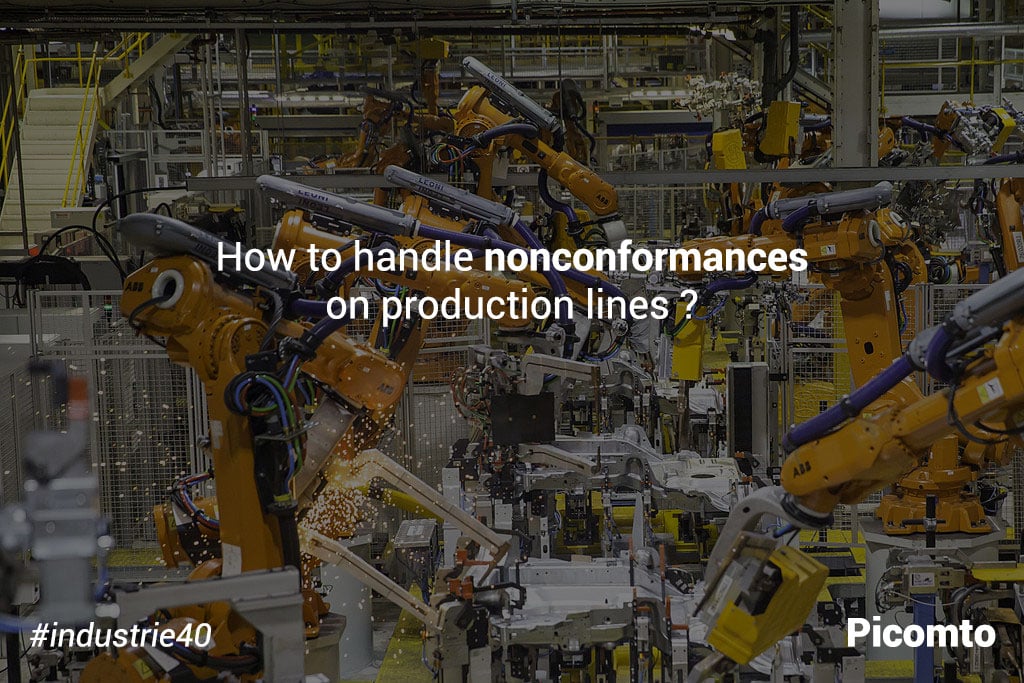
A lot of industrialists agreed to say that anything that could affect the quality has to be detected and corrected as soon as possible. In a context of open markets and, therefore, extreme competition, we can’t afford to lose points against others because of products with any anomalies.
The hunt for non-conformances is one of the priorities of business managers and their management is a major issue. This approach must obviously lead to corrective and preventive actions, as well as monitoring their effectiveness.
What causes non-conformances and what are the consequences?
Tending to the zero defects is the goal of any industrial, but incidents are almost inevitable, even in the best structured organizations. There are still potential sources of anomalies in the design or manufacture of a product, despite all the preventive measures that can be created.
Why ? Because the industry remains based on the human and that the error is unique to it. One can never avoid all the errors of understanding, the weaknesses related to the training, to the execution of a task, to the disagreement between collaborators. As well as some important changes in production can give rise to these non-conformities : launch of a new product, change in staff, change of process etc.
Their impact on businesses can be unfortunate, going from delayed deliveries to the deterioration of their brand image, incremental costs and risks for users.
When are they discovered?
There are two situations in which a non-conformance can be detected. The first is in the internal framework of the company. To make it simple, the organization detects the anomaly itself by means of checks carried out during the various stages, from the design to the preparation of the delivery which is obviously passing through the manufacturing. Here, finding a non-conformance is not a good news, but it shows that the controls are properly doing their job.
But what is even more annoying is when, the non-conformance is detected externally, once the product is in the hands of the customer, because it significantly affects his perception of the quality of this product that the company produces. This is the best way to lose business opportunities for the benefit of competition.
React as quickly and efficiently as possible to maintain and improve quality
It is extremely important to create processes in order to prevent, detect and correct non-conformances as early as effective. This implies a real collaboration between the actors that are concerned and the production chain progress needs to be carefully checked.
The ISO 9001: 2015 standard provides that “depending on the nature of the non-conformance […], the organization must take appropriate corrective action” and also that “where non-conformance occurs, including those related to complaints, the organization must […] react to control and correct […] the consequences […] of assessing whether it is necessary to take action to eliminate the cause or causes“.
The main production incident management supports are the non-conformance sheets, on which the identified anomalies are described in detail : nature of the non-conformance, Concerned persons, stage of the process in which it occurred, the time, the place, the causes and their analysis, as well as the solutions proposed in order to prevent it from happening again. These documents also include information regarding the establishment and monitoring of the corrective action, as well as the verification of its effectiveness.
By carefully recording these elements, you maximize your chances to prevent other non-conformances, in particular by having always up-to-date working instructions (modified by taking into account of detected and corrected anomalies).
Decrease the risks by using Digital Work Instructions
By using digital and visual work instructions in production, you can help your workforce produce right the first time. Picomto is the leading software in Europe to create, exploit and analyze Digital Work Instructions. Feel free to contact us for a demonstration.
Leave A Comment