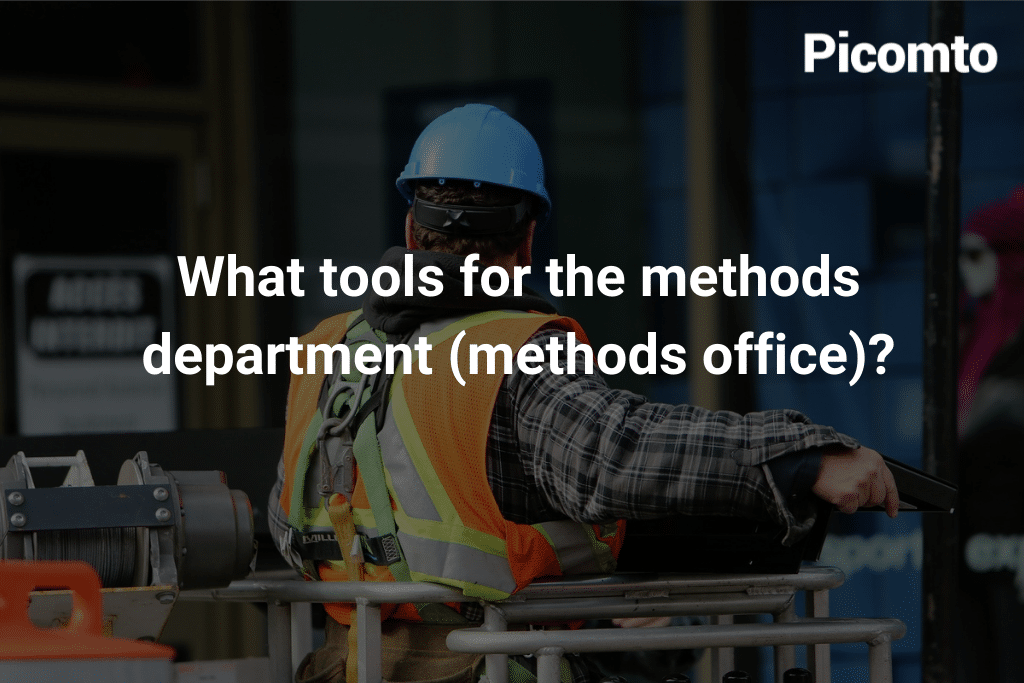
The methods department or the methods office is considered as one of the essential pillars of industrial companies’ development. It connects with lean management techniques so that the company keeps its competitiveness in an evolving market. It is the interface between the production line and the design office.
The methods cover the technical as well as the organizational aspects of industrial production. Let’s discover the major tools they use.
Work instructions software
In the industrial environment (aeronautic for example), operating modes are the main guarantees of quality production of new products and safe work environment. Therefore, they require special attention in their drafting, optimization and presentation to operators (technicians or engineers).
During the digital transition, paper work instructions are outdated to make way to digitized operating modes.
work instructions software is a powerful tool that allows to draft, update and share operating modes while collecting data pertaining to their use (technical solutions, manufacturing processes, manufacturing methods, production means…)
The method engineer, the method manager and the industrial method technician save a lot of time by using software for the design of these documents.
Method engineers also provide employees with clear and precise instructions that reduce non quality.
Kaizen and continuous improvement
Kaizen is a continuous improvement tool that is based on small improvements that are simple to implement by methods. This philosophy tends to make small improvements that affect the space and working conditions, production and delivery deadlines, quality of produced parts and of course productivity of all operators by focusing on simplification of processes.
The Kanban Method
It is a production management and knowledge sharing method that is based on the organization of tasks’ distribution. In fact, Kanban requires to start with the tasks already in progress and the implemented processes while stimulating cumulative changes.
In fact, this method relies on employees’ understanding of the need for evolutionary, continuous and increased changes in the continuous improvement of production process. Accepting changes here is a key factor in the success of methods. Abrupt and imposed changes are more often rejected by teams. The latter are afraid of big changes. For this reason, the Kanban method requires small changes yet evolutionary and continuous.
Implementing such working methods is facilitated when each employee respects their role and responsibilities. In addition, good leadership at all levels of the company builds trust and eliminates fear that can slow down improvements.
Process implementation and adherence
Implementing clear and effective processes is the role of the company’s administration that anticipates its needs and analyzes its operation. In fact, process development is carried out in close collaboration with all hierarchical levels of the industrial company. Data assembly, centralization and analysis that come from the application of processes at the level of the production chain help to imagine and implement process improvement. This is in the aim to make the company more productive and not lose in competitiveness.
Digitalization of Methods!
The Methods department is based on planning and monitoring processes of the continuous improvement. To make it realistic, the digitalization of tools is necessary. In the framework of their transformation, industries must privilege connected work stations that foster teamwork and continuous exchange between various employees (production manager, production teams, head of department, engineer, technicians, team leader, workshop manager…)
For example, industries that are looking for productivity improvement, efficiency and cost reduction should make digital work instructions software available to employees at the Methods department. If you want to know more about digital work instructions software, just contact us.
Leave A Comment