En matière de culture d’amélioration continue, le Kaizen est une véritable référence. Bien plus qu’une méthode, c’est une philosophie. Un savoir être même. Le Kaizen fait appel à toutes les ressources de l’entreprise et à toutes les compétences : c’est un catalyseur d’amélioration continue.
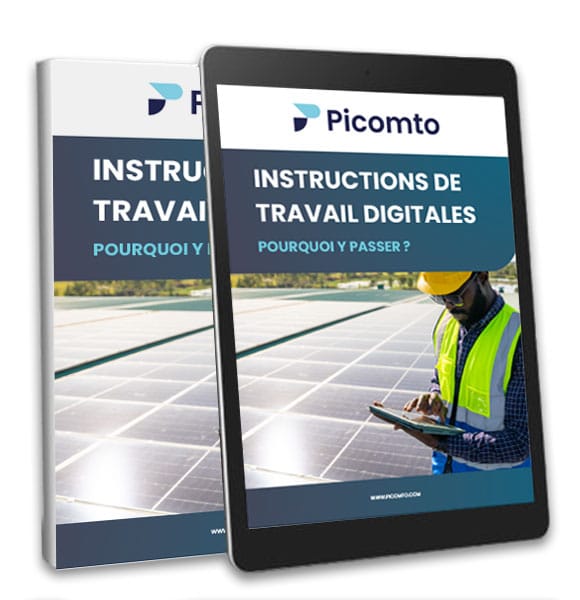
voyages évités chaque semaine
gagnés chaque année
La Philosophie Kaizen
L’esprit Kaizen est né à la fin de la Seconde Guerre Mondiale au Japon. Soulignons qu’il est au cœur du lean manufacturing et du lean six sigma chers à Toyota. En effet, il a été rapidement adopté dans l’industrie automobile où Toyota en a fait la pierre angulaire de son développement. Le mot Kaizen est la contraction de deux termes japonais, Kai (Changement) et Zen (Meilleur).
Par extension, on entend par Kaizen «démarche d’amélioration continue » ou encore système de management de la qualité.
Le Kaizen est une philosophie qui implique tous les acteurs de l’entreprise (travail d’équipe) et un plan d’action clair et précis. Du directeur à l’ouvrier. En effet, pour que le Kaizen existe dans une usine par exemple, il faut que chaque intervenant se l’approprie dans son poste de travail.
Ce n’est pas une technique que l’on applique, c’est un état d’esprit dont on s’imprègne. Pour cela, le Kaizen va s’appuyer sur le savoir être de chaque membre de l’entreprise : sa propension au changement et sa capacité à le mener à bien.
C’est pourquoi, la philosophie Kaizen pourrait se définir ainsi : « Se réinventer constamment pour toujours s’améliorer ». Car le Kaizen ne se contente jamais d’une situation existante.
Découvrez comment des entreprises comme Veolia utilisent la philosophie Kaizen pour optimiser leurs processus. Lire l’étude de cas.

La prise de conscience, le levier Kaizen
Le Kaizen, dans une entreprise, se met en place en douceur et par petite touche selon les résultats obtenus. Pour cela, il va faire levier sur trois axes :
- Savoir-faire (compétences et besoins en compétences) ;
- Savoir être (écouter, comprendre, analyser et intégrer) ;
- Faire Savoir (communiquer et transmettre).
Il s’agit ici de réaliser un audit complet de la structure : processus, systèmes, qualité, ressources humaines. Ces audits permettront une prise de conscience globale et individuelle des axes d’amélioration (démarche qualité).
Ils permettront aussi d’identifier les éventuels problèmes opérationnels de fonctionnement et de les adresser. Une fois l’étape de l’audit réalisée, le Kaizen, à proprement parler, pourra se déployer.
En effet, un Kaizen qui améliorerait la gestion de la qualité de la production en se contentant uniquement de régler les problèmes manquerait son objectif. Le but premier de cette philosophie est l’amélioration continue, pas la résolution de problème. Il s’agit donc d’une approche proactive plutôt que réactive.
Il faut savoir que le bureau des méthodes, étant l’interface entre la production et le bureau d’études, il est en mesure de garantir le bon déroulement des processus.
Participez à notre webinar pour découvrir comment intégrer le Kaizen dans votre stratégie d’amélioration continue. Inscrivez-vous ici.
Les outils du Kaizen au service de la qualité
Le Kaizen s’inscrit en douceur dans l’ADN de l’entreprise et des individus qui la composent. Il fait appel au savoir-être de chacun.
Pour « alimenter » ce savoir-faire et tendre vers le savoir être, il existe plusieurs outils ou méthodes de travail permettant d’assurer l’amélioration continue de la qualité.
Nous en citerons 4 outils :
La Méthode 5 S
Sans doute c’est la meilleure porte d’entrée pour le Kaizen. Cette méthode d’origine japonaise permet de prendre conscience de façon simple des axes d’amélioration continue des processus de production, de l’environnement de travail et des postes de travail. Améliorer de manière continue et en suivant de petits pas, l’entreprise pourrait atteindre l’excellence opérationnelle et assurer la satisfaction des clients. Le management des unités de production joue ici un rôle prépondérant dans l’amélioration de la performance.
Les « 5S » de cette méthode représentent 5 actions correctives déterminantes pour améliorer la productivité et l’efficacité d’une entreprise : Seiri (éliminer), Seiton (Ranger), Seiso (nettoyer), Seiketsu (Maintenir l’ordre) et Shitsuke (être rigoureux).
La roue de Deming
Très visuelle et facilement mise en place, cette méthode d’amélioration développée par William Edwards Deming identifie les 4 axes de l’amélioration de la qualité : prévoir, faire, vérifier et réagir. La roue de Deming complète parfaitement la méthode 5S, car elle permet de mettre en œuvre de façon concrète ce que le 5S définit en théorie. Il s’agit d’un outil de management visuel qui permet de mettre en place des plans d’actions d’amélioration continue.
Le Kaizen est une philosophie qui met le savoir être au cœur de l’amélioration continue. Intégrée par petite touche à la culture de l’entreprise, la culture d’amélioration des processus a un impact conséquent sur la qualité de la production, la résolution de problèmes et la productivité.
Mais le Kaizen ne s’apprend pas, il s’approprie. C’est une remise en question quotidienne qui ne se satisfait jamais d’une situation existante.
Les 3M (les trois types de gaspillage)
Il faut souligner que la réduction des gaspillages est également au cœur du principe d’amélioration continue. Cela se concrétise par l’application des 3M. Cela fait principalement référence aux 3 sources de gaspillages :
Muda
Il s’agit ici de toute activité n’important aucune valeur ajoutée dans un lieu de travail. Généralement, nous parlons des 7 mudas :
- Temps d’attente inutiles
- Transport inutiles
- Traitement inutiles
- Surproduction (stock dormant)
- Surstockage
- Mouvement inutile
- Non qualité (défaut des pièces ou un service incomplet)
Mura
Cela renvoie aux irrégularités dans les processus de fabrication. Par exemple, nous trouvons des variations dans le système de production d’un produit ou d’un service.
Muri
Une autre source de gaspillage, c’est les difficultés soudaines pour effectuer une tâche (méthodes et outils non adaptés ou une formation insuffisante). Notons que cela engendre une surcharge et des efforts supplémentaires inutiles.
Le Kanban
Se basant sur l’approche de Lean management, cette méthode de gestion de flux de production vise principalement à réduire les délais de production et améliorer la réactivité des équipes. Reposant sur la méthode du juste-à-temps, il s’agit d’une méthode visuelle facile à comprendre par tous. En effet, on communique l’information aux opérateurs, et ce de manière ponctuelle afin de ne pas les surcharger de données inutiles.
Découvrez comment Picomto peut vous aider à structurer vos processus Kaizen grâce à des instructions de travail digitales. En savoir plus.
À propos de Picomto
Picomto est la solution pour créer, gérer, partager, consulter et analyser des instructions visuelles de travail. Notre solution logicielle vous permet d’exploiter les outils d’amélioration continue, collecter les suggestions des opérateurs, piloter le processus d’amélioration continue et assurer la satisfaction client.
On peut vous accompagner dans la mise en place d’une stratégie d’amélioration continue. Contactez-nous pour en savoir plus : Planifiez un appel.
Vous souhaitez en savoir plus sur l’intégration du Kanban dans votre entreprise ?
Contactez-nous pour discuter avec nos experts.
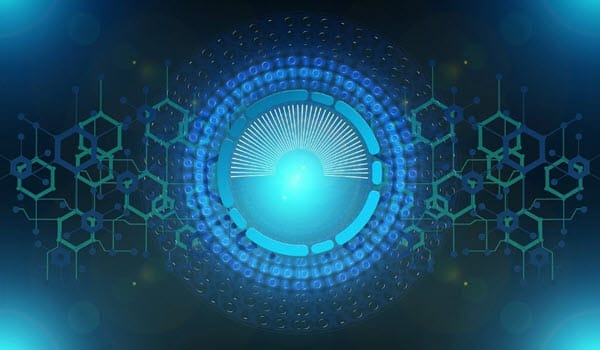
Laisser un commentaire