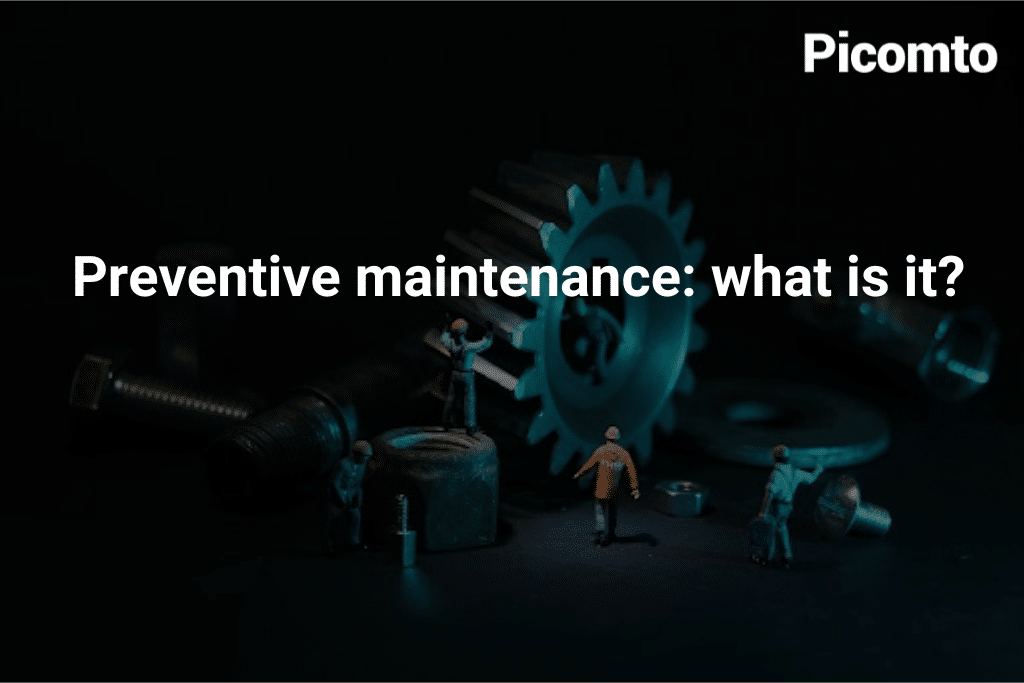
In general, we tend to neglect to do preventive maintenance work when a piece of equipment is working at full capacity. However, an incident is expected to occur at some point. The latter will inevitably lead to more expensive and more complicated repairs in the future.
Therefore, the best way to avoid any kind of breakdown is to implement a preventive maintenance plan within your organization. In fact, with this type of maintenance, you will avoid a minor problem becoming a major problem. This not only allows you to avoid equipment replacement costs and unplanned downtime but also to improve the safety of your workspace by reducing risks to your installation.
What is preventive maintenance?
Also known as planned technical maintenance, preventive maintenance mainly refers to any intervention on equipment at regular intervals or according to predefined criteria. Its main purpose is to reduce the risk of breakdown on goods, machinery and equipment. It also aims to achieve more general objectives. It is for this reason that most companies are looking to develop the preventive maintenance part compared to corrective maintenance.
What is the purpose of preventive maintenance?
As mentioned above, the primary objective of preventive maintenance is to reduce the risk of malfunction and to limit the number and frequency of machine breakdowns.
Through this goal, we seek to:
- Reduce the frequency of production shutdowns
- Reduce machine downtime for repair
- Optimize the service life of machines and equipment
- Plan corrective maintenance interventions to achieve in the best conditions
- Improve inventory management of spare parts
- Avoid unnecessary consumption of energy, lubricant and consumables
- Reduce maintenance budget
- Improve the working conditions of employees
- Reduce or eliminate the causes of serious accidents
- What are the different types of preventive maintenance?
There are 3 types of preventive maintenance:
- Systematic maintenance
- Conditional maintenance
- Predictive maintenance
Systematic maintenance
This type of maintenance is necessary from a criticality point of view concerning the first stages of degradation on a part of equipment. It can be carried out at predefined intervals or according to a criterion of use without taking into account the conditions of use of a machine. For example, the replacement of timing belt on a vehicle every 150,000 kilometers.
Systematic maintenance requires a solid knowledge of degradation rules. Therefore, it should be carried out in a reliable manner to avoid additional monitoring out of inspection periods and eliminate any further need for additional verification between interventions.
This type of equipment is carried out on equipment that does not require high costs for parts replacement. It mainly includes:
- Replacement of bearings, oil, springs, seals, resistors, lamps, contacts…
- Setting potentiometers, belt tension, pressure…
- Torque and level control
Conditional maintenance
This type of maintenance requires monitoring the operation of a machine according to certain parameters (pressure, level, debit…). Industrial maintenance operations will be scheduled according to the results of this monitoring. Conditional maintenance helps to overcome the drawbacks of systematic maintenance. For this type of maintenance, no additional knowledge is required.
Predictive maintenance
Predictive maintenance is carried out using estimates following analysis and evaluation of the machine’s parameters.
You should know that this type of maintenance is costly and requires sophisticated tools. It applies only to elements of important criticality from a safety and cost point of view.
In conclusion, the 3 types of preventive maintenance aim to limit the probability of breakdown. However, they do not prevent possible breakdowns between two interventions.
Why do we need a preventive maintenance plan?
Implementing a maintenance plan is important to apply the principles of preventive maintenance. In fact, it is important to know that planning is the ultimate key to respecting procedures that allow to predict the breakdowns.
A preventive maintenance plan is a document that comprises procedures, resources and planning of maintenance interventions on equipment or a machine.
It is important to follow certain steps in preparing a maintenance plan:
- Defining the scope of intervention
- Choosing the type (s) of preventive maintenance to be applied as well as the corresponding interventions
- Preparing a file gathering all the planned interventions as well as the information necessary to carry them out
How to create a sustainable preventive maintenance program?
Set your business goals
What are you waiting for to implement a preventive maintenance plan for equipment? The first step to making an effective plan is to set your goals. If you are willing to save money, you have to focus on maintenance that considers the age of your equipment, reduces labor costs and prevents breakdowns.
Set action parameters
In addition, you should bear in mind that there are many things to consider when you plan a preventive maintenance plan. In fact, it is necessary to set action parameters accurately so that you plan is as effective as possible. Among action parameters, we find the following interventions:
- Essential: this type of intervention comprises obligatory maintenance, equipment regulations and periodic control of machines and infrastructures.
- Of use: this concerns breakdowns and users’ feedback
- Recommended: what is recommended by the manufacturer
A qualified team
Implementing a maintenance plan is an effective solution but you still need to be able to apply it. It is important to have a qualified team to carry out preventive maintenance and to analyze and maintain your equipment.
Good communication is the key to success
Once you have a preventive maintenance plan in place, it is important to communicate it to your employees. It is essential that your employees know what will be achieved and when it will be carried out. Good communication ensures smooth maintenance and avoids extra work.
Leave A Comment