mieux prédites et les opérations mieux organisées et exécutées à la faveur de moyens logiciels performants.
La numérisation des entreprises intervient également au niveau de l’amélioration des processus, rendant possibles leur modélisation et leur simulation en concevant de multiples scénarios. Ce qui permet de mettre en place les mesures correctives adéquates, notamment en éliminant les lenteurs, les gaspillages et les non-conformités. Au final, les processus deviennent encore plus aptes à soutenir la productivité et la compétitivité, ce qui renvoie à l’un des principes fondamentaux du Lean (améliorer le processus de production).
Découvrez comment Daher a réussi à valoriser ses équipes grâce au Lean Digital. Lisez notre étude de cas pour en savoir plus.
3. La relation-client boostée par la transformation numérique
L’approche Lean implique aussi d’assurer l’amélioration de l’expérience-client, d’une part en lui fournissant un produit de qualité et conforme à ses attentes, et d’autre part en renforçant le lien avec lui par l’intermédiaire du digital.
Le Lean Digital entend exploiter le maximum des potentialités qu’offrent les outils numériques en termes d’accroissement de la qualité. Par l’optimisation des processus citée plus haut, on a moins de risque de se retrouver, en bout de chaîne, avec un produit comportant un défaut, une non-conformité.
Parallèlement, les échanges entre le fabricant et le client s’intensifient considérablement grâce à une proximité accrue permise par Internet et les applications mobiles. Les entreprises peuvent, en effet, collecter des informations cruciales quant aux préférences des clients, leurs comportements d’achat, leurs tendances consommateurs, leurs attentes, etc.
4. La valorisation du facteur humain dans l’entreprise
Le Lean Digital suppose, enfin, une meilleure prise en compte du capital humain de l’entreprise, de la formation au façonnement des postes de travail.
Il encourage la valorisation des équipes en les dotant d’outils novateurs et en favorisant chez elles à la fois le sentiment d’appartenance à l’organisation et la volonté de porter le projet commun.
La digitalisation du Lean Management, c’est aussi la dématérialisation du management visuel, avec l’analyse approfondie et l’affichage en temps réel des indicateurs clés de performance (KPI) sur des solutions d’affichage dynamiques (écrans).
En résumé, le Lean Digital reprend les piliers de Lean traditionnel en soutenant l’amélioration continue à tous les niveaux et en usant des nouvelles possibilités offertes par la technologie.
Transformez vos processus avec Picomto, la solution dédiée à l’amélioration continue et au Lean Digital.
5. Quels sont les enjeux du lean digital ?
Le lean digital représente une évolution essentielle pour les entreprises cherchant à améliorer leur efficacité et leur réactivité dans un environnement en constante mutation.
Voici les principaux enjeux associés à cette démarche.
- Améliorer la communication
Les innovations digitales sont désormais ancrées dans le quotidien des collaborateurs. Étant des « digital natives », les générations actuelles ont des compétences technologiques qui peuvent être exploitées par les entreprises.
Pour tirer parti de ces nouvelles compétences, il est crucial de mettre en place des solutions de communication modernes, intuitives et plus efficaces que la traditionnelle messagerie électronique.
Par exemple, des applications intuitives peuvent remplacer des logiciels obsolètes ou peu performants dans le secteur industriel. Ce type d’outil permet aux collaborateurs de rester informés en temps réel sur les flux de travail, favorisant ainsi le partage d’informations immédiat.
Cette transparence motive les équipes, renforce leur engagement et constitue un véritable levier de performance.
De plus, le management visuel, en rendant les informations visibles et accessibles, s’avère être un atout précieux pour l’apprentissage et la formation des nouveaux employés. Cela leur permet de s’intégrer plus rapidement et efficacement.
- Optimiser la productivité
L’optimisation de la productivité des collaborateurs, des processus et des équipements demeure au cœur du lean manufacturing. La digitalisation des entreprises a pour objectif de générer des gains de productivité significatifs grâce à plusieurs stratégies :
- Standardisation des procédés : En uniformisant les méthodes de fabrication, les contrôles et les alertes, les entreprises peuvent réduire les variations et les erreurs.
- Utilisation d’applications simples et collaboratives : Ces outils offrent une vision globale des flux, facilitant ainsi la coordination entre équipes et le suivi des tâches.
- Collecte de données opérationnelles : La mise en place de systèmes de collecte permet d’analyser des données en temps réel, ce qui est essentiel pour une prise de décision éclairée.
- Mesures d’indicateurs de performance pertinents : Un suivi efficace des KPI permet de résoudre rapidement les problèmes identifiés.
- Proactivité des équipes : La transparence et la fluidité des informations, associées à des Animations à Intervalle Court (AIC), encouragent les équipes à prendre des initiatives et à s’impliquer davantage.
En somme, cette méthodologie digitalisée ne se limite pas à l’amélioration des processus. Elle favorise également une meilleure implication du personnel, ce qui, in fine, renforce la compétitivité de l’entreprise.
- Atteindre l’excellence opérationnelle
L’exploitation de données digitales plus nombreuses, précises et facilement compilables permet aux managers d’atteindre une excellence opérationnelle. Grâce à ces outils, ils peuvent :
- Avoir une vue d’ensemble des workflows : Cela facilite la compréhension du fonctionnement des équipes et des processus.
- Développer des routines de suivi : La mise en place de routines permet de garantir une gestion cohérente et efficace des tâches.
- Pérenniser et historiser les savoir-faire : La documentation des processus et des expériences inter-équipes assure la continuité des connaissances au sein de l’organisation.
- Prendre des décisions rapides et efficaces : Avec l’aide des AIC, les managers peuvent agir rapidement face aux défis, sans perdre de temps dans des processus décisionnels lourds.
- Standardiser les processus de fabrication : Cela permet d’assurer la qualité et la cohérence des produits tout en réduisant les coûts.
En conclusion, les enjeux du lean digital sont multiples et interdépendants.
En améliorant la communication, en optimisant la productivité et en visant l’excellence opérationnelle, les entreprises peuvent s’adapter aux exigences du marché. Elles peuvent aussi anticiper les évolutions futures. Cette approche intégrée est essentielle pour rester compétitif dans un monde de plus en plus digitalisé.
6. Quelles sont les étapes pour mettre en place un management visuel digital ?
La mise en place d’un management visuel digital nécessite une approche structurée. La première étape consiste à établir un pilote afin de tester le concept en conditions réelles, mais sur une échelle réduite.
À l’issue de cette phase, un bilan permettra de décider si le concept doit être généralisé à plusieurs lignes ou au sein d’un site, ou s’il faut l’abandonner.
6.1. Définir une équipe pilote
Il est essentiel que la démarche Lean transcende les frontières interservices. Ainsi, votre équipe doit être constituée de membres issus de divers horizons pour obtenir des points de vue variés. La difficulté réside dans la constitution d’une équipe représentative tout en maintenant un effectif limité.
Par exemple, vous pourriez former une équipe pilote incluant un représentant de l’équipe qualité, de la maintenance, de la logistique, etc. Cette diversité permettra d’enrichir les discussions et de trouver des solutions adaptées.
6.2. Définir vos objectifs à atteindre
Il est crucial de définir des objectifs précis afin d’organiser votre suivi quotidien ou hebdomadaire sur les indicateurs que vous aurez choisis. Ces objectifs peuvent inclure :
- Gain de temps sur des tâches de travail, comme la réduction du temps consacré aux réunions.
- Réactivité des équipes face aux problèmes.
- Autonomie dans la résolution des problèmes, permettant aux équipes de gérer elles-mêmes certaines situations.
La clarté des objectifs facilitera le suivi de la performance et l’évaluation des progrès.
6.3. Intégrer ce management dans des routines et rituels quotidiens
Le choix des indicateurs clés de performance (KPI) est une étape déterminante pour optimiser la résolution de problèmes. Il est important de prioriser ces indicateurs afin de ne retenir que ceux qui sont essentiels, évitant ainsi la surcharge d’informations.
Par exemple, vous pourriez suivre le taux de rebut machine ou le nombre de jours sans accidents. Ces indicateurs doivent être pertinents et directement liés aux objectifs que vous avez fixés.
6.4. Mesurer, analyser, progresser
Finalement, après quelques semaines d’implémentation, il sera temps de tirer les leçons de votre démarche Lean Digital.
L’analyse des mesures effectuées doit vous permettre d’identifier clairement les aspects positifs et négatifs du processus. Cette évaluation vous aidera à améliorer le concept, à décider de sa reconduction, de sa généralisation ou de son abandon.
Grâce au Lean Digital, vous obtiendrez une vision globale des objectifs visés et atteints à la fin de la phase pilote.
En conclusion, chaque étape est essentielle pour garantir une mise en œuvre réussie du management visuel digital. Cette méthode permet d’optimiser les processus tout en favorisant une culture d’amélioration continue au sein de l’organisation.
6.5. Utiliser un outil de Lean Digital
Picomto, solution pour digitaliser les instructions de travail, est une composante da méthodologie du Lean Digital. Elle favorise l’amélioration continue en redonnant un outil aux opérateurs et techniciens pour les aider dans la réalisation de leur tâche et faciliter la collecte de données terrain.
FAQ
Comment mesurer l’efficacité d’une approche Lean Digital ?
L’efficacité peut être mesurée à l’aide d’indicateurs clés de performance (KPI), tels que le taux de productivité, le temps de réponse aux problèmes et la satisfaction des employés.
Quelle est la différence entre Lean traditionnel et Lean Digital ?
Le Lean traditionnel se concentre sur l’élimination des gaspillages et l’amélioration continue, tandis que le Lean Digital intègre des technologies numériques pour moderniser et optimiser ces processus.
Le Lean Digital nécessite-t-il des investissements importants ?
Les investissements varient selon les outils et technologies choisis. Cependant, les gains de productivité et d’efficacité réalisés peuvent compenser ces coûts à long terme.
Quels secteurs peuvent bénéficier du Lean Digital ?
Pratiquement tous les secteurs peuvent en bénéficier, notamment l’industrie, les services, la santé et la logistique, où l’optimisation des processus est cruciale.
Quels indicateurs clés de performance (KPI) sont les plus pertinents pour le Lean Digital ?
Des KPI tels que le taux de rendement global (OEE), le temps de cycle, le coût par unité produite et la satisfaction client sont essentiels pour évaluer l’efficacité des initiatives Lean Digital.
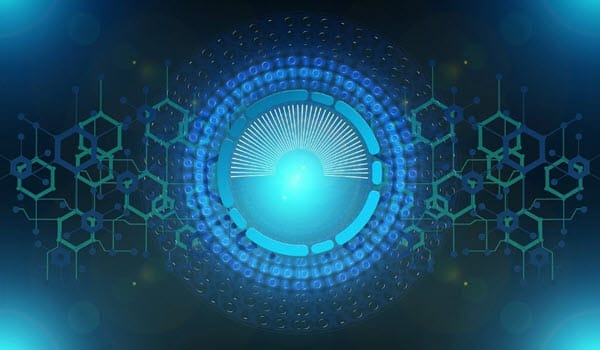
Laisser un commentaire