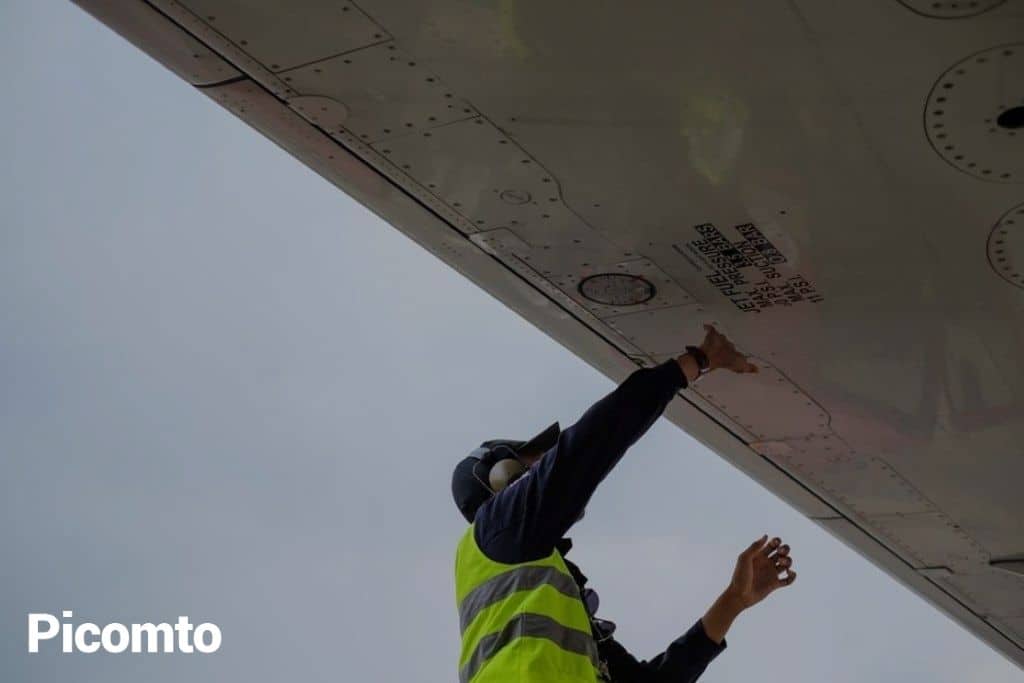
The digitisation of processes is a logic that is already well underway in the industry. The factories are equipped with digital tools that not only make it possible to get rid of paper supports that are as cumbersome as they are impractical and complicated to update, but also to increase the automation of operations and the circulation of information.
By dematerializing processes for technicians, the companies concerned benefit from at least two levels:
- Cost reduction
- The improvement of manufacturing performance in all its steps
Dematerialize manufacturing steps to reduce costs
The implementation of digital tools in field processes represents a significant initial investment, but this approach allows companies to reduce their costs significantly. This optimization of production-related expenses is observed at different levels, but one of the most notable aspects is that of maintenance.
We know, in fact, that the operations carried out by technicians to ensure the proper functioning of the machines and to restore them in the event of immobilisation (breakdown, malfunctioning…) is essential, but very costly. They weigh on the company’s financial resources, on the one hand, because the means of production must be immobilized during its maintenance and therefore does not produce, and on the other hand because they incur direct costs: labour costs incurred (maintenance technicians, experts…), spare parts, etc.
However, the solutions provided by digital innovations make it possible to optimize maintenance interventions both in their organization (planning of operations, preventive and predictive actions using sensors and reference values) and in their execution. Faced with maintenance or machines repair, technicians are better prepared and perfectly guided by following detailed instructions on the tablet, via mobile applications specifically developed or even directly in their field of vision thanks to augmented reality devices.
At the same time, tools such as Picomto make it easier for operators to make documents available during their maintenance mission.
A more fluid process thanks to digital tools
The digitisation of processes also has the advantage of making them fluid, since the sources of slowness, malfunctions, errors and non-conformities are more easily and quickly detected. Once identified, it becomes easier to remedy them, then to ensure the effectiveness of the readjustments and corrections made by carrying out tests and simulations, also made possible by advanced digital tools.
The improvements made possible by the dematerialization of processes also concern the management and use of stocks. Accurately identifying the number of products or raw materials in real-time, integrating them into the manufacturing stages in a reduced time and with a minimum of intervention, this also contributes to improving process efficiency and thus making the company more efficient.
Not to mention that thanks to the fact that compliance problems are better identified and solved, as explained above, quality improvement is considerably supported. In the end, this ensures much higher levels of customer satisfaction and thus makes it possible to become much more competitive.
Picomto is the web and mobile solution for creating, operating and analyzing work instructions, maintenance procedures in an intelligent, connected and dynamic way. Feel free to contact us for more information.
Leave A Comment