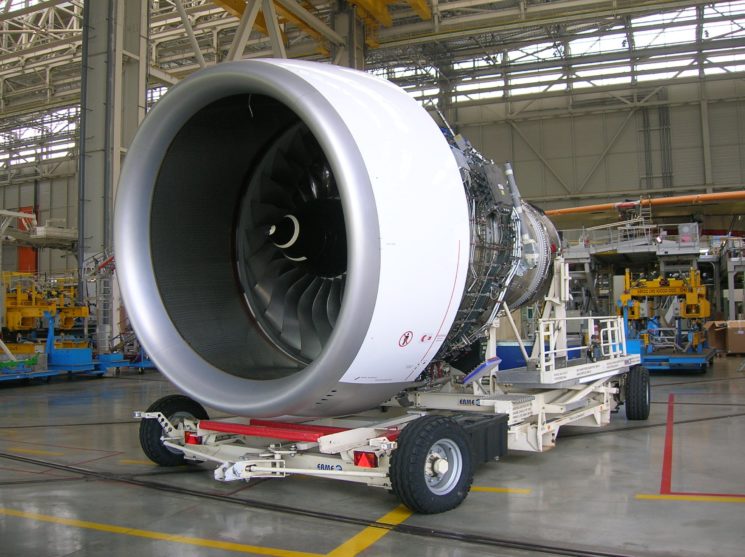
In industry, robots and software are now part of the landscape and continue to profoundly change production locations. These new and increasingly sophisticated tools redefine both the working environment and the way employees carry out their missions, including those related to maintenance. The monitoring of machines and infrastructure, as well as their maintenance in optimal working order, are the main beneficiaries of technological innovations, such as those related to the Internet of Things (IOT).
Remote monitoring
If there is one opportunity offered by new technologies that many industry stakeholders particularly appreciate, it is to be able to be informed of the state of the means of production and their performance without having to be present on site.
Thanks to solutions offered by start-ups and specialized companies, it is possible to have, on a terminal (laptop, tablet or even smartphone) connected to the Internet, precise data on the “health” of the equipment and its performance, but also to receive a direct alert in case of detected malfunction. All this by being far from the production site and having full freedom to set a number of parameters, such as alert thresholds, for example.
In this way, it is possible to react quickly by contacting the maintenance teams, transmitting the information collected to them to facilitate their work and save them time. This significantly reduces machine downtime and, therefore, reduces the impact of these downtime events on the company’s production.
Support during the interventions
Technological innovations provide improved means for intervention support when a maintenance operation is to be carried out.
Machine information and procedures to be followed to correct the different types of failures that may occur are directly available on digital media, which have the triple advantage of being less cumbersome, more practical (access to a given piece of information is facilitated) and more complete (large storage capacities).
As a result, the employees called upon to intervene, gain in efficiency and speed in order to quickly make the means of production available to operators.
Some designers go even further in this logic of connected maintenance, developing visual work instructions on different media. These high-tech gadgets, like the Polm Studio, XSED or GRDF models, allow field staff to exchange information in real time with geographically remote experts, allowing them to benefit from the shared vision so they can see the scene and guide operators during troubleshooting. Not to mention that employees who are in direct contact with the machines can, thanks to its visual work instructions, work with new media. These solutions are either currently being tested in companies or are already fully implemented.
Tools to better predict failures
In terms of preventive maintenance, innovations can also be considered as making it possible to make considerable progress in terms of efficiency and optimization of production capacities.
The central components of the new generations of machine monitoring systems remain sensors, which record vital data. These are then processed, analyzed and linked to reference values, such as the failure threshold of an equipment (for example, a number of hours beyond which a machine is likely to be damaged or become less efficient). The software component of this type of device then notifies users that the machine is approaching a possible failure and must therefore be subject to maintenance as soon as possible.
This makes it possible to plan interventions well in advance and to organize maintenance team rounds more efficiently.
The industry of the future and maintenance are undoubtedly destined to become more and more connected.
About Picomto
Picomto is a web and mobile software solution for creating, managing, sharing, viewing and analyzing visual work instructions.
Leave A Comment