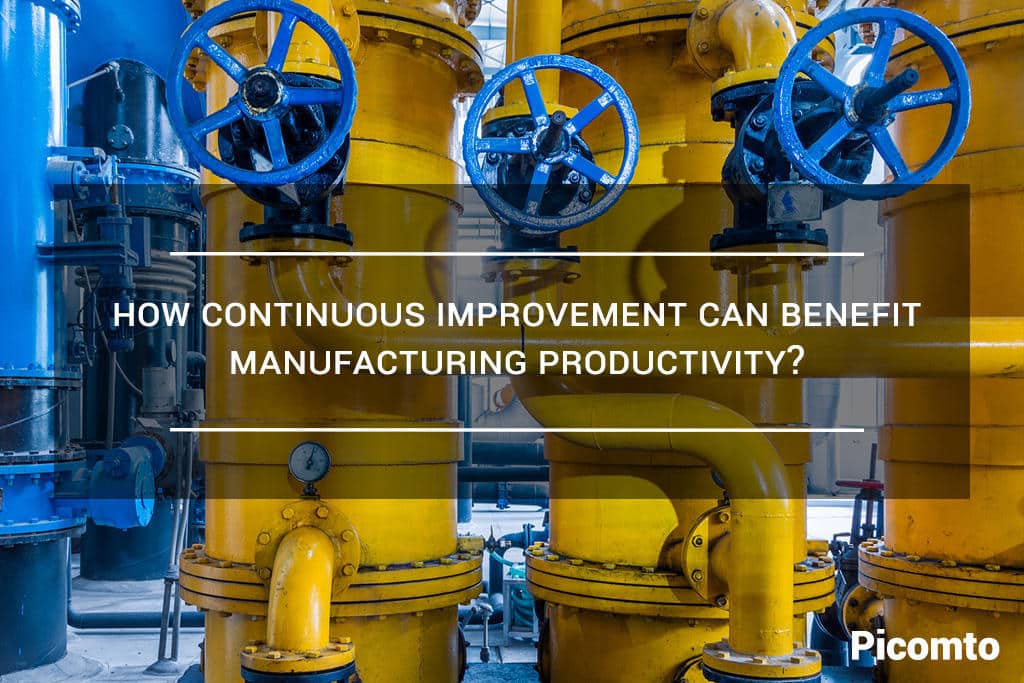
The concept of productivity matches the relationship between the production of goods and the means (human, material, financial and organizational) necessary for its realization. It constitutes one of the fundamental stakes for any actor in the industry.
Maximizing it is the permanent goal of any industrial companies, whatever the nature of his activity and the type of good. Among the main levers implemented for this purpose, continuous improvement undeniably occupies a preponderant status, especially as it aims for optimum efficiency, practicability, flexibility of processes and perfection. The elimination of the elements generating inefficiency and the evolution of the managerial culture is the major axes.
Eliminate anything that can stop the production
The essence of continuous improvement in the industry and one of its best-known methods is Lean Management. So, what is lean method? It lies in the elimination of anything that can contribute directly or indirectly to alter production, fluidity and performance.
A whole organization is thus set up to hunt for undesirable factors, obstacles and constraints to productivity. This is, to use Japanese terminology as coined by one of the most prominent Japanese companies, Toyota Production System, the:
- Muda (worthless transactions, wastage, stocks, corrections, retouching)
- Muri (excess, overloads)
- Mura (variability, irregularity).
The goal is to have a smoothly efficient production, without waste, defects, unscheduled interruptions, and unnecessary actions. This will also allow having optimal automation and standardization.
The search for performance is pervasive in any policy of continuous improvement in the industry. It covers productivity, quality improvement, time and cost, all of which are progressively improved to maximize overall add-value for the customer.
For this, different techniques and tools can be deployed which will improve reactivity when problems are encountered:
- the 5S
- the VSM (Value Stream Mapping – value chain analysis, physical flows and production run times)
- KPI (Key Performance Indicators)
A necessary change of managerial culture
For the continuous improvement process to be successful and truly prioritize and support productivity, it is necessary to adapt management, mentorship and the workforce including all employees from practitioners to facilitators and supervisors.
It is a totally different managerial culture that needs to be promoted. It relies on the development of employees’ skills, their greater involvement and the sustaining motivation to improve their problem-solving skills.
The leader must, therefore, show its personal commitment and exemplarity to ensure that staff are fully aware of the crucial role of the culture of continuous improvement in the organization. He must also provide employees with the means to be more efficient: material means, sources of motivation, etc.
The goal is also, for the leader, to show his team that he is open to suggestions and initiatives that may come from the latter. In this way, it will be much more likely to get employees to join the continual improvement process.
Use a Continuous Improvement tool
It also relies on using the right lean tool. For example, a digital work instructions software helps to remove ineffective documentation. All the paper work instructions which are obsolete, difficult to update, no traceable and therefore impact the productivity of the workforce.
Picomto is the European leading software for Digital Work Instructions. Request a demo for more details!
Leave A Comment