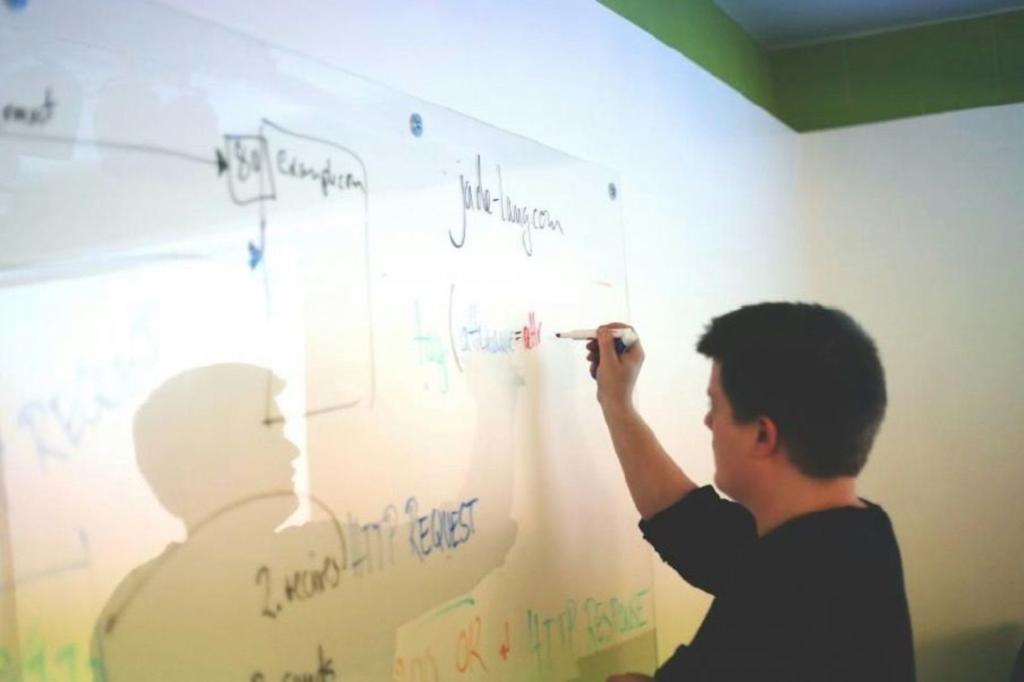
In terms of continuous improvement, Kaizen is a reference. Much more than a method, it’s a philosophy. It uses all the resources of the company and all skills: It is a catalyst for continuous improvement.
The Kaizen Philosophy
Kaizen was born at the end of the Second World War in Japan. It was quickly adopted in the automotive industry where Toyota has made it the cornerstone of its development. The word Kaizen is the contraction of two Japanese terms, Kai (Change) and Zen (Best).
By extension, Kaizen means “continuous improvement”.
Kaizen is a philosophy that involves everyone in the company. From the director to the worker. Indeed, for the Kaizen to exist in a factory for example, it is necessary that each speaker is appropriate.
It is not a technique that we apply, it is a state of mind that we are impregnated. For this, the Kaizen will rely on the knowledge of each member of the company: its readiness to change and its ability to carry it out.
This is why the philosophy of Kaizen continuous improvement could be defined as: “To constantly reinvent oneself to always improve“. Because the Kaizen is never satisfied with an existing situation.
Awareness, the Kaizen lever
The Kaizen in a company is set up smoothly and by little touch. For this, he will leverage on three axes:
- Know-how (skills and needs of skills);
- Interpersonal skills (listening, understanding, analyzing and integrating)
- Communication skills (communicate and transmit).
This involves performing a complete audit of the structure: processes, systems, quality, human resources.
This audit will allow for a global and individual awareness of areas for improvement.
It will also identify any operational problems and address them. Once the audit stage is completed, the Kaizen itself can be deployed.
Indeed, it that would improve the quality of production by simply solving problems, would miss its objective. The primary purpose of this philosophy is continuous improvement, not problem solving. It is therefore a proactive rather than a reactive approach.
Tools at the service of quality
The Kaizen fits smoothly into the DNA of the company and the individuals that compose it. It appeals to everyone’s savo irre but is based on know-how.
To “feed” this knowledge and tend towards interpersonal skills, there are several tools or methods. We will mention two:
Method 5 S
Without doubt the best gateway to the Kaizen. This method of Japanese origin makes it possible to become aware in a simple way of the axes of continuous improvement of a production unit.
The “5S” of this method represent 5 decisive actions to improve the efficiency of a company:
- Seiri (eliminate)
- Seiton (organize)
- Seiso (clean)
- Seiketsu (Maintain order)
- Shitsuke (be rigorous).
Deming wheel or PDCA
Highly visual and easily implemented, this method developed by William Edwards Deming identifies the four areas of quality improvement: plan, do, check and adjust (PDCA). The Deming wheel perfectly complements the 5S method because it makes it possible to concretely implement what the 5S defines in theory.
Kaizen is a philosophy that puts knowledge at the heart of continuous improvement. Integrated by small touch to the culture of the company, it has a significant impact on the quality of production.
But Kaizen can not be learned, he appropriates himself. It is a daily questioning that is never satisfied with an existing situation.
Digital Work Instructions are part of continuous improvement. They allow operators to collect and gather data to improve processes, which is consistent with the Kaizen Philosophy.
Contact us to know more about Digital Work Instructions software.
Leave A Comment