Can we ensure production that meets customer expectations while remaining competitive and improving profit levels? This is the multivariate equation that arises in an industry where performance is a guarantee of survival, with competition more intense than ever.
The cost of non-quality is an aspect that we cannot afford to ignore, especially since we can finally consider it as an opportunity, a source of gain. Non-compliance with quality objectives has an impact on the company’s health at several levels, including:
- Performance
- Finance
What is the notion of non-quality?
The term non-quality is used to describe the situation where it has not been possible to develop, at the first attempt, a product with characteristics that meet the customer’s expectations.
It is enough that there is only one anomaly found on the part produced for us to speak of non-quality. It is therefore the difference between the quality objective previously established and the final quality level.
And when it does, it affects the organization more or less severely, hence the need to quickly identify the cause and implement appropriate corrective actions and preventive management.
The cost of non-quality is quite difficult to assess, but this work is essential to enable the company to maintain its overall performance.
The cost of non-quality from a performance point of view
Non-quality penalizes the fluidity of operations, thus the productivity and competitiveness of the company. It does so by having an impact that can be material or immaterial.
The material aspect of the cost of non-quality is represented by the retouching to be carried out when an anomaly is detected, the replacements to be provided or the rejects. These are manipulations that consume time, resources, energy and staff, when all these elements should be busy producing new parts. The decline in productivity and production due to non-quality cannot be taken lightly, however intense it may be.
The intangible impact of non-compliance with quality objectives relates to the customer’s perception of the company and the product it offers. In other words, it is the image of the organization that is damaged when the user is in possession of a part of insufficient quality. And when customer satisfaction is not guaranteed, it is inevitably felt later on in sales.
The financial repercussions of non-quality
The cost of non-quality to the company is also financial. The effects are direct with penalties for delay to be assumed, loss of margins to be charged and exceptional operations to be carried out (recall of products deemed to be below the expected quality, transport of replacement products, etc.). Each of these malfunctions generates additional costs.
In October 2017, AFNOR conducted a survey on the cost of non-quality in industry.
The organization has thus demonstrated that it is possible to evaluate and quantify it, giving eloquent figures. Thus, for two-thirds of the companies reporting that they measure non-quality costs, the losses related to the latter are in the order of 5% of turnover. They are twice as high in 15% of companies, which is far from negligible.
It is therefore reasonable to assume that remedying non-quality theoretically makes it possible to recover 5 to 10% of the turnover. This requires a quality control strategy involving first of all the promotion of good practices in terms of indicators. The question then arises as to what type of industrial performance indicator to focus on, and then to implement a monitoring exercise of the selected quality indicators.
In the survey mentioned above, AFNOR recommends not only limiting itself to quantitative indicators but also relying on qualitative data. It also recommends a managerial approach involving all stakeholders and intensifying communication among staff. In conclusion, there is a growing consensus that the cost of non-quality is a significant factor and that solutions exist.
Use operational solutions
Picomto is a solution for creating, operating and analyzing visual and intelligent work instructions. It will enable operators and technicians to benefit at any time from assistance in carrying out tasks, but will also give it a tool to simplify and facilitate data collection, making it possible to detect quality problems, feed the continuous improvement process and plan corrective action plans
Study case
Discover how Daher digitized its human resources operations by integrating the Picomto solution.
Daher chose Picomto to digitize its operating procedures, thereby eliminating paper from its workshops. Paper operating procedures presented a major risk, which could lead to non-compliance during internal and external audits.
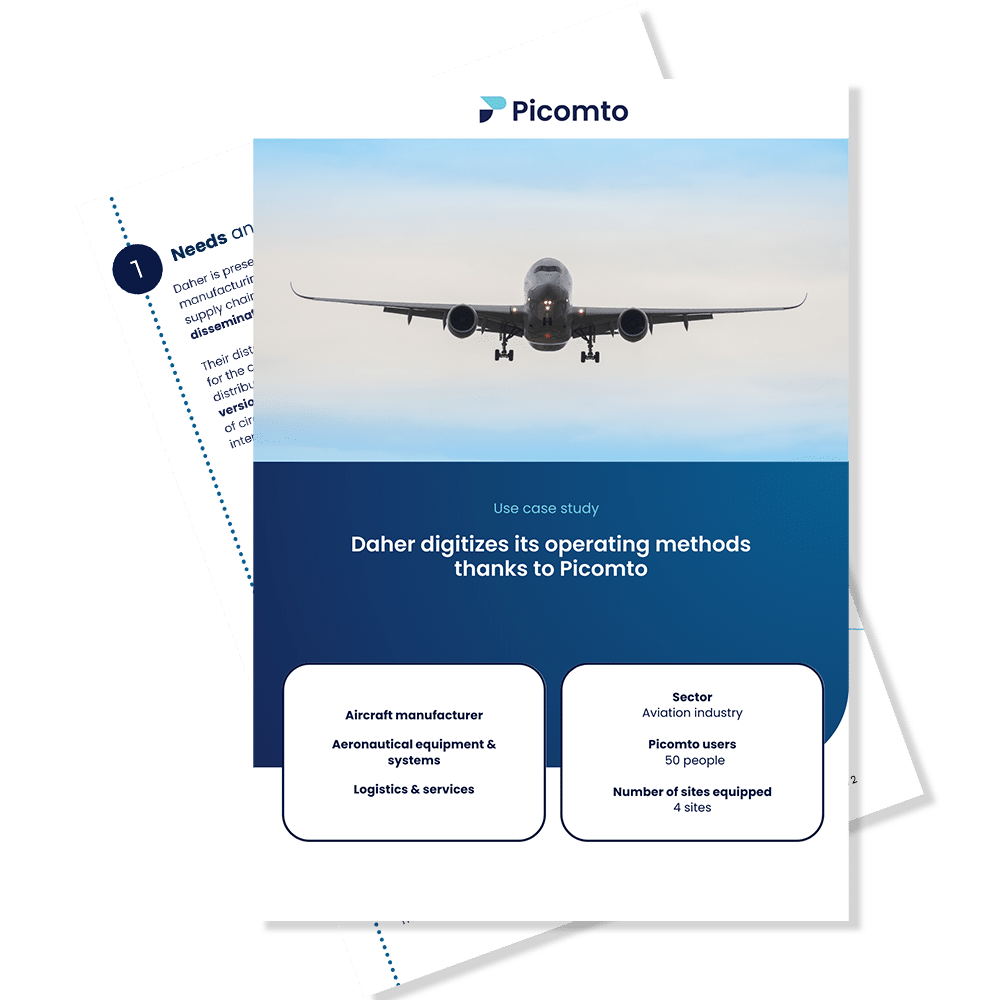
Leave A Comment