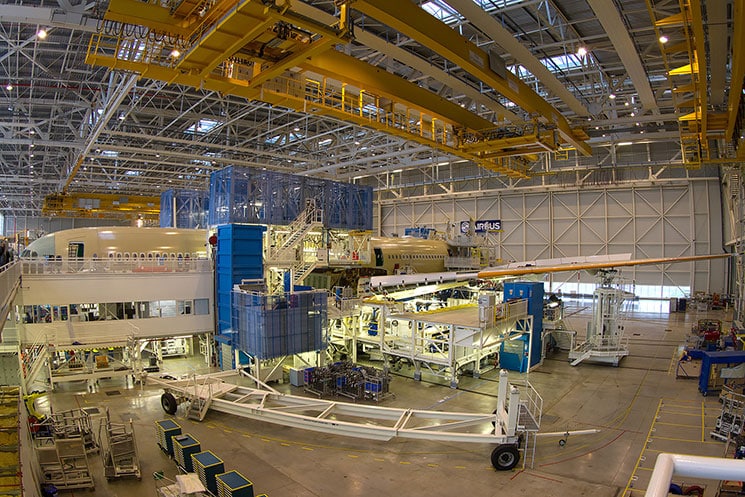
Documentation is one of the pillars of the industry. The media on which important information is recorded, whether material or in digital format, are repositories for the company’s stakeholders that guide them in the accomplishment of their missions. One of the major challenges today is to ensure the relevant and effective use of the various documents directly related to the field (anomaly sheet, progress sheet, etc.), in order to improve production.
Documents at the heart of the quality approach
The keeping of anomaly sheets, progress sheets and other documents of this kind is resolutely in line with the implementation of a quality approach. The constant improvement of products and therefore of production processes requires first of all the identification of malfunctions and the provision of an efficient and sustainable solution.
As a formalized document, the anomaly sheet now takes the form of a digital form (paper supports, less practical and more voluminous, tend to be abandoned in favor of digital formats) that can be completed as part of an internal audit. All the elements allowing the anomaly observed in the production line to be clearly identified (employee who noted the anomaly, degree of seriousness, date of occurrence of the anomaly, etc.), but also the response to this malfunction are recorded. The purpose of this process is, in fact, to correct the anomaly and prevent new occurrences.
Encourage improvement and initiative
The field documents also serve to encourage initiatives and suggestions among operators, always with a view to increase efficiency and productivity. This is indeed what the progress sheet, or improvement sheet promotes. The employee who knows his workstation perfectly is ideally placed to formulate ideas that can optimize the work process.
By presenting the situation as it appears on the ground (nature, person concerned, place, date, how the event occurred and for what reason), the progress sheet then gives the opportunity to propose ways of improvement.
It refers to key quality principles, such as prevention and responsibility, while creating a climate conducive to employee involvement and active participation.
Establish a real process for identifying and resolving problems
An organization for improving efficiency and productivity must be set up taking into account the specificities of the company and its production lines, including an approach designed to identify and solve problems.
The 8D approach responds to this requirement by systematizing problem-solving, involving as many actors as possible (working in transversal teams) and perpetuating the resolution of specific problems.
To this end, it provides for 8 actions:
- Preparation of the process: setting up the team to solve the problem, defining objectives and responsibilities
- Description of the problem: issues, constraints, consequences
- Immediate actions to be undertaken: the aim here is to provide an urgent solution until a definitive response is developed and to address the root causes of the problem
- Identification of the real causes: determine the potential and assignable causes, define corrective actions to eliminate them
- Validation of corrective actions
- Implementation of corrective actions
- Prevention of recurrences
- Assessment: once it has been established, highlight the achievements and improvements made possible by the approach and congratulate the team
Picomto is the European leading platform to build, view and analyze quality documentation. Contact us to know more.
Leave A Comment