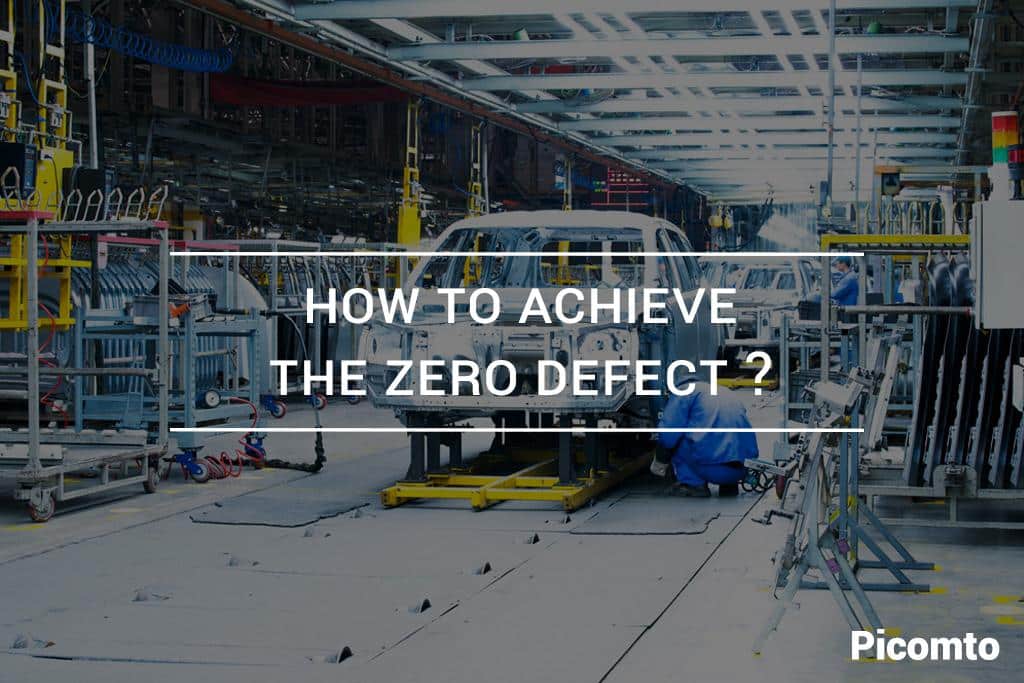
Is achieving zero-defect a realistic goal? This is the question that all industry specialists have been asking themselves for decades. Since there is no such thing as a perfect system and since every organization understands the human factor (which is not infallible by definition), it is safe to assume that it is more pragmatic to seek to achieve the absence of failure than to hope to have a production that is totally free of failure.
Why is quality so important?
Errors and dysfunctions in processes are the fear of industrialists and managers because they prevent them from reaching zero defects. Everything is, therefore, being done to try to maximize production quality levels. Without this, no company can hope to keep pace with its competitors in a context of intense global competition. Excellence is not an option; it is a vital necessity today. Defects penalize the company in many ways.
They have negative repercussions on production costs, generate monster waste in terms of resources, time and energy, produce waste and significantly damage the brand’s image.
To prevent these phenomena and get as close as possible to zero defects, organizations adopt a quality approach based on audits and continuous improvement.
Zero defects: make it good the first time
There is a unit to measure non-quality in production: ppm. This is the number of defects recorded per million parts produced per year. Also known as DPMO (defects by millions of opportunities), it is used in the automotive and aerospace industries. It is one of the benchmark indicators for quality.
The objective is, therefore, to reduce this ppm or DPMO to its simplest expression, which is fully in line with the search for zero defect. In other words, the ideal model is the one that makes it possible to look good the first time around in order to limit returns, rejects and alterations. In reality, the levels of tolerance for failure rates vary widely depending on the manufacturers and the specificities of their activities. Thresholds from 5 to 10 ppm can be found as well as others at 50 ppm.
Addressing these defects through greater control of manufacturing processes ensures optimal use of resources while improving customer satisfaction.
Digitisation to reduce defects to their simplest expression
The digitalization of production and monitoring tools is one of the major advances proposed today to reduce failures and increase quality. Digital solutions for industry offer, among other things, the possibility of detecting the defect earlier, identifying its origin and reacting more quickly. Trying to achieve zero defects also means being responsive and having the appropriate tools to make the necessary readjustments in the manufacturing cycle.
Digitization also pushes in the direction of zero defects by intervening in other aspects such as training, dematerialization of work instructions and the development of maintenance means and procedures.
Picomto is the leading European software of digital work instructions. Do not hesitate to contact us for more information.
Leave A Comment