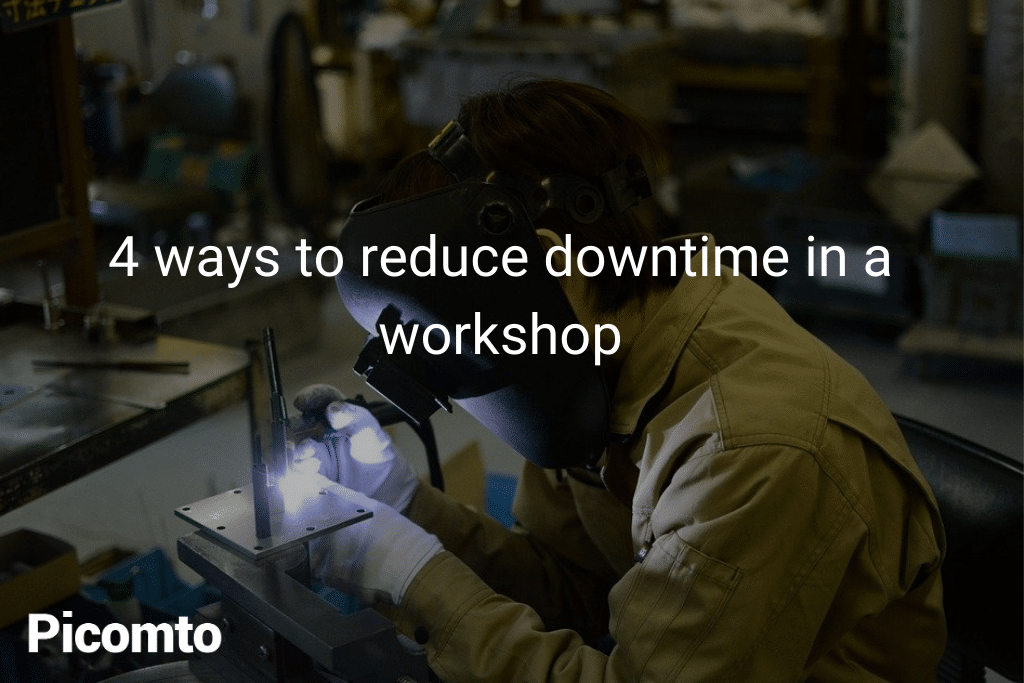
Downtime is one of the major causes that hinder productivity. In fact, this wasted time engenders the loss of irremediable capacities.
Generally, its data is noted on a paper. This makes the implementation of an improvement process difficult. Limiting planned and unplanned downtime often poses a real challenge. Hence, thanks to digitalization, Picomto helps companies to reduce downtime by implementing for example digital work instructions and checklists.
The disposal of downtime permits to ensure both the quality of the final product and customer satisfaction.
Downtime in industry: Definition
Also called outage time or even unproductive time, downtime generally refers to production shutdowns hindering productivity in a factory. It is important to make the difference between breakdown and downtime. In fact, the notion “down” gathers maintenance and production management. The latter encompasses designing and planning material, financial or human resources.
Some of the main effects of production shutdown are the following:
- Stress of operators
- Slowdown of the operational performance
- Increase of waste, NVA (no value added) and non-compliance
It is important to study downtime in an industry. Indeed, this permits to reduce the losses due to production shutdowns. Generally, production shutdowns have a major impact on the overall equipment effectiveness (OEE). Sometimes, simple improvements lead to a marked improvement of performance. Besides, by analyzing downtime, it will be easier to implement corrective measures.
Why is there a downtime?
There are several types of downtime:
- Induced downtime
It is the time during which the means of production is inactive due to an external cause. Several causes may be the origin of these downtimes namely:
- Lack of supply
- Lack of energy
- Saturation of parts
- Lack of staff (waiting, absence, meeting, break, etc.)
This type of downtime affects mainly the performance of the production line as well as productivity of the workshop. This sudden event will mobilize a part of your maintenance staff that has to look for the cause of this downtime and make the equipment functional as soon as possible. However, in the meanwhile, productivity will decrease which can affect the profitability of the factory.
- Proper downtime
It is the downtime attributed to the means of production. In order to analyze this type of downtime, we discern:
- Breakdown time (mechanical or electrical stop, malfunctioning etc.)
- Exploitation downtime (human error, quality problem, etc.)
- Functional downtime: it is the planned downtime (control, adjustment, maintenance or even tool change)
However, it is crucial to mention that even planned downtime still constitutes a loss for the factory. Indeed, no industrial site is spared from undergoing an unexpected situation during the action of correction of the downtime cause, disrupting the starting up of the production. Sometimes, just a simple unplanned extra day is enough to cause losses that affect the competitiveness of the company.
4 ways to highlight and better deal with the causes in a digital manner
Documenting the reasons of downtime
In order to limit the causes of downtime, we opt more for the digitalization solution to simplify the communication process. In fact, thanks to digitization, it will be easier and faster to report incidents of production, thus minimizing alteration of workflows. For example, when a machine breaks down, the operator gathers and transmits information right from his post (terminal digital). This permits to optimize the response time of each collaborator and ensure optimal responsiveness. Also, this allows having a certain visibility of production shutdowns on the factory scale in real time.
Preventive maintenance
In order to reduce the downtime, it is important to implement a preventive maintenance plan. In fact, the latter permits to anticipate the potential breakdowns and to extend the life service of the equipment. It should be noted that the implementation of a program of planned maintenance is essential when the quality of production is altered owing to a flawed machine.
It is recommended that a preventive maintenance policy together with digital forms should be implemented in order to detect and solve the problems before the occurrence of a breakdown.
Advantages of preventive maintenance
- Security
- Production improvement
- Breakdown reduction
- Downtime reductions
Training of operators
The rule says “a well-trained operator will definitely improve his productivity”. In order to develop an ongoing training of operators, it is important to use a digital work instruction. This method permits to facilitate exchanges, information transmission and the certainty of working with latest updated versions. Another important point is to train operators to do it right the first time. It is a LEAN approach that permits to eliminate the production of non-compliances and waste of time. Hence, having concrete training materials is easier to assimilate and apply.
Improving work instructions
In order to limit downtime in a workshop, it is equally important to implement interactive and adapted instructions for operators. This allows avoiding not only interpretation but also human error. We should note that the continual improvement that is carried out on a production site ensures time saving and efficiency.
Concerning Picomto
Picmoto is presented as an innovative solution to help operators to have a clear and precise instruction without ambiguity. This application equally permits to create checklists for preventive maintenance. It should be noted that it is the best means to create operating procedures to train operators. For further information, please don’t hesitate to contact us.
Leave A Comment