Imagine being able to instantly access all your work procedures. Data digitalization makes this possible. Today, 67% of industries are making digital transformation their priority. This is no coincidence. Indeed, digitalization is revolutionizing how work is done on the shop floor. It simplifies operators’ daily tasks.
At the core of this evolution, industrial data automation enables real-time access to reliable information, streamlining production and supporting smarter decision-making.
But how do you approach it concretely? What benefits can you expect? Where should you start? In this comprehensive guide, we answer all your questions about industrial data digitalization.
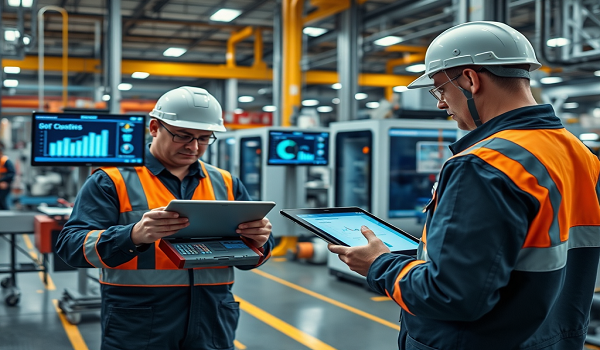
Key points about data digitalization:
- Digitalization improves industrial productivity by 25%
- 73% of factories have already begun their digital transformation
- Digital work instructions reduce errors by 45%
- Return on investment is visible in less than 12 months
- 90% of operators easily adopt digital tools
1. What is Data Digitalization in Industry?
At first glance, digitalization may seem like a simple transition from paper to digital. However, in reality, it profoundly transforms information management.
First and foremost, digitalizing a document means making it intelligent, interactive, and most importantly, accessible in real-time. Gone are the dusty binders. Every factory stakeholder instantly accesses the data relevant to them. Moreover, a recent study reveals a striking figure: 75% of industrial sites have already initiated their digital transformation.
The benefits are clear: fewer errors, improved responsiveness, and better traceability. Let’s take a concrete example. A production operator can consult work instructions directly on a tablet. They gain autonomy and efficiency. And most importantly, the data is always up to date.
1.1. Beyond Simple Document Digitization
At this point, it’s important to note that digitalization goes far beyond simply scanning a document. In fact, content becomes dynamic.
Procedures are no longer static. They transform into interactive, clear, and intuitive guides. Each operator follows steps in real-time, on screen. Furthermore, these instructions adapt to each product, machine, and context.
They evolve according to needs. Take Daher’s case. At their sites, technicians use tablets to consult instructions.
Result: better execution, fewer errors, and more rigorous monitoring.
1.2. What Documents Can Be Digitalized in the Workshop?
In truth, almost all paper documents can be digitalized. Here are some examples of easily transformable documents:
- Operating procedures: to guide workstation tasks
- Maintenance procedures: to make interventions more reliable
- Quality checklists: to ensure standards
- Training materials: to transfer know-how
- Production reports: to track key indicators First and foremost, work instructions are often the priority. Why? Because they directly impact productivity and safety. Their digitalization yields immediate and measurable results.
2. Transformation through Industry 4.0
First, it must be said that Industry 4.0 is disrupting traditional production models. It imposes new standards. And at the heart of this evolution lies an essential driver: digitalization.
Thanks to digital technologies, factories become more agile, smarter, and above all, more performant.
2.1. New Production Standards
First and foremost, the numbers speak for themselves. Large companies are no longer just experimenting. They’re moving forward rapidly. Here are some key field data:
- 80% of large groups already have a digitalization plan
- 65% use digital instructions
- 45% have completely eliminated paper in their workshops These figures clearly show one thing: digitalization is no longer an option but an industrial standard.
2.2. Impact on Professions
Secondly, it should be emphasized that this transformation affects all factory functions. Every profession evolves. And for many, the benefits are immediate. Here’s how roles are changing in the field:
- Operators gain autonomy and responsiveness
- Supervisors monitor production in real-time
- Trainers incorporate interactive and up-to-date content
- Maintenance becomes predictive thanks to data In sum, everyone becomes an actor in collective performance. Digitalization strengthens skills and gives new meaning to daily work.
3. Concrete Benefits of Digitalization
First, it must be said that industrial digitalization produces measurable results. It’s not just a trend; it’s a real performance lever. Indeed, according to a study, factories that have adopted digital are 26% more productive.
Operators save precious time, tasks are better mastered, and data becomes reliable. Moreover, the transition to digital significantly reduces paper usage. For example, a medium-sized factory saves up to 3 tons of paper per year. A strong gesture for the environment.
3.1. Improved Daily Productivity
First and foremost, digital tools facilitate everyday tasks. Operators are better guided. Training is faster. Maintenance interventions are smoother. Here are the concrete gains observed in the field:
- 25% time saved in production
- 40% faster team training
- 30% additional efficiency in maintenance In sum, each team gains autonomy and efficiency.
3.2. Enhanced Quality at Every Step
Next, it should be emphasized that digitalization significantly improves quality. Errors are reduced. Processes become safer. Every action is recorded and traceable. Here are the concrete impacts on quality:
- 45% fewer errors in production
- 60% of non-conformities avoided
- 100% traceability of sensitive operations In fact, quality is no longer a difficult-to-achieve goal: it becomes a standard integrated into each step.
Discover the results obtained by SKF through the digitalization of instructions and quality controls!
4. How to Succeed in Your Digitalization?
At first glance, digitalizing may seem simple. In reality, success relies on a structured and progressive approach.
First, you need to define a clear direction, involve teams, and choose the right tools. Without these pillars, the transformation risks remaining incomplete.
4.1. Start with a Diagnosis
First and foremost, take time to evaluate your current situation. This step is crucial for building a solid project. Here are the actions to take from the start:
- Identify priority processes
- Measure time lost with paper documents
- Gather field feedback
- Set clear and achievable objectives
4.2. Choose the Right Tools
Secondly, opt for solutions that naturally integrate with your operations. The tool should simplify, not complicate. A good tool is one that is:
- Easy to handle for operators
- Accessible on tablet, mobile, and PC
- Scalable to accommodate your future needs
- Compatible with your existing systems
4.3. Support Change
It must be said that project success doesn’t depend solely on technology. In fact, the human factor makes all the difference. Supporting change means:
- Including users from the start
- Valuing their feedback and ideas
- Creating ongoing dialogue between field and management
4.4. Train Your Teams
Training is an essential lever. It promotes adoption and builds confidence. For this:
- Offer short, targeted training sessions
- Identify internal ambassadors
- Celebrate first successes
- Support each team step by step
4.6. Measure Results
Finally, track your progress. Clear indicators allow for continuous project adjustment and improvement. Among the key indicators:
- Time saved in production
- Reduction in errors and non-conformities
- Team satisfaction
- Visible return on investment
Conclusion
Data digitalization has become essential in modern industry. It positively transforms teams’ daily operations.
As a key component of Industrial Process Digitalization, it enables seamless workflows and better resource utilization across the production chain.
It also serves as a foundation for the Smart Industry, where connected systems, real-time data, and intelligent automation drive continuous improvement and innovation.
The benefits are concrete and measurable:
- Improved productivity
- Enhanced quality
- More autonomous teams
- Reduced environmental impact
Ready to transform your industry? Our experts are here to support you in your digitalization project.
FAQ
Q: What is data digitalization?
A: Digitalization transforms information into intelligent and interactive digital resources, beyond simple dematerialization.
Q: What’s the difference between digital and digitalization?
A: Digital converts documents to electronic format. Digitalization transforms processes and creates new value.
Q: What are the pillars of digitalization?
A: Digitalization relies on three pillars: technological tools, business processes, and human support.
Q: How to define digital?
A: Digital refers to all technologies enabling the creation, management, and sharing of data in a connected manner.
Q: What are the challenges of digitalization?
A: The main challenges are change management, data security, and integration with existing systems.
Q: Why does digitalization impact time and space?
A: Digitalization enables instant access to information anywhere, eliminating traditional time and distance constraints.
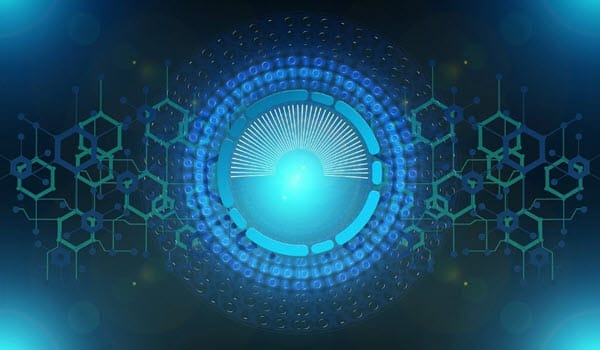
Leave A Comment