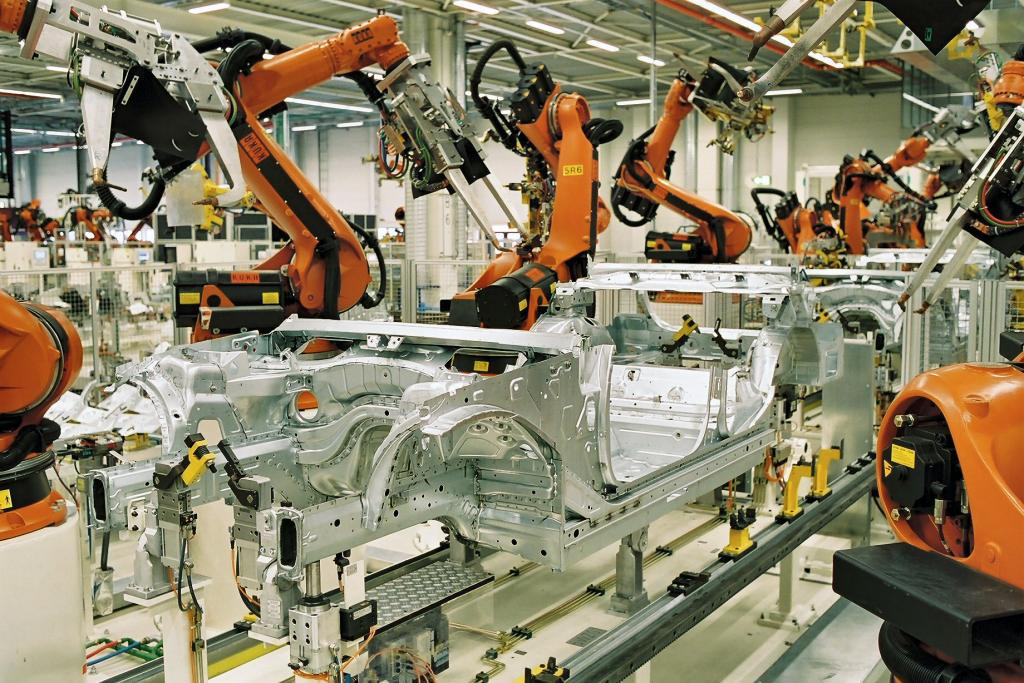
In many countries, the industry has already entered a new era, that of the industrial revolution, mainly linked to the digital technology boom. One of the main features of industry 4.0 is the proliferation of smart factories, in which machines are interconnected and the Internet of Things and robotic devices play an ever-increasing role. By bringing all these evolutions, the industry of the future promises multiple prospects for improvement.
Interconnection of means of production and systems
One of the most important aspects of industry 4.0 is the evolution of communication systems and exchange networks within and around plants. The remarkable progress made in digital technologies provides innovative tools that benefit all the company’s key elements: production, but also logistics, management and relations with partners and customers.
Today, equipment and workstations are increasingly interconnected. The machines communicate with each other and with the employees, sending signals to the latter when there is a failure, when a critical threshold is approached and an intervention (maintenance, repair, troubleshooting, replacement…) is to be programmed or simply to report on its condition and performance.
The possibility of consulting data remotely and acting without necessarily being at the production site is also one of the benefits offered by technological innovations related to the industry of the future.
More flexible production and personalization
The intelligent tools that make up the smart factory are also formidable levers of flexibility. Thanks to the Internet of Things and the Internet itself, the company communicates more with its customers at the same time as it adapts its production more easily, which allows it to personalize its offer without having to produce on a small scale.
Identifying the real expectations of consumers is indeed one of the major challenges for any industrial company, and it is undeniable that new technologies constitute a major asset in this field because of the increased proximity and interactivity they allow.
Traceability and quality
The new organizations implemented and the tools deployed offer advantages in terms of process monitoring and traceability. If necessary, it becomes less complicated and more practical to focus on a given operation to identify, for example, the origin of a failure or any other element that could affect productivity and quality. The implementation of quality and safety controls throughout the production chain is considerably facilitated to provide reliable and usable data.
At the same time, industry 4.0 wants to be a better manager of its costs, as well as its energy and raw material resources, in particular through improved coordination between needs and available resources.
What place for the human factor?
Some fear that the rampant automation induced by the digitalization of the industrial environment will relegate man to the background. However, far from being sidelined, the employee’s role and place are evolving towards a broadening of skills, at the same time as new professions are being created to meet the new requirements and specificities of industry 4.0. Encouraged to constantly improve its qualifications through, among other things, continuous training, the human remains at the heart of the company’s operations.
About Picomto
Picomto is the software solution to digitize the operationnal documentation in the industry : work instructions, checklists, maintenance procedures.. Request a demo by contacting us
Leave A Comment