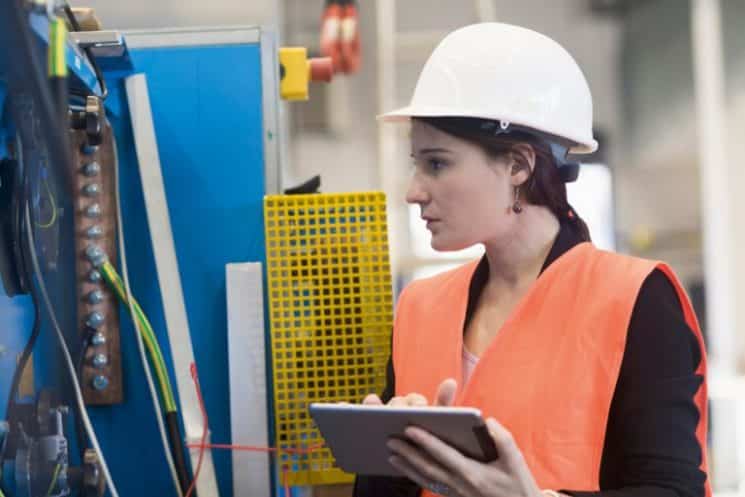
The evolution towards industry 4.0 is taking place at all levels, including maintenance. A crucial activity determines the availability and performance of means of production, maintenance is driven by technological innovations in digital technology. The technician responsible for carrying out these missions are the first to benefit from the arrival of new tools and state-of-the-art software dedicated to maintenance, which is more connected than ever.
Better organized predictive maintenance
While corrective maintenance remains a priority, predictive maintenance is now a priority, as it reduces machine downtime. While this development allows companies to improve efficiency and productivity, it also benefits maintenance technicians, who are thus less exposed to the pressure induced by the possibility of an incident occurring on a means of production. In other words, maintenance operators are not required to work in an emergency because a problem has just occurred on an equipment. Thanks to the sensors fitted to the machines, failure warning signs are collected and analyzed by CMMS (Computer Assisted Maintenance Management) software. The latter, combined with supervision software, warn the technicians in advance, so that they have plenty of time to prepare their interventions. This also allows them to better organize their tasks and schedules, especially on smartphones and tablets, which again helps to reduce pressure and stress at work.
Reduction of intervention times and improved efficiency
Maintenance 4.0 also promises significant time and efficiency gains.
Let’s take the concrete example of Microsoft’s HoloLens augmented reality headset, adopted in 2016 by German elevator manufacturer ThyssenKrupp. This device that the maintenance technician wears, while facing the machine and with his hands free, keeps him in continuous contact with a remote expert, who can see what the operator has in front of him. The latter also has information superimposed on the glasses to be better guided towards the actions to be carried out, always under the supervision of the expert who may be thousands of kilometers away. According to Javier Sesma Sánchez, Managing Director of ThyssenKrupp Elevator, “a typical case that used to take 2 hours until now only takes 20 minutes. Sometimes it was even necessary to send specialists to the site by plane” (source: Usine Digitale). This shows the levels of speed and efficiency that such hardware and software solutions offer.
Easy maintenance work and extended functionalities
On the other hand, the new maintenance tools provide concrete help to the technician and extend the functionalities at his disposal. Picomto specializes in the digitization of technical documents: the maintenance operator relies on a mobile application that, installed on a smartphone and tablet, provides all the necessary documents including checklists and operating modes. The latter integrate a particularity which is their interactivity; according to the answers that the technician enters, they will direct him towards the action to be taken. Even better, the solution developed by Picomto automatically produces a maintenance report, thus helping the operator to avoid a lot of work.
Leave A Comment