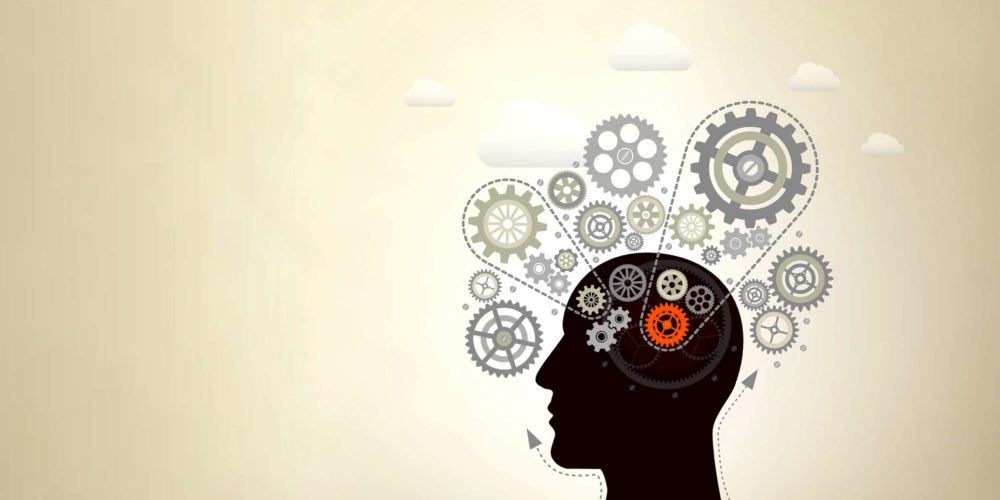
In a previous article, we talked about training for operators and how to improve it. Quite naturally, in the process of monitoring the skills of operators and technicians, it is necessary to evaluate the learning of employees, this article is therefore in continuity with this theme.
Continuous improvement in the industry means ensuring that teams are constantly able to strengthen their skills and acquire new ones so that the company can perform ever better. This includes, among other things, training sessions, which occur when new procedures, tools or innovative machines are to be integrated.
It will then be necessary to support operators and see how they behave in relation to these new features if they apply them in accordance with expectations. For this purpose, Professor Donald Kirkpatrick (1924 – 2014) had created a model dealing with employee appraisal. The latter consists of 4 levels: evaluation of reactions, learning, knowledge transfer and results.
These are the last two that interest us here, because they are the ones that fall under the so-called delayed evaluation. In other words, it is the evaluation of operators carried out several months after the training.
Delayed evaluation, which is also referred to as factual and deferred, has several interests, including the following:
- Ensure proper execution of work instructions
- Report on changes in employee practice
- Evaluate the impact of learning and training on the collective performance of the company
Enable the worker to do his job properly
This is the first and most obvious objective of the operator’s delayed evaluation process. It is a matter of ensuring that the employee is able to perform the tasks associated with his or her position without error or defect after having been trained.
The deferred assessment of the employee’s skills emanates from indicators on the proper application of work instructions (paper-based procedures are still very present in most industries and have consequences for everyday life) and possibly the elementary rules inherent in his environment (safety instructions, etc.). Based on the information collected and analyzed, managers will be able to make the most appropriate decisions to ensure that the company maintains and consolidates its performance.
The delaued evaluation process is therefore one of the main vectors for continuous improvement in the industry.
Assess the degree of change in the operator’s practice
Assessing the skills of delayed employees makes it possible to see to what extent they were able to change the way they operated after the training.
When you put in place a training plan for your staff, you do expect your employees to change their practice in their respective positions. In practice, this means checking whether, for example, changes made in one of the process steps have been implemented.
Whatever the method of skills monitoring chosen and applied, the effectiveness of the changes and their integration into the organisation’s operating mode can be accurately measured when the evaluation takes place 3 or 6 months (these are only indicative deadlines) after the training action.
The only way to know the impact on overall performance
Finally, delayed evaluation is the only way to measure the impact on the company’s performance, in other words, at the collective level.
Technically, it is difficult, if not impossible, to have a complete and accurate overview of the assimilation of new knowledge at the global level downstream of training. Of course, estimates can be made or based on past experience, but only a factual evaluation can make it possible to assess the effects of the continuous improvement strategy via training on the organisation as a whole.
Adopt visual work instructions to facilitate operator skill development
Picomto provides solutions to facilitate and simplify the development of operator skills through visual and digital work instructions. Our experts are available to answer your questions.
Leave A Comment