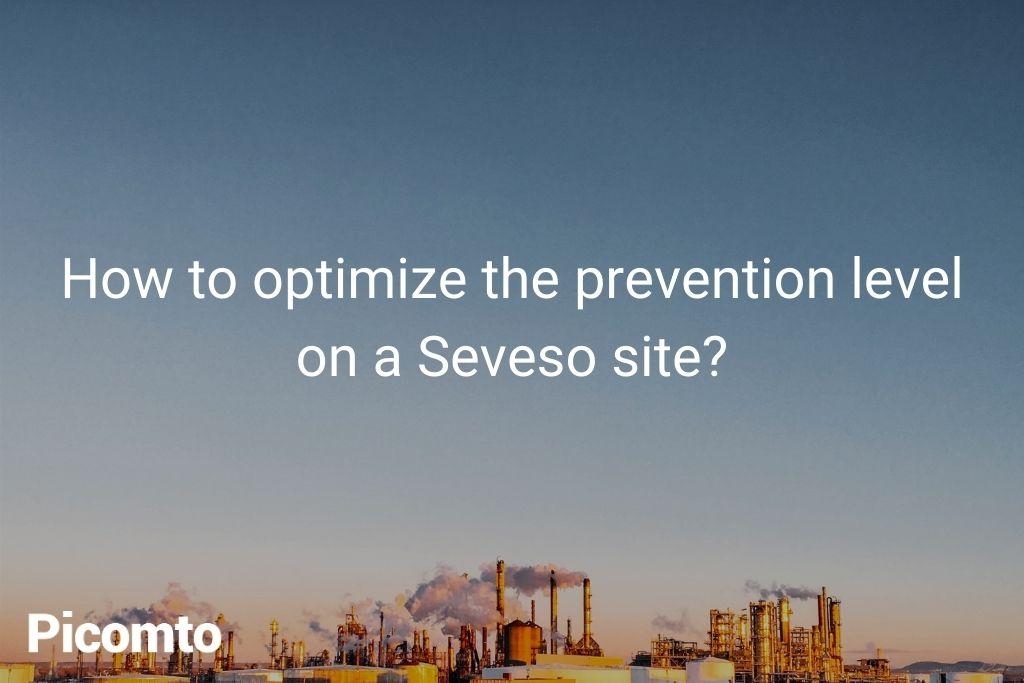
Seveso sites are industrial sites that present a high risk of major incidents endangering the health of workers and the surrounding environment (animals, humans, plants, etc.). These sites are subject to a risk management strategy and preventive management systems to prevent accidents from occurring. Employee training plays a major role in incident prevention.
Seveso Directive
This is the name given to a series of European directives requiring EU member states to identify industrial sites at risk of major accidents involving hazardous materials in order to maintain a high level of prevention. The latest Seveso directive is the one that came into force on June 1, 2015 and concerns 10,000 industrial sites and 1,200 French establishments.
Why optimize the level of prevention?
Zero risk does not exist on a Seveso site. In such an establishment it is necessary to always maintain a high level of prevention and to apply the rules of problem anticipation.
The level of risk depends on the quantity and nature of the hazardous material handled within the establishment. It may be chemical materials intended for the production of pharmaceutical or agricultural products (fertilizers, etc.) or petrochemical materials derived from petroleum such as gasoline, tar, etc.
Risks can be classified into 3 categories according to the effects caused by a possible accident:
- Thermal risks :
The risk of explosion is present when handling flammable or explosive products. The thermal effect caused by such an accident can lead to more or less serious burns.
- Mechanical risks :
Mechanical effects are caused by explosions or detonations. The shock wave can cause severe material damage, but also damage to the lungs and eardrums.
- Risk of intoxication :
Leaks of toxic chemicals are a major risk in chemical industrial sites. Damage caused by contact with such substances by inhalation, ingestion or touch may include chemical burns to the skin, damage to the nervous system or acute oedema of the lung.
Continuous training of employees on new measures and risks
The human factor is one of the main causes of industrial incidents. To reduce this risk factor, establishments must provide ongoing training for employees to keep them up to date with new preventive measures, handling and the risks involved.
The reality is that when people work in a hazardous occupation over a long period of time, they often tend to lower their level of vigilance through the monotony of repetitive tasks. It is therefore necessary to always remind people of the risks and to refresh their knowledge and know-how with regard to preventive gestures and protective measures.
Having immediate access to operating procedures in digital format allows operators to be more efficient in their safety control and inspection tasks. This information is easily updated by managers to implement new protection, control and inspection measures. Optimizing the flow of information helps to improve the level of safety in high-risk establishments.
Another point to consider is that the format of training materials is as important as their content. Having digital materials illustrated with explanatory images helps to improve the level of understanding of the training content or operating procedures. Thus, the digitization of documentation and training materials within the Seveso establishment is essential to maintain a high level of security.
What strategies to anticipate problems?
Set up preventive maintenance
Preventive maintenance helps to increase the level of safety and efficiency of industrial equipment. Implementing and planning a preventive maintenance strategy reduces the risk of leaks or explosions at Seveso sites.
Automation of maintenance improves efficiency by always reducing the human factor (forgetfulness, negligence, etc.). The use of planning and notification software solutions helps preventive maintenance teams to carry out their tasks. It is also imperative to opt for clear and comprehensible documentation to avoid any errors.
Digitalizing checklists
Also with a view to improving the effectiveness of preventive maintenance and the level of security in Seveso establishments, it would be useful to use digital checklists to monitor the level of security.
Indeed, the digitalization of checklists makes it possible to monitor their use and centralize the resulting data for better visibility and control of the overall security status. It also improves the level of reactivity to problems by notifying the right people to intervene at the right time without wasting time.
Giving operators the right tools
To perform their tasks properly, operators must be equipped with the right tools. The use of tablets allows operators to have immediate access to the information they need, fill out forms or even take pictures to report anomalies.
Having immediate access to work instructions allows operators to perform more efficient inspections. They focus on what they have to do and avoid unnecessary travel. Thanks to connected tablets, the operator would be able to access the latest version of industrial documentation as well as a more intuitive and understandable format that allows the operator to carry out tasks in the best possible way.
What is the solution?
Picomto is a software solution for industrial companies to digitize checklists and industrial documentation. Our solution allows operators to be more efficient in control and inspection tasks by immediately reporting problems to the right people. The digitization of operating procedures ensures instant access to the latest information and protection measures. For more informations, contact us.
Leave A Comment