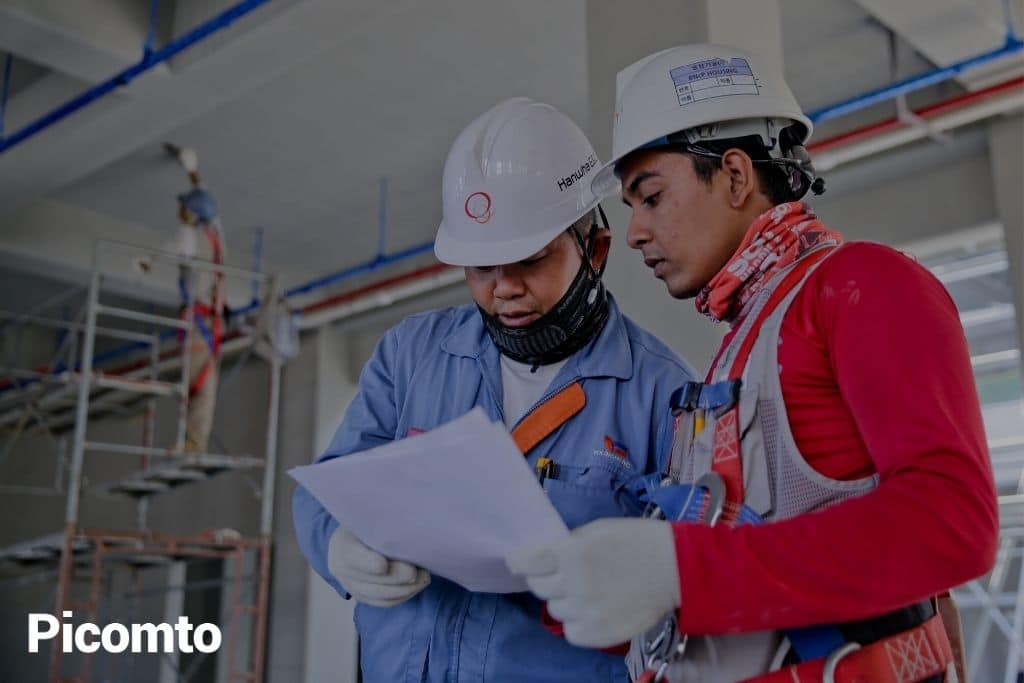
All professional activities involve some risk. The industrial world is no exception; operators operate in the midst of equipment that is sometimes heavy, bulky, powerful, and sometimes in the presence of potentially dangerous substances. Manufacturers must, therefore, provide their teams with optimal safety conditions because it is as much a question of the health of employees as it is of the company’s performance and its image. To this end, it is essential to work on three aspects: risk identification and analysis, implementation of good practices and staff awareness of these risks.
Assess and analyze risks
According to International Labour Organization statistics, 2.3 million people lose their lives as a result of accidents at work or occupational diseases every year around the world. Safety is one of the major challenges facing the industry and for which it is vital to provide effective and sustainable solutions.
Before setting up a safety action programme, it is necessary to carry out a risk assessment and analysis work so that the measures subsequently developed can really respond to the various alert situations that may arise.
Risk identification is a long-term and multidisciplinary task, involving a variety of stakeholders, from occupational safety specialists to managers of the departments and services concerned by these measures. It requires a perfect knowledge of the processes, the specificities of the positions and their requirements.
Implementing good practices
Once the risks have been identified and accurately assessed, managers can move on to the implementation of good security practices.
The aim is to define the actions to be taken, to allocate roles and responsibilities and to deploy all the technical and material resources necessary for the safety of operators.
This includes the installation of safety signs, pictograms and other safety signage in accordance with standards, behaviour in the event of an accident, coordination between the various departments and safety equipment. PPE (personal protective equipment: helmets, earplugs, high-visibility vests, gloves, masks, protective glasses…), precisely, are the subject of particular attention and benefit from technological progress, especially those of the digital and connected world. One example is the “Connected Operator” project, jointly led by Bouygues Construction, Suez, Air Liquide and the CEA’s Technical Research Department. It includes, among other things, the development of a connected sleeve guiding and informing the worker in real-time, an intelligent vest capable of analysing the quality of the air breathed by the employee, protective goggles equipped with a mini-camera and displaying warning pictograms, and shoes with geolocation.
Raise awareness and involve staff
The wearing of PPE and the newly connected tools developed in this field promise to improve operator safety. However, all these technologies are not worth much if they are not accompanied by adequate training to ensure their proper use, as well as the involvement of staff.
It is crucial to make the operator aware of the risks associated with their jobs, as well as the means of preventing and reacting to them. Communicating compliance with work and safety instructions among employees is an obligation for any company, which thus avoids the negative repercussions that incidents can have on its performance, on the morale of its employees and on its image.
In any case, the requirements for the protection of personnel are constantly being increased to allow for continuous risk reduction. ISO is currently developing a new standard, ISO 45001, to improve occupational health and safety management systems. It is expected to be published on February 2018.
About Picomto
Picomto is the web and mobile software solution for creating, managing, sharing, consulting and analyzing visual work instructions.
Leave A Comment