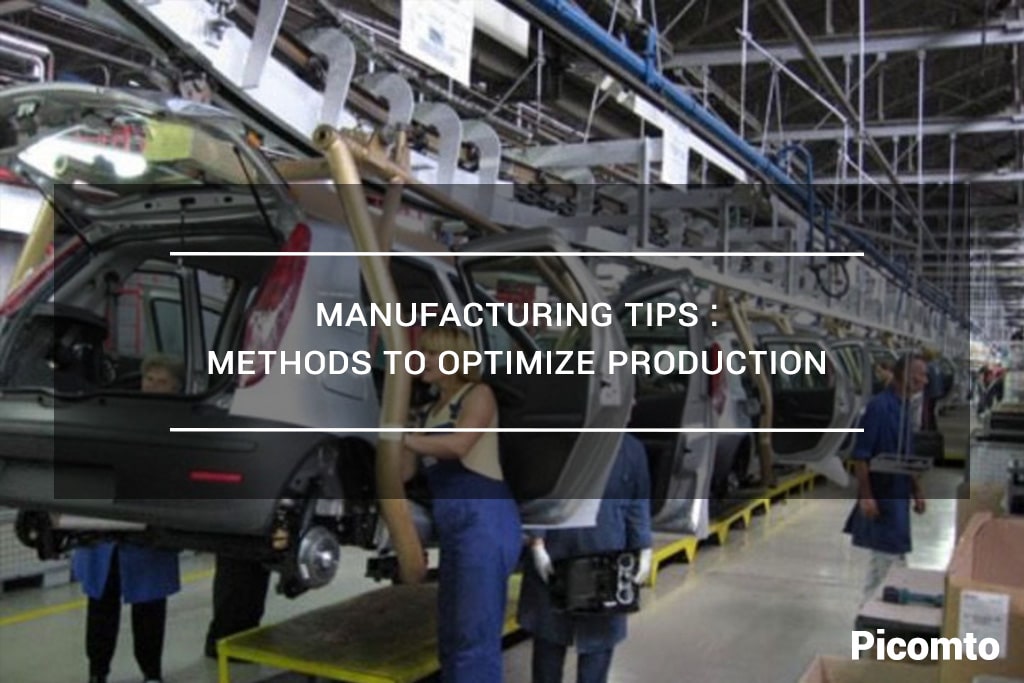
Faced with an increasingly evolving and highly competitive environment, today’s industry needs to make every effort to continually improve its competitiveness. To achieve this, there are management methods specifically designed to optimize production. Skills, information, customer expectations and quality are the pillars on which they are built.
While most of these approaches are new, some inherit processes that have been in place for several decades.
Develop in-house capabilities
This is particularly the case of the Training Within Industry (TWI), which was born during the 2nd World War in the United States. The US military industry needed to train a large number of employees and supervisors in a short period of time to meet the enormous need for complex warfare equipment. A strategy that has achieved considerable levels of productivity and quality. But nowadays, it is used in various sectors of the industry.
To improve the staff’s skills, the company implementing the TWI approach is developing these four areas:
- Work instructions: train supervisors so that they can train employees themselves after having duly incorporated the different aspects of the production process
- Working methods: improving working methods, and therefore productivity and quality
- Work Relationships: improving Employee Management to Prevent Problems
- Continuous improvement: implement a program to optimize production processes on a continuous basis
Optimize the exploitation of knowledge
In industry, access to information and its proper use are the keys to reach performance. It is on this principle that Knowledge Management is based. This approach includes all the tools, processes and resources to share the knowledge circulating within the company, but also to ensure the best possible use of information from outside.
It is thus as much to collect and to exploit a maximum of data having a real value that not to collapse under useless information.
Knowledge Management which is essential for smart manufacturing is carried out in five major phases: the identification of knowledge, their preservation, their valuation, their creation and sharing, and their updating.
Support productivity and efficiency
Another approach to optimize production, the Lean Six Sigma approach is the merger of two others. On the one hand, the Lean method focuses on reducing non-value-added tasks. It’s simplifying processes, improving fluidity and flexibility and, ultimately, increasing value for money for the customer. On the other hand, the Six Sigma method emphasizes the reliability and repeatability of processes by reducing their variability.
Thus, by merging the two approaches, the Lean Six Sigma method proposes to support productivity while promoting quality.
Focus on quality
In the world of industry, the establishment of a QMS (quality management system) is also part of the methods of optimizing production. Again, the ultimate goal is customer satisfaction through the implementation of an organization involving a variety of resources.
The 8 fundamental principles that determine the success of a QMS are :
- Leadership
- Employee involvement
- Continuous improvement
- System approach management
- Process approach
- Factual approach to decision making
- Customer focus
- Mutually beneficial supplier relationships
When this system is in line with the specificities of the company, it is a real booster for quality, performance and customer satisfaction.
What software solution to optimize production ?
Picomto is a digital work instructions software that helps industrial companies digitizing operational documentation and sharing knowledge within the shop floor. To know more about how we can help you, contact us by clicking on this link.
Leave A Comment