Have you measured the impact of a well-structured manufacturing process on your production? Indeed, the manufacturing process plays a fundamental role in optimizing production operations.
Through precise instructions and well-defined manufacturing orders, each workstation becomes more efficient, enabling time savings and better finished product quality. Picomto, through its digital solution, not only facilitates the creation but also the sharing and monitoring of these processes.
This structured approach also plays a key role in improving industrial machine durability by ensuring that equipment operates under optimal and consistent conditions.
In this article, we’ll explore how to digitize manufacturing processes to gain productivity and competitiveness in an industrial context.
I. What is a Manufacturing Process? Understanding the Basics
A manufacturing process is the backbone of any industrial operation. It describes each step, from initial machining to the finished product, including assembly and quality control.
This detailed structure of manufacturing steps enables precise task management. It organizes the sequence of operations at each workstation and facilitates product traceability throughout its lifecycle.
I.1. Definition of Manufacturing Process and Its Importance
A manufacturing process represents a sequence of technical instructions necessary to obtain a quality finished product.
In a production line, each workstation follows this process, including all manufacturing specifications, such as which machines and tools to use.
The advantage is clear: better productivity, simplified production monitoring, and increased traceability.
I.2. Difference Between Manufacturing Process and Work Instructions
Though similar, manufacturing processes and work instructions have specific roles. The process covers all production steps, while work instructions focus on specific tasks for each workstation.
Together, they ensure that components and sub-assemblies are efficiently assembled, enabling repetitive manufacturing in large or small series.
II. Components of an Effective Manufacturing Process
The performance of a manufacturing process relies on well-defined elements that, when properly integrated, enable efficient production management and rigorous quality control.
A well-constructed manufacturing process integrates resources, tooling, machine tools, and machining times to ensure each operation runs smoothly and without interruption.
II.1. Manufacturing Steps
Manufacturing steps form the heart of a manufacturing process.
From raw material cutting to sub-assembly assembly, each phase is crucial for obtaining a finished product that meets expectations. Precise documentation of manufacturing steps facilitates production monitoring and improves inventory management by avoiding stockouts.
II.1.1. Raw Material Cutting
Cutting is often the initial step, involving the use of machines such as saws or CNC machines to process raw materials. This step is essential for preparing components to specific required dimensions.
For example, in mechanical parts manufacturing, precise cutting ensures perfect assembly of sub-assemblies and reduces error margins.
II.1.2. Part Preparation and Finishing
After cutting, parts go through finishing processes such as drilling, deburring, or polishing. This step is crucial for obtaining smooth surfaces ready for final assembly.
Equipment such as drills and grinders are often used at this stage to ensure optimal finish quality and precise tolerances.
II.1.3. Sub-assembly Assembly
Sub-assembly assembly combines multiple parts into a functional unit.
In the aerospace industry, for example, this step is particularly critical, as each sub-assembly must comply with safety standards. Good production monitoring at this level ensures each part integrates perfectly into the final product.
II.2. Required Equipment, Machines, and Tools
The equipment and machine tools used in a manufacturing process play an essential role in the precision and efficiency of each operation.
II.2.1. Using Precision Machine Tools
Precision machine tools, such as CNC milling machines and lathes, are essential for ensuring high tolerances and precise dimensions. These machines are used in high-precision industries like mechanics and aerospace.
For example, a CNC lathe can machine parts to exact required dimensions, thus reducing rework needs and increasing productivity.
II.2.2. Specific Tools for Each Step
Each manufacturing step may require specific tools, such as drilling jigs or clamping devices, to hold parts in place and ensure stability during operations.
These tools contribute to precise task execution and facilitate operators’ work by reducing error margins.
II.2.3. Quality Control Machines
Quality control is an essential part of the manufacturing process.
Measuring equipment, such as gauges and micrometers, allow verification of part dimensions and ensure compliance with manufacturing file specifications. Meticulous inspection at each step helps detect defects before products are assembled.
Attend our webinar on equipment maintenance management!
III. Why is the Manufacturing Process Essential for Productivity?
Optimizing resources and costs through a well-designed manufacturing process improves industrial operations’ profitability. It also contributes to waste reduction and better finished product quality.
III.1. Resource and Cost Optimization
With a clear manufacturing process, production costs are reduced. Each step is precisely defined, allowing optimal scheduling.
Industries that automate this process using ERP or production management software see a reduction in raw material costs and production time.
III.2. Improving Finished Product Quality
The manufacturing process often includes quality controls for each operation.
By digitalizing this step with tools like Picomto, production managers ensure real-time monitoring. This guarantees product conformity and customer order satisfaction.
IV. Creating a Digital Manufacturing Process with Picomto
Digitalizing your manufacturing process enables efficient monitoring and reduces human errors.
With Picomto, each operation becomes accessible and visual, facilitating understanding of operating procedures.
IV.1. Process of Creating a Manufacturing Process with Picomto
Creating a digital manufacturing process with Picomto takes just a few clicks.
By integrating technical data, visual instructions, and safety procedures, operators can work confidently with visual tools at their fingertips.
IV.2. Real-time Collaboration and Sharing
Thanks to Picomto’s features, teams can instantly share information about operational processes.
This connectivity ensures better responsiveness and allows operators to consult the latest updates without delay, even on mobile devices.
V. Benefits of Digitalizing Manufacturing Process with Picomto
A digitalized manufacturing process offers undeniable advantages in terms of precision, traceability, and productivity. It enables real-time monitoring and integrated quality controls.
V.1. Reducing Human Errors and Optimizing Monitoring
Digitalization reduces the risk of human errors and improves monitoring of each manufacturing step.
Thanks to the traceability ensured by Picomto, errors are spotted earlier, limiting waste and delays in customer orders.
V.2. Integrating Quality Controls into the Process
Adding quality controls at each step of the process allows quick detection of manufacturing defects.
Picomto offers the ability to monitor each operation in real-time, ensuring finished products comply with customer specifications.
Conclusion
In summary, an optimized manufacturing process is crucial for improving productivity and reducing costs in business.
It also plays a central role in effective manufacturing operations management, ensuring consistency, traceability, and performance across all production stages.
Additionally, a well-structured and digitalized manufacturing process actively contributes to Industrial Risk Prevention by standardizing operations and reducing the likelihood of human error or process deviation.
Thanks to Picomto’s digital solution, companies can create, manage, and share precise and visual manufacturing processes.
Contact Picomto today to discover how our solutions can transform your production process.
FAQ
1. What is a manufacturing process?
A manufacturing process is a document detailing each step necessary for product creation, including operations, machines, and production times.
2. Why digitalize a manufacturing process?
Digitalization improves traceability, reduces errors, and enables real-time monitoring. It also facilitates information access and optimizes productivity.
3. What are the differences between manufacturing process and operating procedure?
The manufacturing process describes all global production steps. The operating procedure details specific procedures for each specific task.
4. How can Picomto help optimize manufacturing processes?
Picomto enables digitalization, sharing, and real-time monitoring of manufacturing processes, making procedures more efficient and accessible.
5. What are the advantages of a well-structured manufacturing process?
A well-structured process optimizes resources, reduces costs, and ensures finished product quality through better operation control.
6. How does digitalizing a manufacturing process help reduce human errors?
By digitalizing information, operators can access the latest instructions and updates in real-time, thus minimizing error risks.
7. What digitalization tools does Picomto offer for manufacturing processes?
Picomto offers a digital management platform for creating, sharing, and analyzing manufacturing processes with visual instructions and real-time monitoring.
8. How does manufacturing process digitalization impact inventory management?
A digital process helps better anticipate needs and optimize inventory management, reducing surplus and stockouts.
9. Is digitalization suitable for small businesses?
Yes, Picomto adapts to SME needs by offering scalable solutions that are easy to integrate into production environments of all sizes.
10. Which industries can benefit from manufacturing process digitalization?
All industries, from aerospace to food processing, can benefit from process digitalization to improve quality and productivity.
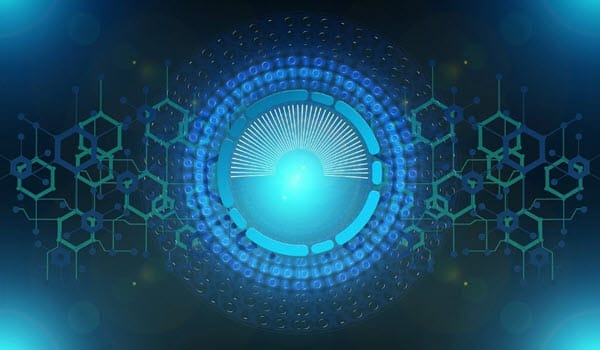
Leave A Comment