How can your food processing company guarantee optimal production while adhering to strict quality and safety standards? Production performance indicators in food processing constitute the answer to this crucial question. In a sector where margins of error are minimal and traceability is mandatory, these KPIs enable you to measure, analyze, and continuously improve your processes. Indeed, these indicators help you make informed decisions based on concrete data. Consequently, they become indispensable for maintaining your competitiveness and ensuring regulatory compliance.
Moreover, the food processing industry faces unprecedented challenges: reinforced quality requirements, cost pressure, and the necessity for complete traceability. Thus, performance indicators enable you to transform these constraints into improvement opportunities. Finally, this guide will accompany you in identifying, implementing, and optimizing your KPIs through modern digital solutions.
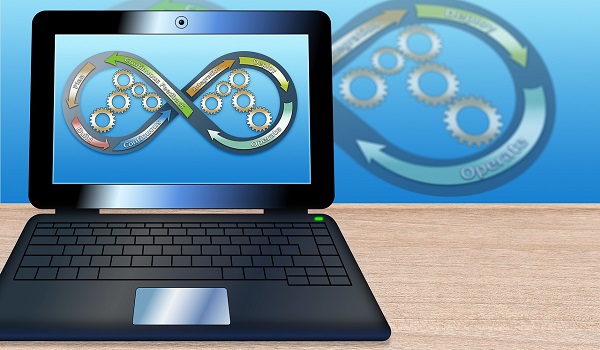
Key points to remember regarding performance indicators in food processing production :
- Efficiency measurement: OEE, yield, and productivity to optimize resources
- Quality and safety: Defect rates, non-conformities, and complete traceability
- Equipment performance: Preventive maintenance and machine availability
- Digitalization: Automated data collection and real-time analysis
- Continuous improvement: Implementation methodology and team training
Discover how our solution can transform your performance monitoring for a personalized consultation.
1. What are the essential performance indicators in food processing production?
Identifying the right performance indicators constitutes the foundation of efficient food processing production. Nevertheless, each company must adapt its KPIs according to its business sector and specific objectives. However, certain indicators remain universal for measuring the overall performance of your production.
1.1. How to measure production efficiency?
The Overall Equipment Effectiveness (OEE) represents the most comprehensive performance indicator. It combines three essential dimensions:
- Availability: Actual operating time / Planned time
- Performance: Actual rate / Theoretical rate
- Quality: Conforming products / Total production
Furthermore, material yield measures the efficiency of raw material utilization. Similarly, hourly productivity indicates the number of units produced per hour of work.
Optimize your OEE with our digital instructions. Consult our Agromousquetaires case study to discover the results obtained.
1.2. Which KPIs for quality and food safety?
Quality constitutes a critical issue in food processing. The following indicators enable rigorous monitoring:
- Defect rate: Percentage of non-conforming products
- Customer return rate: Quality complaints / Products sold
- HACCP compliance: Adherence to critical control points
- Traceability: Product information retrieval time
Additionally, food safety indicators include the number of sanitary incidents and compliance with storage temperatures.
1.3. How to monitor equipment performance?
Preventive maintenance optimizes equipment availability. Essential KPIs include:
- MTBF (Mean Time Between Failures): Equipment reliability
- MTTR (Mean Time To Repair): Maintenance efficiency
- Maintenance cost: Expenses / Revenue
- Operational availability: Operating time / Total time
2. How to digitalize performance indicator monitoring?
Digitalization radically transforms performance indicator monitoring in food processing production.
Indeed, it enables automated collection, real-time analysis, and better reactivity to deviations. Thus, companies can transition from manual and sometimes approximate monitoring to a precise and reliable system.
2.1. Why switch to digital work instructions?
Digital work instructions revolutionize data collection. They offer several advantages:
- Standardization: Uniform procedures across all workstations
- Automatic collection: Data entered directly into the system
- Complete traceability: Timestamp and operator identification
- Instant updates: Modifications distributed immediately
Consequently, data entry errors decrease considerably. Moreover, operators benefit from clear and updated instructions.
2.2. How to centralize data collection and analysis?
Data centralization enables a global view of performance. Modern systems integrate:
- Real-time dashboards: Instant KPI visualization
- Automatic alerts: Notifications in case of deviation
- Predictive analysis: Anticipation of potential problems
- Automated reporting: Generation of periodic reports
Nevertheless, integration with existing systems (ERP, MES) remains essential to avoid data silos.
2.3. Which tools for real-time monitoring?
Real-time monitoring tools include:
- IoT sensors: Automatic parameter surveillance
- Production screens: Real-time KPI display
- Mobile applications: Mobile data entry and consultation
- Connected glasses: Instructions and data directly in the field of vision
3. How to effectively implement your KPIs with a digital solution?
Successful implementation of performance indicators requires a methodical and structured approach. However, many companies fail due to lack of planning or training. Thus, a proven methodology guarantees the success of your digitalization project.
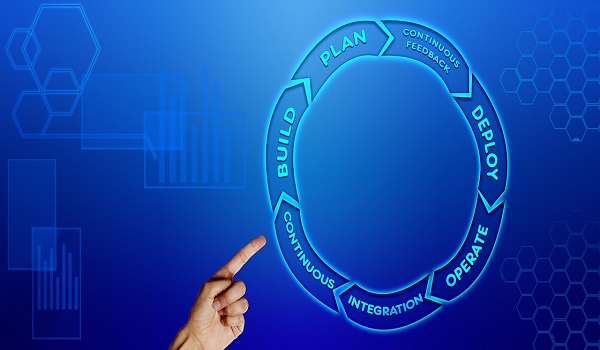
3.1. Which methodology to deploy your indicators?
Deployment follows a progressive approach:
Phase 1: Diagnosis and audit
- Analysis of existing processes
- Identification of priority KPIs
- Evaluation of current systems
Phase 2: Design and configuration
- Definition of alert thresholds
- Dashboard configuration
- Testing and validation
Phase 3: Pilot deployment
- Launch on a restricted scope
- Adjustments and optimizations
- User training
Phase 4: Generalization
- Progressive deployment across all sites
- Monitoring and support
- Continuous improvement
3.2. How to train and support your teams?
Training constitutes a key success factor. It must cover:
- Technical training: Use of digital tools
- Methodological training: KPI interpretation
- Behavioral training: Adoption of new practices
- Continuous support: Post-deployment assistance
Moreover, change management involves clear communication about benefits and objectives.
3.3. How to ensure adoption of new tools?
Successful adoption relies on several factors:
- Management involvement: Visible support from leadership
- Tangible benefits: Demonstration of added value
- Ease of use: Intuitive and ergonomic interfaces
- User feedback: Consideration of field input
4. How Picomto revolutionizes food processing performance monitoring
Picomto transforms performance indicator monitoring through its integrated platform. Indeed, our solution covers the entire KPI lifecycle, from procedure creation to results analysis. Thus, food processing companies benefit from a complete and coherent ecosystem.
4.1. Creation and standardization of digital procedures
The Picomto platform enables easy creation of standardized digital procedures:
- Visual editor: Intuitive creation with photos and videos
- Centralized library: Procedure storage and sharing
- Automatic versioning: Modification and update management
- Instant distribution: Deployment across all workstations
Consequently, operators always access the latest procedure versions. Moreover, consistency between sites is guaranteed.
Create your digital procedures in just a few clicks.
Discover our Marine Nationale case study to see standardization in action.
4.2. Field data collection and analysis
Data collection is performed directly from workstations:
- Guided input: Forms adapted to procedures
- Quality controls: Automatic data validation
- Geolocation: Intervention traceability
- Timestamps: Precise execution time tracking
Subsequently, data analysis produces actionable insights for continuous improvement.
4.3. Remote expert support and process validation
Picomto offers integrated expert support:
- Real-time assistance: Video support and chat
- Remote validation: Quality control by experts
- Knowledge capitalization: Know-how preservation
- Continuous training: Team skill development
Conclusion
Performance indicators in food processing production constitute the foundation of effective continuous improvement. Indeed, their strategic implementation enables optimization of quality, productivity, and food safety. However, digitalization proves indispensable to fully exploit their potential.
Digital transformation offers unparalleled precision and reactivity. Consequently, companies that adopt these solutions gain an advantage over their competitors. Finally, investment in modern tools like Picomto generates rapid and sustainable return on investment.
Ready to revolutionize your performance monitoring?
Contact our experts to transform your production.
FAQ
What are the performance indicators in production?
OEE, material yield, hourly productivity, defect rate, equipment availability.
What are the 5 types of indicators?
Efficiency, quality, safety, cost, food production timeline.
What are the 5 KPIs used to monitor performance?
OEE, defect rate, MTBF, productivity, HACCP compliance.
How to formulate a performance indicator?
Define objective, measurement unit, collection frequency, alert thresholds.
What are the productivity indicators?
Units/hour, material yield, unit cost, overall efficiency.
What are the 4 types of performance?
Operational, financial, quality, safety in food processing production.
What are the performance measurement tools?
IoT sensors, dashboards, mobile applications, MES systems.
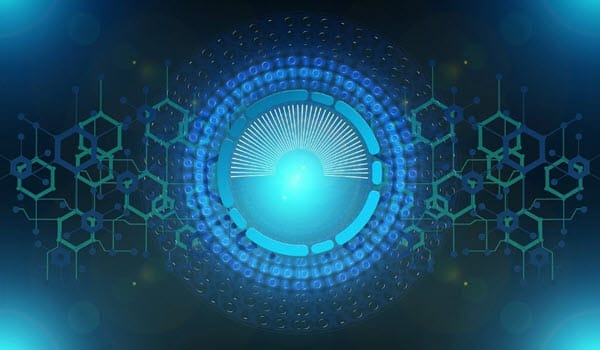
Leave A Comment