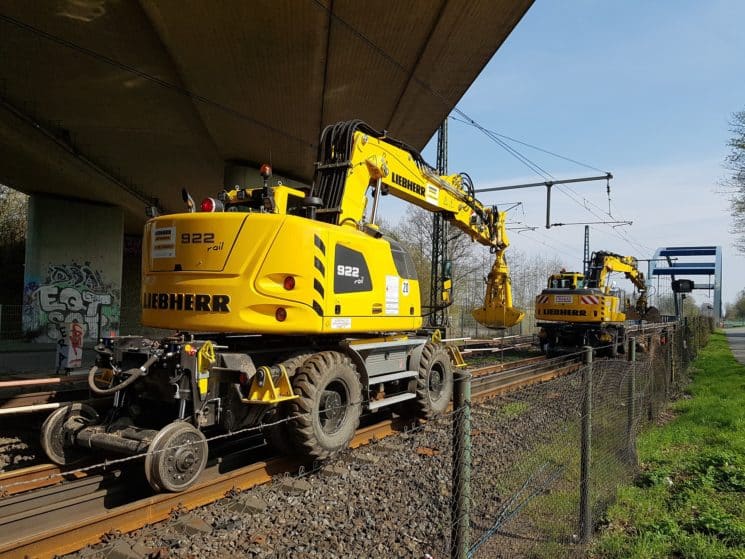
Total productive maintenance, which began in Japan in the early 1970s, was quickly exported, as the first experiments proved to be so successful. Today, this method is applied in most mass production industries. TPM is considered by many specialists as a real performance lever. However, to be fully effective, several conditions must be met, such as the right choice of equipment to target, the reliability and speed of data collection, and the involvement of staff.
Maximize productive time
Considered one of the leading developments in maintenance methods in modern industry, Total Productive Maintenance is based on the following principle: ensure the maintenance of machines without stopping production (or at least not slowing it down too much), taking into account all aspects related to production and involving all stakeholders in this approach.
Total Productive Maintenance has quickly conquered the major players in the industrial sectors in many countries around the world. It is interesting for organizations that produce small series and has a strong interest in making their expensive machines as profitable as possible.
Focus on preventive actions
For its implementation to be fully successful, it is necessary to work to ensure that all the conditions for success are in place.
Total Productive Maintenance requires, first of all, a perfect knowledge of machines, processes and work instructions. It requires optimal analysis and understanding of the data collected by the various sensors, taking into account vital criteria such as wear and tear, efficiency, etc. It is on the basis of this information, the collection and use of which is greatly facilitated by digital media, that preventive maintenance actions can then be planned. Anticipation is, in fact, one of the key factors in MPT, which is part of a proactive approach.
The aim is to set up an effective organization to anticipate breakdowns and malfunctions and to act before they occur.
Total Productive Maintenance aims to eliminate, as much as possible, waste as well as downtime, which greatly penalizes the company’s activity. At the same time, it is a question of hunting down elements that could alter quality. We, therefore, have here the three levers often cited by the apostles of the TPM: availability, performance and quality.
Greater involvement of operators
Among the conditions necessary for the success of a TPM approach, the involvement of staff is undeniably a crucial aspect. This concerns the driving forces of the industry at all levels; those belonging to top management (managers, planners and decision-makers) as well as those who operate in the field. Operators are an essential link in the chain, as they are the ones who know the production equipment best. As they operate and monitor them on a daily basis, they are ideally placed to identify the more or less significant sources of malfunction and the factors likely to improve their performance.
Maintenance teams are therefore encouraged to work closely with these employees to integrate the valuable information and feedback they can provide.
All this contributes to creating and strengthening a real corporate culture among employees. The resulting sense of involvement helps to motivate employees and thus make them more efficient as well.
About Picomto
Picomto is a SaaS software to create, manage, share and analyze maintenance procedures and procedures in a visual and interactive way.
Leave A Comment