Is your industrial company facing performance challenges? Are you seeking concrete solutions to optimize your production? Continuous improvement tools currently represent the most effective answer to sustainably transform your industrial performance. Indeed, 78% of companies using them report a significant increase in their productivity from the first year.
But where to start? How to choose the right tools? And above all, how to implement them effectively on the shop floor?
This comprehensive guide presents the essential continuous improvement tools and their concrete application. You will discover how to digitalize them to maximize their benefits and sustainably transform your industrial performance.
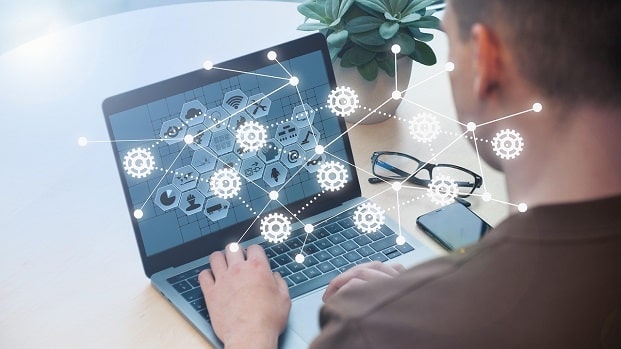
Key takeaways regarding continuous improvement tools:
- Continuous improvement increases productivity by 25% on average
- 73% of industries use at least 3 continuous improvement tools
- Digitalization accelerates results by 40%
- 90% of companies start with 5S and work standards
- The average ROI of continuous improvement projects is 3:1
1. What are the main continuous improvement tools?
At first glance, continuous improvement seems to rely on classic methods. Yet, these tools, developed as early as the 1960s by Toyota, remain essential.
In fact, thanks to digitalization, they adapt perfectly today to modern industry.
1.1. Diagnostic and analysis tools
First of all, diagnosis represents the very first step in a continuous improvement approach.
Indeed, without precise analysis, no effective action can be undertaken. Diagnostic tools therefore allow:
- To quickly identify problems
- To prioritize the actions to be taken
- To guide solutions in a structured way
Thus, a good diagnosis avoids treating only the symptoms.
The 5 Whys
At first glance, the 5 Whys method seems childish. However, it proves formidably effective in finding the true cause of a problem.
In practice:
- One starts by asking the question “Why?” after observing a problem.
- Then, the exercise is repeated five times consecutively.
- With each answer, one digs deeper into the cause.
In this way, the team often discovers causes invisible at first sight. Furthermore, this approach also promotes collective reflection.
The Ishikawa Diagram
Secondly, we must talk about the Ishikawa Diagram, also called the fishbone diagram. This visual tool allows structuring the analysis of causes simply and clearly.
Concretely, it distributes potential causes into five main categories:
- Material: defects related to the materials used
- Method: process or procedure errors
- Manpower: lack of training or skill
- Machine: technical failures or worn machines
- Milieu (Environment): disruptive environmental conditions
In short, this tool helps explore all avenues, even the least obvious ones.
1.2. Standardization and organization tools
At first glance, standardization may seem rigid. Yet, it primarily guarantees the repeatability of best practices.
In fact, a standardized process becomes measurable, reliable, and above all, improvable. Without standards, no sustainable improvement is possible. Let’s examine two essential tools together.
The Digital 5S
First, let’s talk about the famous 5S, now available in a digital version. This method relies on five simple steps to effectively organize the workspace:
- Seiri (Sort): Sort what is useful from what is not
- Seiton (Set in Order): Arrange in a logical manner
- Seiso (Shine): Clean regularly
- Seiketsu (Standardize): Standardize best practices
- Shitsuke (Sustain): Maintain standards daily
Thanks to digital, it becomes possible to:
- Audit work areas more easily
- Track actions in real time
- Involve teams more in the process
Thus, the digital 5S sustainably transforms work habits.
Standard Work
Secondly, we must discuss Standard Work, a true pillar of industrial performance. The principle is simple: describe the best way to perform a task, step by step. The digital version of standard work now allows:
- Integrating explanatory photos and videos
- Offering interactive instructions accessible on tablet or smartphone
- Facilitating the training of newcomers
Furthermore, operators can consult procedures at any time, which reduces errors and enhances efficiency.
1.3. Monitoring and control tools
After implementing standards, it is still necessary to monitor their application. In fact, regular monitoring:
- Guarantees compliance with standards
- Measures progress made
- Quickly detects deviations
Let’s see how digital improves this monitoring.
Digital KPIs
At first glance, digital KPIs offer a decisive advantage: real-time visibility. Concretely, key indicators:
- Instantly measure performance
- Centralize data in dashboards
- Facilitate decision-making thanks to factual data
Thus, managers steer activities with precision and reactivity.
The Connected Gemba Walk
Finally, let’s address the Connected Gemba Walk, a real revolution for shop floor managers. Traditionally, the Gemba Walk consists of going to the field, observing, and talking with operators. With digital, efficiency soars:
- Observations directly entered on a tablet
- Action plans created in real time
- Continuous follow-up of corrective actions
In short, the connected Gemba Walk allows acting fast and sustainably involving the teams.
2. How to effectively use these tools daily?
The effectiveness of tools depends on their proper daily use. Digitalization facilitates their adoption by field teams.
2.1. Which tool to start with?
The choice of the first tool influences the entire approach. The majority of companies start with 5S and work standards.
- 5S creates an optimal work environment
- Work standards reduce variations
- Digital documentation facilitates application
2. How to effectively use these tools daily?
The effectiveness of tools depends on their proper daily use. Digitalization facilitates their adoption by field teams.
2.1. Which tool to start with?
The choice of the first tool influences the entire approach. The majority of companies start with 5S and work standards.
- 5S creates an optimal work environment
- Work standards reduce variations
- Digital documentation facilitates application
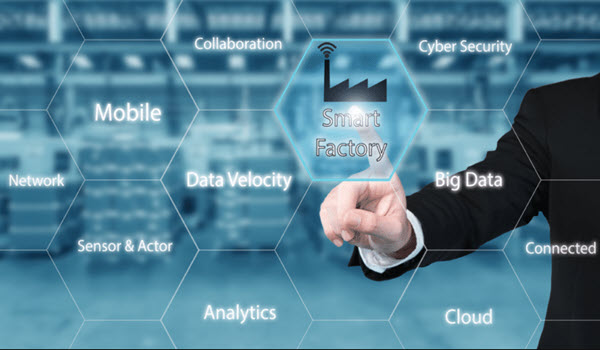
2.2. How to avoid common mistakes?
Certain mistakes compromise the success of the approach. Digitalization helps avoid them. Frequent errors:
- Lack of regular follow-up
- Standards difficult to access
- Insufficient team training
3. What is the difference between Lean and Six Sigma?
The complementarity between Lean and Six Sigma enables achieving operational excellence. Companies combining these approaches increase their productivity by 35% on average.
3.1. The specifics of each approach
Lean focuses on eliminating waste. Six Sigma reduces process variation. These two methods reinforce each other. Lean targets:
- Elimination of the 7 wastes
- Smoothing of flows
- Reduction of inventory
- Optimization of processes
Six Sigma prioritizes:
- Reduction of defects
- Stabilization of processes
- Improvement of quality
- Customer satisfaction
3.2. Which tool for which objective?
The choice of tools depends on your specific objectives. An adapted combination maximizes results. For productivity:
- VSM (Value Stream Mapping)
- SMED (Single-Minute Exchange of Die)
- Visual Management
For quality:
- DMAIC (Define, Measure, Analyze, Improve, Control)
- SPC (Statistical Process Control)
- Poka-Yoke (error-proofing systems)
4. How to digitalize your continuous improvement tools?
Digitalization radically transforms the application of continuous improvement tools. It facilitates their deployment and maximizes their impact.
4.1. Why switch to digital?
Traditional methods show their limits. Digital brings agility and measurable efficiency. Limits of paper tools:
- Time-consuming updates
- Complex distribution
- Tedious follow-up
- Difficult analysis
Advantages of digitalization:
- Instant updates
- Real-time distribution
- Automated follow-up
- Simplified analysis
The average ROI of digitalization reaches 300% from the first year. Productivity gains often exceed 25%.
4.2. How does Picomto transform your traditional tools?
Picomto revolutionizes the application of continuous improvement tools in the field.
Digitalization of standards:
- Intuitive creation of operating procedures
- Interactive work instructions
- Mobile access to best practices
Connected checklists:
- Digital 5S audits
- Quality controls on tablet
- Automated reports
Real-time monitoring:
- Dynamic dashboards
- Instant alerts
- Trend analysis
Conclusion
Continuous improvement tools sustainably transform industrial performance.
Digitalization facilitates their deployment and maximizes their benefits. By enabling structured data digitalization, companies can better monitor, analyze, and enhance continuous improvement initiatives.
Picomto supports you in this transformation. Our digital solution simplifies the daily application of continuous improvement tools.
FAQ
Q: What tools and methods for a continuous improvement approach?
A: 5S, Kaizen, PDCA, Six Sigma, VSM, Kanban, and DMAIC form the essential toolbox.
Q: What are the 7 tools of quality?
A: Ishikawa Diagram, Pareto chart, histogram, check sheet, mapping, control charts, and correlation diagram.
Q: What are the 4 steps of continuous improvement?
A: Plan, Do, Check, Act – the famous PDCA cycle.
Q: What are the 5 S’s of continuous improvement?
A: Seiri (Sort), Seiton (Set in Order), Seiso (Shine), Seiketsu (Standardize), Shitsuke (Sustain).
Q: What are the three types of improvement?
A: Continuous improvement (Kaizen), breakthrough improvement (Kaikaku), and radical innovation (Kakushin).
Q: What is the Lean method?
A: An optimization approach that eliminates waste to maximize the added value of processes.
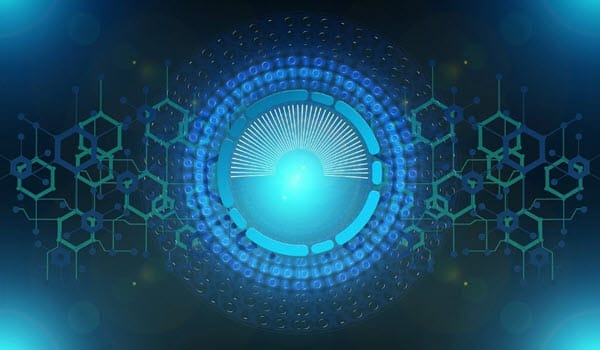
Leave A Comment