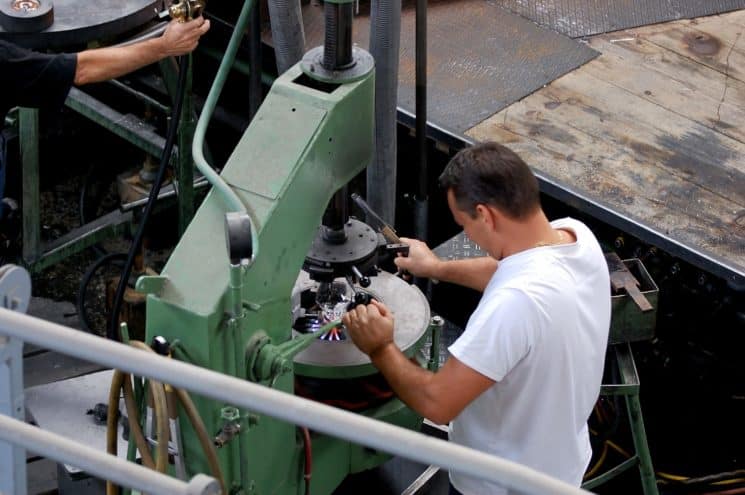
The world of the modern industry does not leave room for stagnation, especially when it comes to quality. Each company is called upon to improve in this regard in order to remain efficient and competitive. Waste, dysfunctions and sources of non-quality are real obstacles to production and quality, hence the need to identify and remedy them. Improving production quality requires particular attention to be paid to processes and the organisation of operations, in particular through a redefinition of technical media and documents (thanks to new technologies) and the implementation of appropriate quality tools.
Technical support is the basis of quality
Any operation, process step or procedure shall be recorded and detailed in a corresponding document. It is this support that allows you to be guided in your work, but also to react in the event of an error or exceptional situation (malfunctioning of a machine, for example).
Instructions, maintenance guides, operating or repair manuals, technical specifications and other reference works are some of the technical documents whose role is fundamental in the industry.
Thanks to new technologies, these media are ported in digital format, which makes it easier to create, use and update them, allowing more accurate monitoring of production and performance.
Production quality benefits fully from this redefinition of technical support, as it makes it easier to prevent and compensate for errors and non-quality elements.
One of the major challenges for the plant of the future is to effectively integrate new technologies into the various components of its organization, including those related to technical documentation.
Choose the quality tools adapted to the specificities of the company
There is no shortage of quality tools. Fruits of various industrial crops – particularly those from Japan and the United States – these methods focus on different aspects of the company’s operations aimed at improving production. This ranges from managing the company to identifying the causes of malfunctions, solving and preventing problems, and checking the reliability of processes. These are all factors that can have a direct or indirect influence on production quality.
The tools at the service of quality are therefore very present, but it is necessary to use those that can really conform to the company and its specificities. This choice depends on many criteria, including the size of the company, its activity, its organization, its objectives and its direct environment.
One example is the FMECA (Failure Mode, Effects and Criticality Analysis) method. A preventive analysis tool, it aims to identify and treat the causes of malfunctions and defects before they occur. A FMECA can be performed on a process, product or equipment to make the necessary adjustments.
ISO standards also provide considerable support in this process of improving production quality. ISO 9001 quality procedures cover a wide range of related aspects, including corrective actions and risk prevention.
About Picomto
Picomto is a SaaS web and mobile software solution to create, manage, share and analyze digital work instructions
Leave A Comment