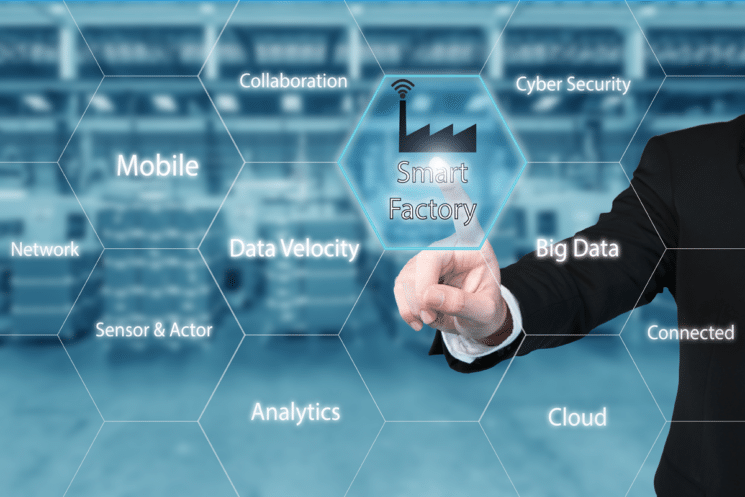
Under the impetus of government institutions and business representative bodies, actions have been taken to facilitate the transition to organizations that are more in line with technological innovations. The aim is to take advantage of the potential offered by the latter to gain in competitiveness, but also to meet environmental and societal challenges. Industry 4.0 is well and truly on the move, but at what stage of this evolution are we at today?
The promises of the industry 4.0
The industry of the future, or industry 4.0 to use the name that appeared in Germany in 2011, is presented by the French Federation of Mechanical Industries (FIM) as “a response to several simultaneous transitions: energy, ecological, digital, organizational and societal. Each of these transitions involves many new technologies or organizational modes that are maturing, being developed or designed. It aims to support the modernization of the production tool and to transform business models and organizational modes on the one hand, and design and marketing modes on the other.
The shift to this 4.0 industry offers interesting opportunities for companies:
- Produce faster
- Improve quality, especially through process optimization
- Increase the personalization of production
- Ensure better cost control
- Optimize the use of resources
- Making work easier
- Expand the product range
In the service of this modernization, many innovative technologies are being introduced in the heart of the plants and in the various departments of the companies. The machines and the products themselves are equipped with sensors that collect considerable amounts of data (Big Data), the analysis of which helps to optimize production lines. Robotization is taking an increasingly important place in the workshops, promising greater autonomy and flexibility. On this point, it is mainly the cobots, or collaborative robots, that are integrated in order to act in collaboration and harmony with human operators. The Internet of Things applied to industry (IIOT), additive manufacturing (3D printing) and cloud-based media also contribute to the edifice of digital transformation. The same applies to augmented reality tools and those used to perform 3D simulations to improve models.
Government actions and state of play in 2017
To support companies in their modernization process, governments have launched various programs.
The one called “Industrie du futur” in France was created in 2013 and reissued in 2015. The “Industrie du futur” Alliance has been entrusted with the task of coordinating these efforts, in particular through support for 47 key new technologies.
In Germany, the cradle of the Industry 4.0 concept, connected and intelligent factories have benefited from the dynamism of major players such as Siemens.
The Chinese government, for its part, has launched the ambitious “Made in China 2025” plan to develop a more innovative and creative industry, while boosting productivity.
In Belgium, more specifically in Wallonia, the Made Different Digital Wallonia program, with the objectives of “raising awareness and supporting Walloon manufacturing companies in their transformation towards a company of the future”, has already delivered a first quantified assessment for 2017: more than 120 companies approached for an in-depth analysis of their situation and around sixty “have carried out or are carrying out a digital maturity diagnosis or an in-depth scan to identify the gap between their situation and their objectives. »
Picomto is the European leading web and mobile solution for creating, managing, sharing and exploiting visual work instructions. The solution is part of the industry 4.0 concept.
Leave A Comment