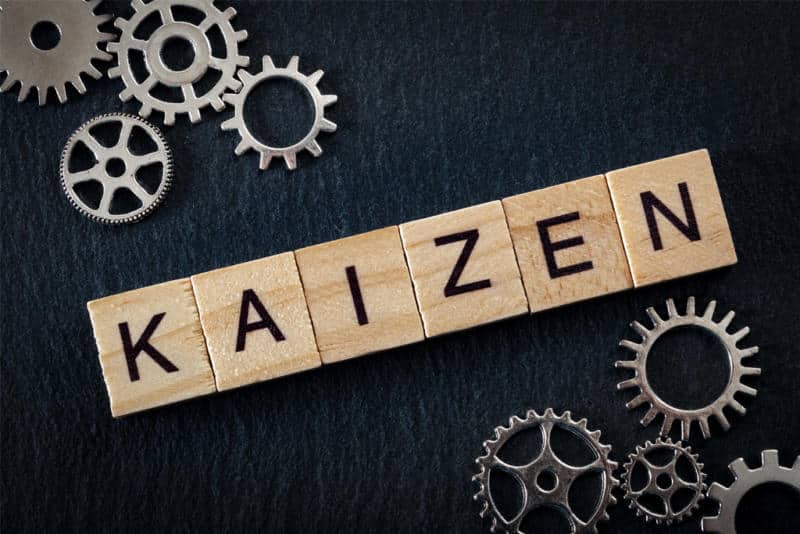
Improvement is a rigorous process that consists of optimizing products, services and industrial processes within factories. Efforts can be spread over specific interventions at specific intervals or grouped together for global implementation. Kaizen is one of the most widely deployed continuous improvement systems in industry 4.0. Let’s find out everything you need to know about this system and its efficiencies!
Definition of Kaizen
Kaizen is a Japanese word. It can be considered as quality management and continuous improvement system that was created and tested for the first time at Toyota in Japan. The particularity of this process improvement is that it is based on the involvement of all the links in the production chain in the continuous improvement process rather than on financial investments.
Kaizen thus involves employees, managers and non-managers by asking them to have a brainstorming to propose ideas and to improve quality, productivity and lean manufacturing. Small changes are implemented every day in a continuous way allowing the industrial company to optimize its management, productivity, products and profitability.
The tools of the Kaizen system
The 5S method:
Developed by the Japanese, particularly within Toyota production system, the 5S method consists of continuously implementing small improvements that affect the various organizational processes.
- SEIRI (tidying up): It concerns the layout of the workstation by arranging the space in such a way as to eliminate tools and materials that the worker does not use to perform his or her daily tasks.
- SEITON (put in order): Customize storage spaces to give each object a space adapted to its shape and functions.
- SEISO (clean): Improve the quality of the working environment by taking care of its cleanliness. After the work tools have been properly stored, the station must be owned to ensure the operator’s comfort.
- SEIKETSU (care): Take care of the workstation as rigorously as possible during the previous steps so that any operator can find what he or she is looking for.
- SHITSUKE (follow procedures): Compliance with previous procedures is essential to achieve continuous and ongoing improvement. Generally, a person is designated to ensure that procedures are followed as part of the chain management.
The SMED method :
SMED is the abbreviation for Single Minute Exchange of Dies. This method strives to reduce the time required to changeovers in order to optimize the minimum batch size.
The TQM (total quality management) method
This quality management approach aims to involve the entire company in order to use lean practices, reduce waste and improve output. The TQM approach makes it possible to mobilize all employees and human resources by involving them in the continuous improvement process.
Lean management
What is lean? It is a production management method that revolves around lean management. Lean management also concerns all the company’s departments and services that ensure the elimination of any waste and inefficiency.
The advantages of the Kaizen system
The Kaizen system touches on the different aspects of business management. It thus allows manufacturers to apply a low-cost and highly efficient continuous improvement model. From workstation continual optimization to administrative management and waste management. The Kaizen system makes it possible to improve working conditions, thus boosting productivity and ultimately quality improvement and perfection.
Which continuous improvement solution?
Picomto is a digital work instruction solution that provides operators with a communication tool to report field information and feed continuous improvement processes. Feel free to contact us for more information.
Leave A Comment