Are you still filling out paper checklists in your factory? The digitalization of checklists represents a decisive turning point for industry today. But why are so many companies still hesitating to take the leap? How can you ensure that this digital transformation will truly benefit your organization?
In a world where every second counts, modernizing your processes becomes vital. The paper era is coming to an end. The digitalization of checklists has become an essential solution for industries aiming for operational excellence.
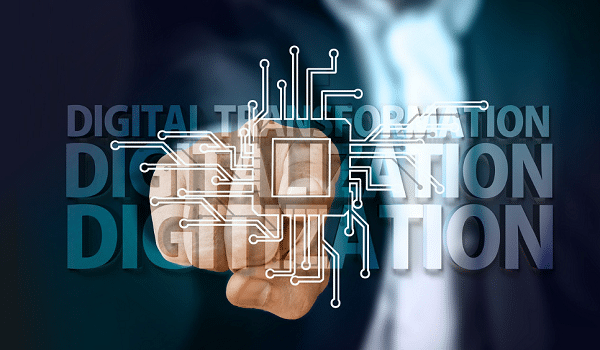
Key points to remember about checklist digitalization:
- Checklist digitalization reduces operational errors by 75%
- Average productivity gain of 30% after implementation
- Real-time data access on all devices
- Enhanced compliance and traceability
- Positive ROI observed in less than 6 months
1. Why abandon your paper checklists in favor of digital?
Digital transformation is disrupting all industrial sectors. Yet many companies continue to use paper checklists in their internal processes. But at what cost? Companies that cling to traditional methods lose competitiveness, efficiency, and responsiveness every day.
It’s time to take stock of the limitations of paper checklists and discover how digitalization can transform your way of working.
1.1. The limitations of paper checklists that hinder your productivity
At first glance, paper seems simple and economical. However, this simplicity is deceptive: it hides hidden costs and considerable time waste.
Time loss and lack of efficiency
A recent study reveals that 23% of operators’ time is lost due to handling paper documents. This wasted time translates into:
- Searching for misplaced documents
- Manual data entry
- Transcription errors
Less time devoted to essentials = Less productivity.
Costly and risky physical storage
An average company accumulates more than 10,000 pages of documentation per year. This represents:
- Storage cost: Archiving, maintenance, and securing documents
- Risk of loss: A fire, flood, or human error can lead to the loss of critical information
- Search difficulty: Finding a specific document in a mountain of paper is time-consuming
Physical storage is not only costly: it slows responsiveness and increases the risk of error.
Rapid obsolescence of information
Paper checklists quickly become obsolete:
- Updates are manual, therefore slow
- It’s difficult to ensure that all versions are properly distributed
- Errors due to using outdated versions are frequent
An obsolete paper version can lead to a costly error in the production process.
1.2. Digitalization: a powerful solution to improve your productivity
Going digital is much more than a simple format change: it’s a revolution in process management. Digitalization makes your checklists:
Accessible in real-time
- Operators instantly access necessary information from a tablet, smartphone, or computer
- Updates happen in real-time, without delay
- No more errors due to using obsolete versions!
An immediate time saving and enhanced responsiveness.
Process automation
- Digital checklists integrate directly with ERP or MES systems
- Data is automatically recorded, analyzed, and shared
- Automatic alerts notify operators in case of anomalies
Fewer human errors and more traceability.
Reduction of operational costs
- No more need to print, store, or distribute paper documents
- Information search becomes instantaneous
- Errors are detected more quickly, thus limiting financial losses
A rapid return on investment and better cost control.
Real-world case: Veolia, an inspiring success story
Let’s take the example of Veolia, which digitalized its maintenance processes. In six months, they observed a 40% reduction in operational errors. Traceability also improved considerably.
2. Concrete benefits of checklist digitalization
Adopting digital checklists is much more than a simple modernization of processes. It’s a profound transformation that improves the overall performance of the company.
The figures prove it: digitalization optimizes time, strengthens process quality, and simplifies operations management.
2.1. Measuring operational efficiency gains
The results are clear: companies that have taken the step toward digitalization see immediate productivity gains.
A 75% reduction in information search time
- Operators directly access information via a tablet or smartphone
- No more time wasted searching for paper documents or checking for updates
- Files are classified, indexed, and accessible in seconds
Result: More responsiveness, fewer errors.
A 30% improvement in team productivity
- Tasks are automated, reducing time spent on repetitive tasks
- Updates and validations occur in real-time, without loss of information
- Operators save time and focus on their core business
Result: Better overall efficiency.
A 65% decrease in non-conformities
- Digital checklists include automatic alerts in case of anomalies
- Controls are reinforced thanks to complete traceability
- Operators are guided step by step, reducing the risk of human error
Result: Enhanced quality and lower costs related to errors.
2.2. Strengthening compliance and traceability
Digitalizing checklists simplifies compliance management and improves process traceability.
Automatic timestamping of each action
- Each action is recorded in real-time, with a precise date and time
- Modifications and interventions are automatically tracked
- Operators can easily verify the history of actions
Result: More transparency and fewer errors.
Automatic report generation
- Compliance reports are generated in a few clicks
- Data is centralized and automatically structured
- Auditors have all necessary information in real-time
Result: Considerable administrative time saved.
2.3. Improving communication between teams
Communication is an essential pillar of a company’s performance. Checklist digitalization allows for smoother information sharing and strengthens collaboration between teams.
Instant information sharing
- Information is shared in real-time between field teams and headquarters
- Operators receive immediate updates on their terminal
- Interventions are better coordinated thanks to a global view of operations
Result: Less confusion and faster decision-making.
Automatic notifications
- Operators are instantly alerted in case of an anomaly or procedure change
- Managers can validate or correct an intervention remotely
- The communication loop is shortened, avoiding misunderstandings
Result: Increased responsiveness and better incident management.
3. How to select the ideal solution?
Choosing a checklist digitalization solution is a strategic step that requires thorough analysis. An unsuitable solution can lead to additional costs, wasted time, and team resistance.
To make the right choice, it’s essential to rely on clear and relevant criteria.
3.1. Essential criteria for your choice
Before diving in, carefully evaluate each solution based on the specific needs of your company. Here are four key criteria not to neglect:
Interface ergonomics
An intuitive interface allows for quick adoption and reduces the training time needed for your teams. Operators must be able to navigate easily in the application, even without technical expertise. Good ergonomics improves execution speed and limits errors.
Compatibility with your existing systems
The solution must integrate easily with your current infrastructure (ERP, MES, CMMS).
A smooth connection with your systems allows for real-time data synchronization, thus avoiding duplications or processing errors. Also check compatibility with your equipment (tablets, PCs, industrial terminals).
Industry-specific functionalities
Each industrial sector has unique needs. The solution must offer customization options adapted to your work environment: management of quality control procedures, automation of compliance reports, or automatic alerts in case of non-compliance. A tailored solution guarantees better operational efficiency.
Data security
Checklists often contain sensitive information (procedures, reports, audit data). The solution must guarantee data encryption, secure access management, and automatic backup. Effective protection reduces the risk of data leakage or loss.
3.2. Why Picomto stands out in the industry?
Not all solutions are equal. What makes the difference is the platform’s adaptability and rapid return on investment.
A solution designed for industrial environments
Picomto is designed to function in demanding environments (heavy industry, continuous production). The interface is adapted for field use with quick adoption, even in difficult conditions. Operators can report an anomaly or non-compliance in real-time, which improves responsiveness.
A solution that evolves with your organization
The platform is modular and customizable. New functionalities are deployed automatically without service interruption. Integration with your existing management tools (SAP, Oracle, Salesforce) is simple and quick.
A positive ROI in less than 6 months
Picomto clients observe a reduction in errors and an increase in productivity from the first months. Gains are measurable thanks to clear KPIs: reduced processing time, decreased errors, and reduced training costs.
Conclusion
The digitalization of checklists is no longer an option but a necessity. Companies that take the leap today gain a decisive advantage.
As part of a broader Industrial Process Digitalization strategy, digital checklists ensure consistency, traceability, and real-time responsiveness on the shop floor.
In an increasingly competitive industrial world, operational excellence comes through digital.
Don’t let your company fall behind.
Join the leaders in your industry who have already chosen digital transformation.
FAQ
Q: How do you digitalize a checklist?
A: Identify your key processes, choose an adapted tool like Picomto, import your data, and train your teams progressively.
Q: What are the types of digitalization?
A: There are three types: document digitization, process automation, and complete digital transformation.
Q: What is the digitalization of internal processes?
A: It’s the transformation of manual procedures into digital workflows to improve efficiency and traceability.
Q: What are the steps of digitalization?
A: Initial audit, tool selection, team training, progressive deployment, and results measurement.
Q: What are the three pillars of digitalization?
A: Digital technologies, process transformation, and change management for teams.
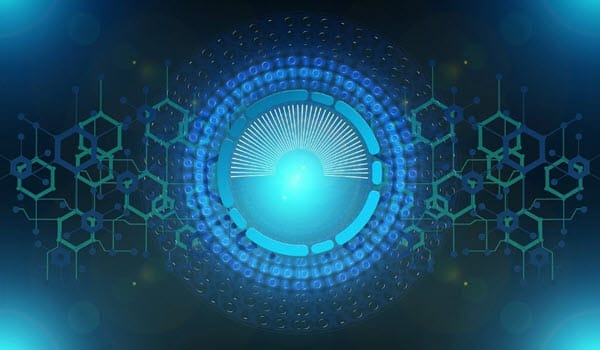
Leave A Comment