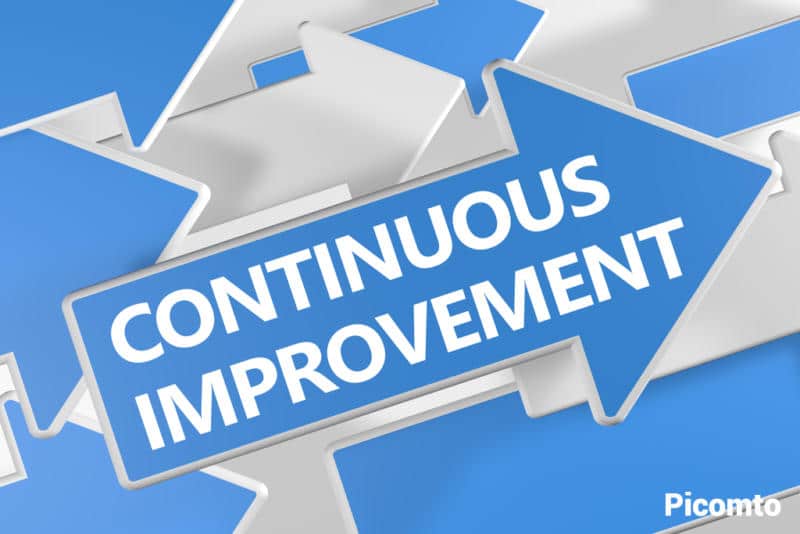
The continuous improvement process is an approach implemented by the company to improve its operations, products and services. The approaches chosen thus vary according to the company’s objectives and resources. However, in order to implement a personalized continuous improvement strategy, manufacturers must collect all the necessary data. They make it possible to feed this process, redesign it and customize it according to needs. Many technologies are involved to facilitate the collection and use of data as part of the optimization of the continuous improvement process. The connected plant will thus be able to evaluate its performance and take the necessary decisions to improve it and sustain it. All this is based on communication between the man and the machine in a connected universe.
Let’s discover how to collect, analyze and use data for continual process improvement!
How to collect industrial data ?
The connected plants generate huge volumes of data on the different operational levels. The information generated by machines, workers, products and consumers can all be used for continuous improvement planning. Thus, and to avoid any loss of data, manufacturers can opt for data collection initiatives and solutions. For example, the use of digital forms facilitates data entry by operators and quality managers and facilitators. Then, all this information must be centralized and stored correctly. Storage must therefore be secure to prevent what is known as a data leak.
Many industrial companies choose to store their data in cloud solutions, providing instant access to information. In this way, industrial data is easily collected from connected objects.
The processing of industrial data for continuous improvement
As far as continuous improvement is concerned, the information collected at the various links in the production chain is of extreme importance. Although some continuous improvement schools and Lean Management principles target factors that affect performance such as waste elimination and rework, other maintenance ongoing improvement methodologies and strategies are based on indicators returned by operators and machines.
Thus, depending on the purpose, the data collected will be processed systematically to prioritize and facilitate decision-making.
Data analysis is thus carried out by algorithms that use machine learning to make the right decisions. To support operational performance, agile and disciplined manufacturers must constantly communicate with data collection and analysis systems to implement the right efforts and decisions.
Let’s summarize!
Continuous improvement within the industrial company is a project team. It requires the involvement of all employees, practitioners, plant operators as well as those in charge of decision-making and organizational spheres. They facilitate the collection of data essential for situation analysis, strategy definition and decision-making. The digitization of forms facilitates data entry and process automation. By using machine learning technologies, the analysis of the large volumes of data collected is carried out in a short period of time and thus ensures efficiencies.
Which solution to implement ?
Digital work instruction softwares such as the Picomto solution gives workers a tool to facilitate data collection and centralize it automatically to feed the continuous improvement process. You can contact our experts for more information on this.
Leave A Comment