Les temps d’arrêt sont l’une des causes majeures qui pénalisent la productivité. En effet, ce temps perdu engendre des pertes de capacités irrattrapables.
Généralement, ses données sont notées sur un support papier, ce qui rend difficile la mise en place d’une démarche d’amélioration. Limiter les temps d’arrêt planifiés et non planifiés pose, souvent, un véritable défi. De ce fait, Picomto, grâce à la digitalisation, aide les entreprises à diminuer les temps d’arrêt en mettant en place, par exemple, des instructions de travail digitales et checklists.
L’élimination des temps d’arrêt permet d’assurer à la fois la qualité des produits finis et la satisfaction client.
Optimisez vos opérations et réduisez les temps d’arrêt imprévus. Regardez notre étude de cas avec SKF pour comprendre comment une maintenance préventive efficace peut transformer votre entreprise.
Définition : Temps d’arrêt (downtime) dans l’industrie
Appelés aussi temps d’indisponibilité ou encore temps improductifs, les temps d’arrêt renvoient, généralement, aux arrêts de production pénalisant la productivité d’une usine. Il est important de différencier la panne et le temps d’arrêt. En effet, la notion d’« arrêt » rassemble la maintenance et la gestion de production. Cette dernière englobe la conception et la planification des ressources matérielles, financières, ou humaines.
Parmi les principaux effets d’un arrêt de production, nous pouvons citer :
- Le stress des opérateurs
- Le ralentissement de la performance opérationnelle
- Une hausse des gaspillages, des NVA (Non Valeurs Ajoutées) et des non-conformités
Dans une industrie, il est important d’étudier les temps d’arrêt. En effet, cela permet de réduire les pertes dues aux arrêts de production. Généralement, les arrêts de production ont un impact important sur le taux de rendement synthétique (TRS). Parfois, de simples améliorations donnent lieu à une amélioration nette de la performance. Aussi, en analysant les temps d’arrêt, il sera plus facile de mettre en place des mesures correctives.
Pourquoi il y a–t-il des temps d’arrêt ?
Nous retrouvons plusieurs types d’arrêt :
- Temps d’arrêt induits:
Il s’agit des moments pendant lesquels le moyen de production est inactif à cause d’une cause externe. Plusieurs causes peuvent être à l’origine de ces arrêts, notamment :
- Un défaut d’approvisionnement
- Un défaut d’énergie
- Une saturation de pièces
- Un manque de personnel (attente, absence, réunion, pause, etc.)
Ce type de temps d’arrêt affecte davantage les performances de la ligne de production et ainsi la productivité de l’atelier. Cet événement brusque va mobiliser une partie de votre maintenance qui devra chercher la cause de cet arrêt et remettre les équipements en état de fonctionnement le plus tôt possible. Toutefois, entre temps, la productivité va chuter, ce qui peut affecter la rentabilité de l’usine.
- Temps d’arrêt propres :
Il s’agit des arrêts imputables au moyen de production. Pour faire l’analyse de ce type d’arrêt, nous discernons :
- Le temps de panne (arrêt mécanique ou électrique, un dysfonctionnement, etc.)
- Les temps d’arrêt d’exploitation (erreur humaine, problème de qualité, etc.)
- Les temps d’arrêt fonctionnels : il s’agit des arrêts planifiés (contrôle, réglage, entretien ou encore changement d’un outil).
Toutefois, il est important de souligner que les arrêts de production, même planifiés, demeurent une perte pour l’usine. En effet, aucun site industriel n’est épargné de subir une situation inattendue lors de l’action de correction de la cause de l’arrêt, perturbant la remise en route de la production. Parfois même, il suffit d’un simple jour supplémentaire, non prévu, pour entrainer des pertes affectant la compétitivité de l’entreprise.
Ebook
Ne laissez pas les pannes imprévues ralentir votre production !
Téléchargez notre e-book sur les modes opératoires pour découvrir comment intégrer la maintenance préventive efficacement.
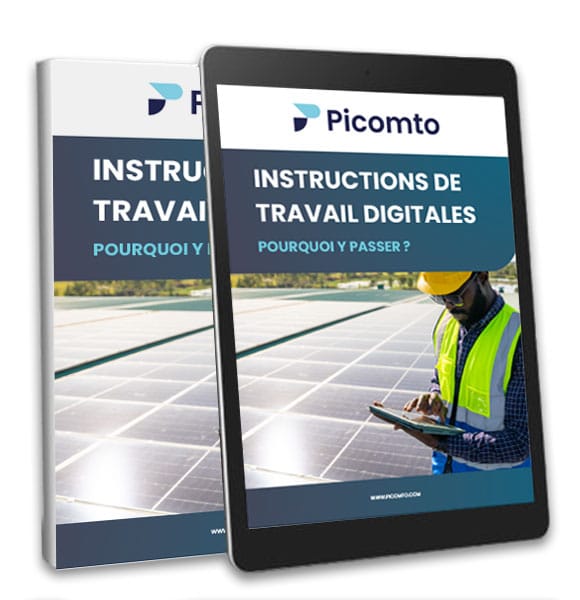
voyages évités chaque semaine
gagnés chaque année
4 façons pour tracer de façon digitale les causes et mieux les traiter
Documenter les raisons des temps d’arrêt
Afin de limiter les causes d’arrêt, on opte de plus en plus pour la solution de digitalisation afin de simplifier les processus de communication. En effet, grâce à la numérisation, il sera plus facile et plus rapide de déclarer les incidents de production, minimisant ainsi l’altération des flux de travail. Par exemple, lorsqu’il y a une panne au niveau d’une machine, l’opérateur rassemble et transmet l’information directement depuis son poste ( terminal digital). Cela permet d’optimiser les délais d’intervention de chaque collaborateur et d’assurer une réactivité optimale. Aussi, cela permet d’avoir une certaine visibilité des arrêts de production à l’échelle de l’usine en temps réel.
Maintenance Préventive
Pour réduire les temps d’arrêt, il est important d’établir un plan de maintenance préventive. En effet, cette dernière permet d’anticiper les pannes potentielles et de prolonger la durée de vie des équipements. Notons que la mise en place d’un programme de maintenance planifiée est essentielle lorsque la qualité de production est altérée à cause d’une machine défectueuse.
De ce fait, afin de détecter et de corriger les problèmes avant l’apparition d’une panne, il est recommandé de mettre en place une politique de maintenance préventive, et ce, avec des formulaires digitaux.
Les avantages de la maintenance préventive
- La sécurité
- L’amélioration de la production
- La réduction de pannes
- La réduction de temps d’arrêt
Optimisez chaque type de maintenance préventive grâce à des outils adaptés et performants. Découvrez comment les checklists et modes opératoires de Picomto facilitent la gestion de la maintenance.
Former les opérateurs
La règle dit : « un opérateur bien formé va impérativement améliorer sa productivité ». Pour établir une formation continue des opérateurs, il est important d’utiliser une instruction de travail digitale. Cette méthode permet de faciliter les échanges, la transmission des informations et la certitude de travailler avec les dernières versions mises à jour.
Un autre point important, c’est former ses opérateurs à faire bien du premier coup. Il s’agit d’une démarche LEAN permettant d’éliminer la production des non-conformités et la perte du temps qui en découle. De ce fait, avoir des supports de formations concrets est plus facile à assimiler et à appliquer.
Améliorez ses instructions de travail
Pour limiter les temps d’arrêt dans un atelier, il est également important de mettre en place des instructions interactives et adaptées pour les opérateurs. Cela permet d’éviter non seulement l’interprétation, mais également l’erreur humaine. Notons que l’amélioration continue effectuée sur un site de production se présente comme un véritable facteur de gain de temps et d’efficacité.
À propos de Picomto
Picomto se présente comme étant une solution innovante pour aider les opérateurs à avoir une instruction claire et précise sans ambiguïté. Cette application permet également de créer des checklists pour la maintenance préventive. Notons qu’il s’agit du meilleur moyen pour créer des modes opératoires afin de former les opérateurs. N’hésitez pas à nous contacter si vous voulez en savoir plus.
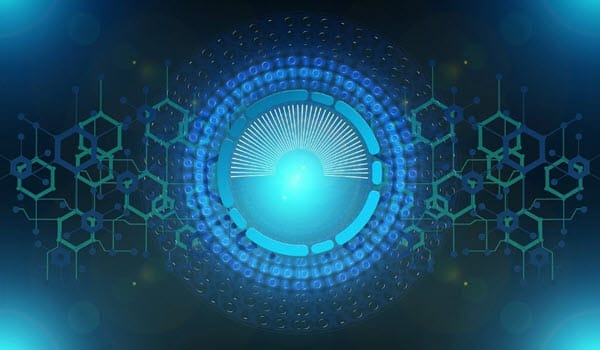
Laisser un commentaire