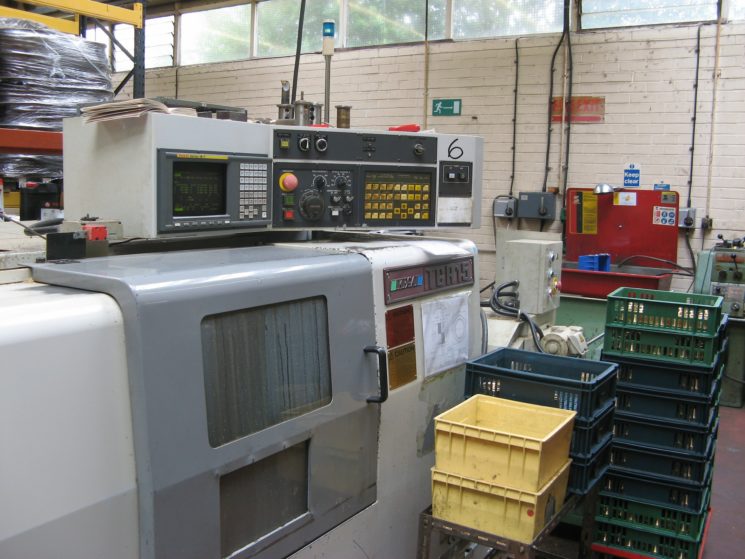
Make processes more efficient by identifying and eliminating waste, knowing customer expectations and organizing to meet them. These are the main objectives that define Lean Thinking, a “way of thinking” based on the Lean approach and promoted by the authors of a book that has become a reference in the field of industrial management. How does Lean Thinking apply to the industry and what are the keys to it?
Let us review its 5 main principles, set out in the book, co-authored by James P. Womack and Daniel T. Jones (Lean Thinking: Banish Waste and Create Wealth in Your Corporation – Lean System: Thinking the Business Right).
Precisely identify the client’s need
The first step of Lean Thinking is to put yourself in the customer’s shoes to identify his need, to know what he really expects as a product or service. His expectations are precise, and he is only willing to pay the price of the good or service he needs. He is not especially willing to pay more for the costs associated with waste and other production problems, nor for an additional service that he did not request. The customer will have no problem in contacting another supplier if he or she feels that the product offered does not meet his or her expectations. In other words, it is about defining the value or utility of the product in the customer’s sense.
Respond by optimizing the process
To meet customer expectations, an efficient and smooth process is required. This involves defining all stages of production and identifying both value-added and non-value-added operations. In the logic of Lean Thinking, the latter constitute waste and a loss of income. These non-value-added tasks should, therefore, be eliminated. Downtimes, logistical failures (transport, employee travel, etc.), defects or even overproduction are all obstacles to the efficiency of the process. The identification of the value chain makes it possible to highlight them in order to find appropriate solutions, such as, for example, the digitization of documents to reduce paper-based media and thus move towards a paperless working environment, less restrictive in terms of physical storage and updating of documentation.
Improving flows
Lean Thinking is also based on flow optimization. The aim is to improve the flow of these operations by remedying anything that could interrupt or hinder the sequence of value-added operations.
In industry, this concerns both production flows and logistics and administrative flows.
Index and orient its production according to the customer’s request
Rather than trying to “push” the flow and demand – which is less and less possible in an increasingly competitive context – Lean Thinking is based on the observation that it is now the customer who drives the flow, and therefore production. In other words, one should only produce when the customer has requested it and strictly according to the nature of his expectations. This characteristic implies optimal management and use of resources.
Tend towards zero defect
Finally, the fifth and final principle of Lean Thinking is to exploit all the opportunities for improvement that arise as the processes are applied. Continuous improvement requires the elimination of waste through various methods, including Kaizen and 5S. Lean thinking encourages industrialists to make their organizations strive for perfection.
About Picomto
Picomto is the European leading software of Digital Work Instructions. Feel free to contact us to know more.
Leave A Comment