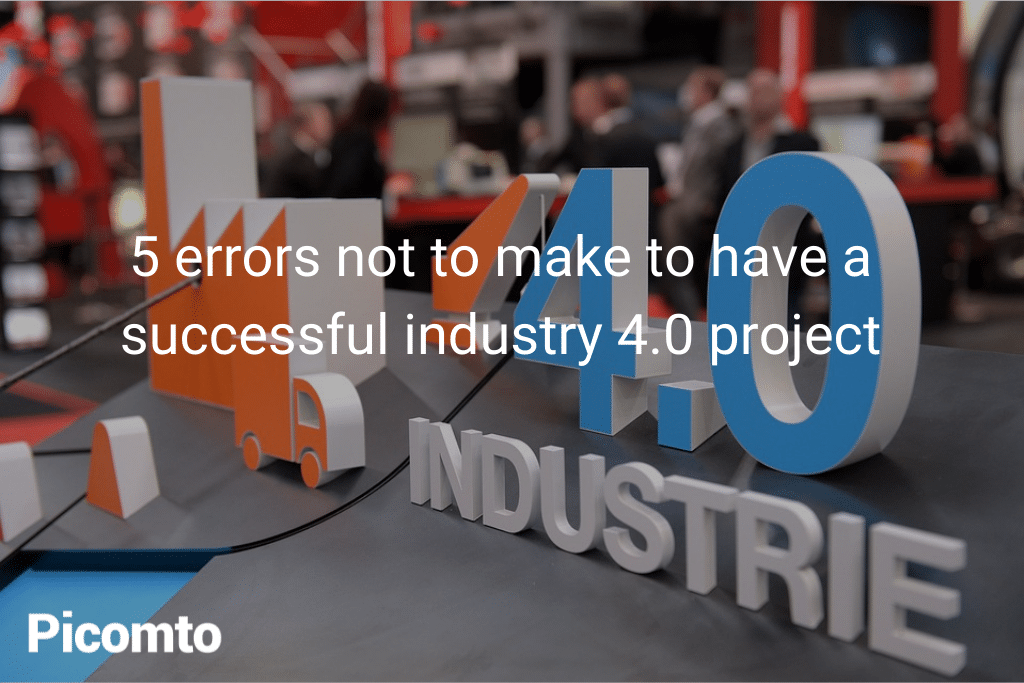
Talking about industry 4.0 refers to a new generation of factories that are connected, robotic and intelligent. Number 4 is to mark and highlight this 4th industrial generation. We can even say that with the digital revolution, boundaries between the physical world and the digital one are reduced to give life to factory 4.0.
The concept “industry 4.0” first emerged in 2011 at Hanover Global Industry Forum. This “industry of the future” project refers to a new way of imagining production means. It is based on technologies such as internet of things, augmented reality or even virtual reality. This new innovative approach helps to move towards a better management of industrial resources. It also helps to achieve a qualitative leap in terms of services.
To ensure a successful transition to industry 4.0, we propose a list of errors that you should not make.
Do not involve the operator in discussions
One of the main evolutions of industry 4.0 is the digitalization of information. However, these new technologies will not eliminate the tasks carried out by humans. However, it is important to place the operator at the core of the automation and computerization procedure.
Considering that he is often the final user of a software or solution, it is important to involve him in the discussion. Human intelligence is essential to operate and monitor production tools however sophisticated they may be. Hence, by taking into consideration the operators’ specificities and requirements, this helps to upgrade them by placing them among the fundamental elements of the company’s strategy.
In this respect, industry 4.0 is synonymous with valuing employees by evolving their tasks and roles to missions with high added value.
Do not make software, machines and robots communicate with each other
Without human intervention in the industry field, interaction between connected equipment develops at top speed.
In an intelligent factory, all devices and software must cooperate. In fact, all systems should be connected to each other. Incapacity to communicate can hinder the production process. Indeed, one of the crucial issues facing industry 4.0 is to ensure reliability, productivity and time saving.
Hence, this “factory of the future” must ensure that its production site communicates machines with software and robots. The idea is to make the work process faster and more flexible.
Note that the advent of the so-called Internet of Things gave birth to a set of disciplines such Machine to Machine, better known as M2M. The latter is a subset of IOT. It groups different information exchange technologies allowing machines to communicate with each other without human intervention.
In other words, we can say that M2M refers to anything that allows software, machines and robots to communicate with each other automatically.
Not having precise objectives or problems to solve
First of all, introducing new technologies of industry 4.0 must be carried out with a great deal of lucidity. You should not opt for the concept of “industry of the future” without a precise objective. Before investing large sums of money in digitization, the company must diagnose the return on investment to measure the real needs of a company. Every industry must ensure that going digital will bring real business benefits. The primary goal of these new technological evolutions is to optimize productivity and turnover of any industry.
To know whether a company should opt for industry 4.0, the first step to take is to carry out an evaluation. Adopting this concept must not absolutely be rushed. It is essential to analyze all aspects properly before embarking on such an approach without anticipating its profitability.
Note that the success of any conversion to industry 4.0 is essentially based on this step, failing which; it could quickly become a real waste of time.
Not mobilizing teams internally
This new generation factory is also based on the mobilization of internal teams. In fact, this helps to start the transition to industry 4.0.
Hence, it is important to train employees to develop their skills. One person is unable to set up everything. In fact, this affects all services and departments and everybody should be involved in project management in order to succeed. Also, teams must learn to use the new tools, follow a continuous training regarding quality and maintenance.
Not accompanying change
Moving to industry 4.0 is also subtly initiating the digital transformation of your industry. You will not start from scratch or simply sweep aside everything you have set up. You are simply going to optimize what already exists.
This transformation is able to affect all aspects of the industrial company. Hence, every industry must adopt tailored measures of change and this of course step by step. In fact, it is not easy to make a radical and abrupt change in your work method. It is therefore necessary to undertake a process of transformation of employees’ habits in the long run.
So, we can say that implementing change management is able to ensure the proper development towards industry 4.0.
Expert in setting up the project of industry 4.0, Picomto is your ideal solution to establish a digital transformation thanks to the feedback of our customers who have implemented it. Indeed, it is software for digitalizing operational documentation of industry 4.0.
Leave A Comment