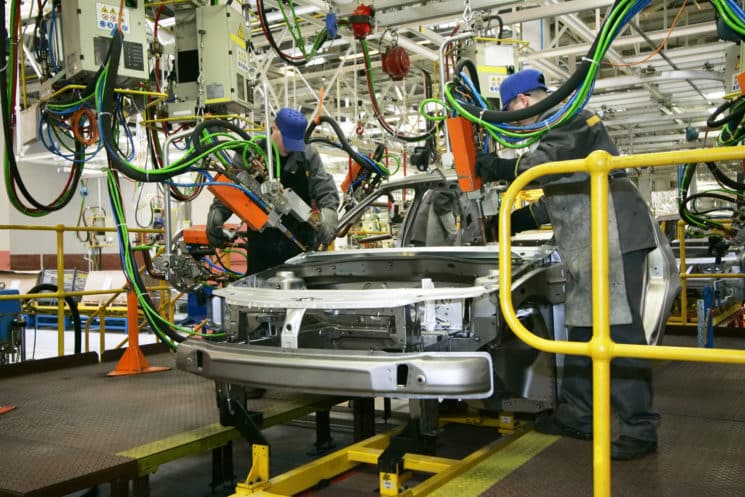
La chasse aux gaspillages, sous toutes leurs formes, est au cœur des stratégies de production, car ils constituent autant de freins à la performance. Les pertes de temps font partie de ces aspects sur lesquels les responsables concentrent leurs efforts afin d’en réduire l’étendue, car elles sont particulièrement pénalisantes. Elles existent notamment lors des changements de séries, qui comportent des opérations inévitables, surtout dans un contexte où la production doit être la plus flexible possible pour répondre à une demande changeante. La réduction de ces temps de changements de séries représente donc un défi majeur et la méthode SMED a justement été élaborée pour le relever.
Les temps de changements de série : de quoi s’agit-il ?
Prenons l’exemple d’une machine qui permet de fabriquer un même produit, mais en plusieurs références avec, pour chacune d’elles, des caractéristiques différentes, comme le diamètre de la pièce. Passer de la production d’une référence à une autre, donc le même type de produit mais avec un calibre plus grand ou plus petit, implique de changer le moule, le gabarit ou les outils. La machine doit être arrêtée pendant un certain temps pour procéder à ces réglages, ainsi qu’à d’autres opérations nécessaires (refroidissement de la machine, nettoyage éventuellement…). C’est cet intervalle de temps, celui de changement de série et durant lequel l’équipement est immobilisé, qui pose problème et qui, s’il est trop important et/ou trop fréquent, freine la productivité et la performance.
Pour réduire ces changements et les coûts qu’ils génèrent, le réflexe a longtemps consisté à privilégier les productions en grandes séries, mais cette manière de faire a ses limites, à commencer par le fait que, bien souvent, les non-conformités ne sont décelés qu’à un stade avancé de la chaîne de production, lorsque la correction est la plus problématique, voire impossible.
Il s’agit donc de trouver un compromis entre la nécessité de produire mieux et avec un minimum d’interruption, et celle d’adapter sa production à la demande, aussi bien en quantité qu’en variabilité (produits plus personnalisés, étant l’une des grandes tendances de la demande actuelle).
Les origines de la méthode SMED
La méthode SMED (single-minute exchange of dies / changement de matrices en une seule minute) a justement pour objectif de répondre à ce véritable challenge en gestion de production qu’est la réduction des temps de changements de série.
Développé par Shingeo Shingo pour Toyota à partir du début des années 1950, ce concept a nécessité une vingtaine d’années de travail et de réflexion de la part de son auteur pour être clairement formulé.
Cet expert japonais cherchait à trouver une solution face aux problèmes posés par les goulots d’étranglement sur les équipements de production, là où la chaîne était considérablement ralentie.
En quoi cette SMED peut-elle permettre de réduire ces temps de changements de séries ?
La SMED théorisée par Shingeo Shingo vise notamment à réduire les opérations internes et, à l’inverse, à maximiser celles externes. Les opérations internes, ce sont celles qui ne peuvent être effectuées qu’en arrêtant la machine, car des composantes de la machine doivent être manipulées. Tandis que les opération externes sont réalisées hors machine et ne rendent donc pas nécessaire son arrêt. Or, il peut arriver que des opérations externes, parce qu’elles sont mal pensées ou organisées, impliquent l’immobilisation de la machine.
Pour faire en sorte que les opérations soient les plus externes possibles, et donc réduire les temps d’immobilisation des machines, il est essentiel de commencer par identifier les opérations véritablement nécessaires et éliminer celles qui ne le sont pas. Ces dernières peuvent provenir de modes opératoires anciens, qui n’ont pas pris en compte les erreurs ou les opportunités d’amélioration relevées sur le terrain, au gré de la production. La digitalisation du mode opératoire est d’ailleurs une évolution décisive dans ce sens, puisqu’elle facilite sa mise à jour et sa mise à la disposition des opérateurs sous sa forme réajustée.
Considérée comme un atout pour l’amélioration continue, la méthode SMED préconise l’élaboration et l’application de modes opératoires, car ceux-ci fixent des standards auxquels les collaborateurs sont appelés à se conformer lorsqu’ils réalisent les opérations associées aux changements de séries.
Picomto est la solution web et mobile pour créer et consulter des modes opératoires visuels. Les modes opératoires Picomto participe à l’amélioration des changements de série de production. Pour plus d’informations, contactez-nous !
Laisser un commentaire