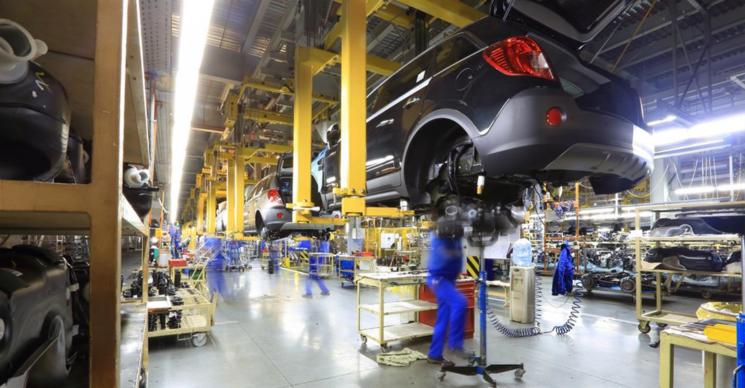
Développée dans les usines Toyota, la méthode 5S a ensuite vu son application s’étendre bien au-delà de l’industrie automobile, allant même jusqu’à être adoptée par des sociétés de services. C’est dire l’universalité et l’efficacité de ce procédé. Elle semble même parfaitement indiquée pour accompagner l’évolution de l’industrie du futur.
Qu’est-ce que la méthode des 5S ?
L’objectif de la méthode 5S est de faire en sorte que l’environnement de travail soit parfaitement organisé pour favoriser une amélioration continue, des conditions de travail et des performances optimales. Cela passe notamment par la mise en place de mesures de rangement, de sécurité et d’hygiène en appliquant des standards non seulement élevés, mais aussi et surtout compréhensibles et applicables par tous les collaborateurs concernés.
Une stratégie 5S bien appliquée permet à chaque opérateur de disposer d’un poste de travail totalement adapté à sa mission ; les outils dont il a besoin sont à portée de main, les documents nécessaires sont accessibles, etc. Ainsi, les déplacements, manœuvres et efforts inutiles, et qui constituent donc des entraves à la productivité, sont minimisés, voire éliminés pour une efficacité maximale.
Consultez également notre article sur : l’industrie 4.0, une véritable évolution du mode de production
Les entreprises organisent des audits 5S pour s’assurer que les procédures soient bien respectées dans tous les domaines. Cette démarche vise à identifier les problèmes et à y remédier rapidement. Elle se base notamment sur des checklists faisant apparaître les actions à réaliser et l’évaluation de leur exécution. Cela fait partie du suivi, le dernier des 5S que voici :
- Seiri (sélectionner) : trier les éléments d’un poste de travail (outils, objets…) pour éliminer ceux qui sont inutiles (à marquer avec une étiquette rouge), garder à portée de main ceux que l’on utilise toujours et ranger judicieusement ceux auxquels l’on a recours de manière occasionnelle.
- Seiton (situer) : prévoir un emplacement pour chaque élément et chaque élément doit être placé dans son emplacement spécifique, afin d’en faciliter l’accès et l’utilisation.
- Seiso (scintiller) : l’inspection, le nettoyage et l’entretien de l’espace de travail et des équipements.
- Seiketsu (standardiser) : mettre en place des méthodes de travail devant être appliquées et respectées à la lettre, ainsi que des outils de contrôle permettant d’évaluer l’efficacité des processus.
- Shitsuke (suivre) : la checklist évoquée plus haut est l’un des supports permettant d’assurer le suivi des bonnes pratiques et du respect des standards, et ce, de façon continue. Il s’agit d’enraciner la démarche dans la culture de l’entreprise pour soutenir l’amélioration continue.
Quelle est sa place dans l’industrie de demain ?
Productivité, sécurité et efficacité sont les priorités de l’industrie d’aujourd’hui et le seront également pour celle du futur. La méthode 5S et l’audit qui y est associé, y compris l’audit de sécurité, offrent des garanties dans ces domaines.
En préconisant la mise en œuvre de procédures standards, avec des consignes de sécurité claires, les risques d’accidents sont réduits. Les résultats d’audits permettent aussi d’apporter des corrections dans les processus et d’identifier plus facilement les problèmes, ce qui contribue à améliorer la qualité des produits. La vérification de la bonne application des 5S assure, en outre, un gaspillage minime, puisque, comme nous l’avons vu, toute manipulation ou consommation superflue est éliminée.
Et comme la numérisation gagne l’ensemble des organes de l’industrie, l’audit 5S n’y échappe pas et profite même des avantages que les nouvelles technologies apportent. La digitalisation des audits 5S, ce sont, entre autres, des checklists informatisées, donc plus simples à générer, à remplir, à communiquer et à analyser pour prendre les décisions adéquates, en fonction des informations recueillies durant les évaluations.
En revanche, la méthode ne peut être couronnée de succès qu’avec l’implication de toutes les parties, du haut de la hiérarchie (direction) aux opérateurs. La participation des employés est un préalable indispensable à la réussite du projet, qui doit d’ailleurs s’inscrire dans la continuité, et non pas obéir à une logique de court terme.
Picomto participe à la digitalisation des audits 5S grâce à sa solution de création d’instructions visuelles de travail et de formulaires de capture de données terrain. N’hésitez pas à nous contacter si vous voulez en savoir plus sur la solution.

Laisser un commentaire