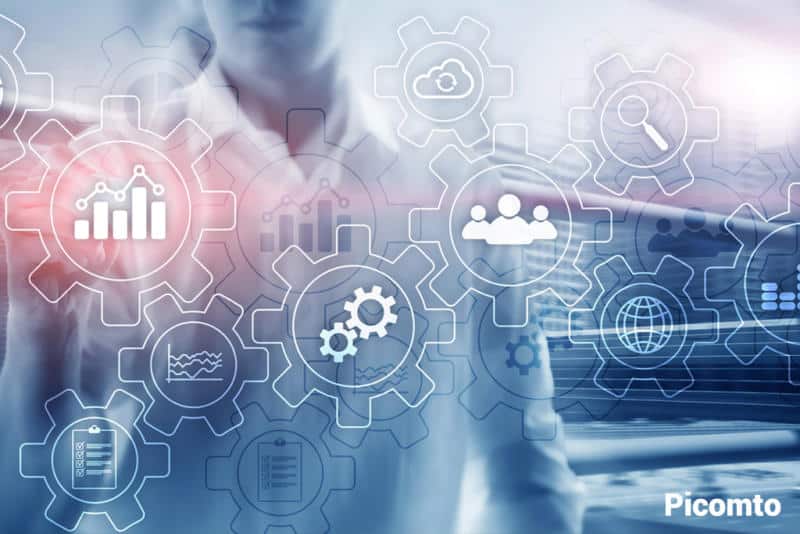
The connected factories that are emerging today in this digital age foreshadow the intelligent industry of the future of work. We are witnessing major transformations and innovations both in the way of production and in the organization of these structures. Innovative Smart Manufacturing techniques and processes, which integrate the tools offered by the IoT (Internet of Things), contribute to improving industrial performance at several levels.
Definition and explanation :
Smart Manufacturing, often abbreviated SM in reference works and referred to as “intelligent manufacturing”, refers to a new global industrial method that relies heavily on the evolutions of the latest technologies in terms of connected means of production during the manufacturing process.
In other words, it is a question of setting up systems in factories in which the machines are connected to each other, but also and above all to the Internet in order to ensure optimal and scalable control of production processes.
In a work environment that applies the principles of Smart Manufacturing, we seek to automate as many operations as possible so that they are carried out with maximum efficiency. The objective is to have them carried out more quickly, guaranteeing quality and profitability at a lower cost.
To do this, the central element of the type of organization is data analysis; collected directly from the equipment, it is digitally analyzed to enable the right decisions to be made and readjustments made to improve and optimize manufacturing performance.
Intelligent manufacturing is one of the applications of the IoT, or more specifically of the IIOT, which is the Industrial Internet of Things.
Smart Manufacturing: tools to support projection and improvement
In a plant structured according to the possibilities offered by Smart Manufacturing, production benefits, on the one hand, from better data acquisition and interpretation, and on the other hand, from improvements made possible by increasingly powerful simulation and projection digital tools.
The information (temperatures, speeds, fluid levels, volumes of raw materials used, etc.) collected by the sensors fitted to the machines are screened by specialists and digital officers such as data scientists. The latter analyses them using software specific to production process and planning.
This not only makes it easier and faster to detect sources of error, disruption, poor quality or slowness but also allows them to use this information to simulate processes and improve work instructions with any necessary modifications.
Which data is increasingly voluminous, and therefore hosted on often external media technologies such as the cloud. It is also one of the major characteristics of Smart Manufacturing, as is the interoperability between software. Indeed, it is essential that in such a system, the software solutions accompanying the machines can work together without there being any compatibility problems, for example. They can integrate common functionalities, collaborate and participate in ensuring communication between the means of production.
In recent years, with the emerging technologies, we have also seen the deployment of machines equipped with artificial intelligence that literally allow them to learn. They are thus able to learn from past operations themselves to readjust their behaviour. This is called machine learning.
Smart Manufacturing: Only possible thanks to people
This intelligent manufacturing is only possible if there are people such as technicians, behind to control this automation. To do this, they need digital and connected work instructions that can be accessed via high –tech tools such as tablets or connected glasses.
At Picomto, we adopt new technologies and develop business applications to digitize work instructions and standard operating procedures. Contact us for more information.
Leave A Comment