Is your company ready for the digital revolution? The digitalization of industrial processes is radically transforming the manufacturing landscape. But how can you adapt to this inevitable transformation? At a time when 76% of industries are accelerating their digital transformation, can you really remain on the sidelines of this evolution? Indeed, digitalization represents a major challenge for all industrial companies today. This digital revolution is disrupting traditional working methods and opening new optimization perspectives.
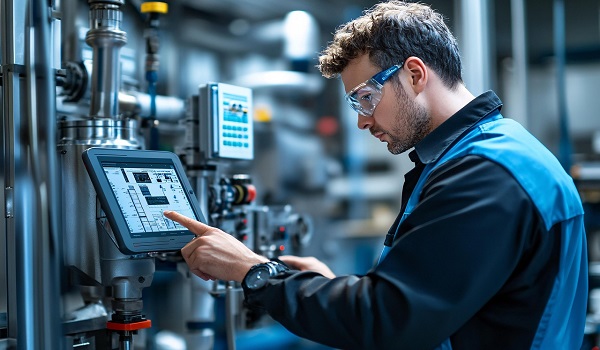
Key points about industrial process digitalization:
- 67% of industries increase their productivity through digitalization
- 25% average reduction in machine downtime
- 35% improvement in production quality
- 18-month average ROI for digitalization projects
1. What is Industrial Process Digitalization?
Today, digital technology is transforming everything. And industry is no exception. Industrial process digitalization consists of converting manual operations into intelligent digital flows.
In other words, it means replacing paper-based or verbal procedures with digital, connected, and often automated tools. This technological transformation affects all companies:
- From local SMEs to large international groups
- All sectors: automotive, food processing, chemical, aerospace…
The digital transformation in the chemical industry, for example, highlights how even the most highly regulated sectors can leverage digital tools to improve traceability, safety, and process performance.
1.1. Which Processes Can Be Digitalized?
At first glance, production often comes to mind. But in reality, the entire industrial value chain can benefit from digitalization. Each step can be optimized through appropriate digital tools.
Here are some examples of processes to digitalize:
- Creation and standardization of operating procedures → To ensure uniform, comprehensible, and easily updated methods.
- Preventive and corrective maintenance → Thanks to sensors and AI, interventions are planned before breakdowns occur.
- Quality control and inspections → Anomalies are detected faster and reports are generated automatically.
- Operator training → Via interactive tutorials, e-learning modules, or digital twins.
- Industrial document management → No more binders! Documents are accessible in one click, up-to-date, and secure.
- Performance monitoring (KPIs, production, downtime, quality, etc.) → Data is analyzed in real-time for immediate responsiveness.
Inspiring example: The SKF group has digitalized all its maintenance procedures. Result: 40% reduction in technician intervention time.
1.2. Why is it Essential Today?
Secondly, digitalization is no longer an option but a necessity. It addresses a dual requirement: performance and adaptation to new Industry 4.0 standards.
A recent study reveals that: 94% of industrial companies consider digital transformation strategic.
Why is this figure so high? Because digitalization enables:
- Reduction of operational costs
- Greater agility in dealing with unforeseen events
- Improved quality and traceability
- Better and faster team training
- Differentiation in the face of increasingly fierce international competition
In short, to stay in the race, transformation is necessary. And action must be taken now.
2. What are the Concrete Benefits of Digitalization?
First and foremost, digitalization is not just a simple change of tools. It profoundly transforms how industrial teams work on a daily basis. The benefits are real, measurable, and often quick to observe.
2.1. What Performance Gains Can Be Expected?
Secondly, let’s examine the concrete results obtained by companies that have taken the step. On average, they observe:
- +25% operational productivity Tasks are better planned and better executed.
- –30% production errors Digital procedures reduce oversights and mishandling.
- +40% product quality Controls are more frequent and better documented.
- –35% training time New arrivals become proficient faster.
Moreover, digital traceability allows better operation monitoring. The French Navy now uses digital instructions for its maintenance operations.
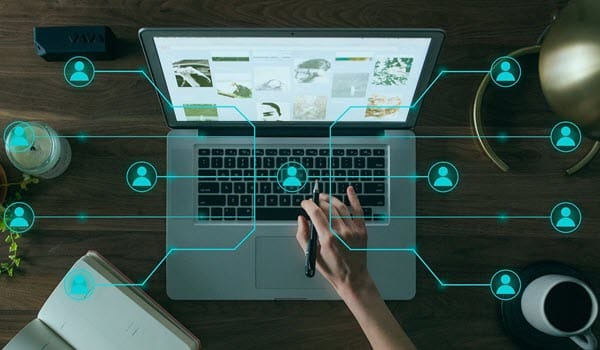
2.2. How to Improve the Operator Experience?
Thirdly, it is essential to talk about those who experience the change in the field: the operators. Thanks to digitalization, their daily work becomes simpler, more fluid, and above all safer. The main benefits for operators are:
- Clear and always up-to-date work instructions → No more searching for paper or old versions.
- Immediate access to the right information → On tablet, mobile, or embedded terminal.
- Enhanced autonomy → Decisions are made faster, without waiting for a supervisor.
- Accelerated skill development → Interactive supports promote continuous learning.
In sum, digitalization doesn’t replace humans. It supports, values, and helps them progress.
3. How to Implement Digitalization?
To begin with, it’s important to understand that digital transformation cannot be improvised. It requires a structured, progressive approach adapted to each industrial environment. First, it is essential to identify priority processes for digitalization.
These are often those that generate the most value or present the most obstacles. In this regard, good preparation makes all the difference.
3.1. What are the Key Steps?
1. Initial audit and diagnosis
- Analysis of existing processes
- Identification of improvement points
- Definition of objectives
2. Choice of technological solutions
- Selection of appropriate tools
- Compatibility assessment
- Deployment planning
3. Training and support
- Team preparation
- Progressive training
- Continuous support
3.2. How to Ensure Project Success?
The success of a digitalization project relies on several key factors:
- Involvement of all stakeholders
- Clear and regular communication
- Adapted support
- Measurable objectives
4. Which Solution to Choose for Digitalizing Your Processes?
First, let’s recall an obvious fact: the choice of solution is decisive. Indeed, an ill-suited tool can hinder the entire project dynamic.
Conversely, an intuitive, well-designed, and evolving solution promotes rapid adoption. Moreover, it directly conditions the success of digital transformation.
This is why it’s essential to choose a reliable, recognized partner, and above all, one focused on field needs.
For example, Picomto offers an integrated approach, designed for industrial realities. This platform facilitates the transition from manual processes to digital instructions, usable anywhere and anytime.
4.1. Which Features to Prioritize?
First and foremost, focus on the concrete utility of the solution. No need for an overly complex system. The important thing is to go to the essentials, with simple and effective tools.
Here are the key features to look for:
- Rapid creation of digital instructions → To standardize procedures and make them accessible to all.
- Real-time sharing in the field → To transmit information instantly to operational teams.
- Operation performance analysis → To identify weaknesses and measure progress.
- Operator skills management → To track know-how evolution and adapt training.
In short, a good solution must meet team needs without complicating their tasks. It must also provide clear visibility to production, maintenance, or quality managers.
4.2. How to Ensure Team Adoption?
At first glance, one might think that a good tool is enough. In reality, this is not the case. Adoption depends as much on technology as on human support.
For teams to embrace the solution, several levers are essential:
- A simple and intuitive interface → Users must understand the tool from the first minutes.
- Training adapted to each profile → Content must be clear, concrete, and immediately applicable.
- Personalized field support → Responsive support helps resolve blocks as soon as they appear.
- Quick visible results → The solution’s utility must be demonstrated through concrete benefits from the first weeks.
Ultimately, the more employees perceive the tool’s utility, the more they engage with it. The key to success is adoption.
Conclusion: Towards the Factory of the Future
The digitalization of industrial processes is no longer an option but a necessity. Indeed, companies that succeed in their digital transformation gain an average of 25% productivity. This evolution towards Industry 4.0 represents a strategic investment for the future.
More specifically, data digitalization plays a crucial role in unlocking operational efficiency and real-time decision-making.
It is also a key enabler of the Smart Industry, where intelligent systems and connected technologies create a more agile, responsive, and competitive industrial environment.
The time has come to engage in your digital transformation. With a solution like Picomto, you have all the tools to succeed in this transition.
FAQ
Q: What is industrial digitalization?
A: It’s the transformation of traditional industrial processes into connected digital flows to optimize production.
Q: What are the 3 pillars of digital transformation?
A: Digital technologies, process evolution, and cultural transformation of the company.
Q: What are the types of digitalization?
A: Digitalization of processes, products, services, and customer experience.
Q: What are the 5 phases of digital transformation?
A: Audit, planning, solution selection, progressive deployment, and continuous optimization.
Q: What is the benefit of digitalization?
A: Improvement in productivity, error reduction, and optimization of production costs.
Q: What’s the difference between digitalization and digital transformation?
A: Digitalization converts processes to digital, digital transformation changes the entire organization.
Q: What are the transformation processes?
A: Production, maintenance, quality, training, documentation, and skills management.
Q: How to create a transformation plan?
A: Define objectives, audit existing processes, choose solutions, and plan deployment.
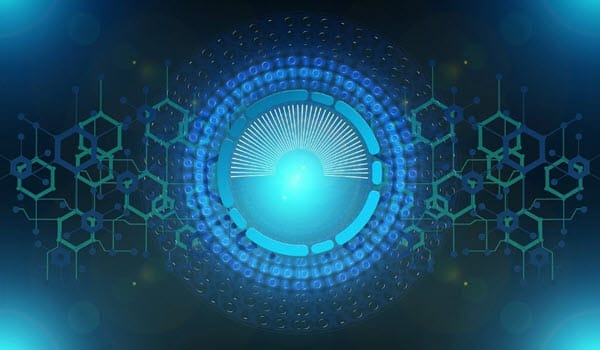
Leave A Comment