Did you know that 85% of industrial companies that master their production control show profitability 20% higher than their competitors? Industrial production control represents today one of the most strategic levers for maintaining competitiveness in a volatile economic environment. Indeed, industrial production control refers to the set of processes, methods, and tools that enable supervision, coordination, and optimization of manufacturing activities within a production unit. This discipline encompasses resource planning, real-time performance monitoring, and continuous adjustment of operational parameters.
Faced with current challenges such as raw material shortages, energy cost inflation, and growing quality requirements, mastering production control becomes more vital than ever. In this comprehensive guide, we will explore the fundamentals of production control, its key stages, available digitalization solutions, and best practices to optimize your industrial performance.
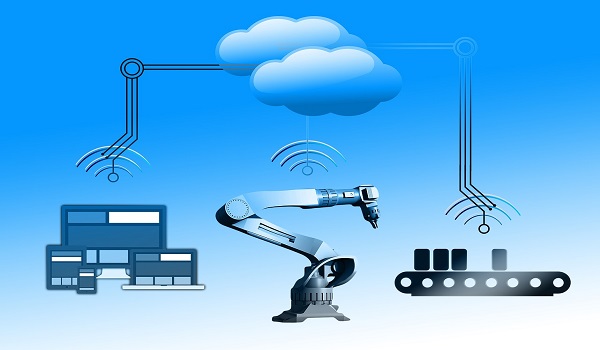
Key Takeaways Regarding Industrial Production Control :
- Resource Optimization: Waste reduction and productive efficiency improvement
- Strategic Digitalization: Digital tools enable real-time monitoring and informed decision-making
- Process Standardization: Procedure formalization ensures reproducibility and quality
- Performance Indicators: Monitoring key KPIs enables rapid identification of improvement areas
- Continuous Training: Team support conditions the success of any optimization approach
1. What is Industrial Production Control and Why is it Essential?
Industrial production control constitutes the nervous system of any modern manufacturing organization.
This cross-functional function coordinates all physical and informational flows to efficiently transform raw materials into finished products. Beyond simple monitoring, it involves a systemic approach that integrates planning, execution, and continuous improvement.
The importance of this discipline intensifies with market evolution toward more personalization and reactivity. Companies that neglect their production control expose themselves to significant losses, delivery delays, and brand image degradation.
1.1. Fundamental Objectives of Production Control
Production control primarily aims to:
- Optimize resource utilization: machines, personnel, raw materials
- Respect delivery deadlines: flow coordination to meet customer commitments
- Maintain quality: continuous monitoring of standards and norms
- Minimize costs: waste reduction and downtime minimization
- Ensure flexibility: rapid adaptation to demand variations
These objectives are structured around continuous improvement logic. Consequently, production control requires a methodical approach and adapted tools to permanently measure and adjust performance.
1.2. Different Types of Production Control
Three types of control are generally distinguished:
- Preventive control: planning and dysfunction prevention
- Concurrent control: real-time operation monitoring
- Corrective control: post-production analysis and corrective actions
Each type responds to specific needs. Furthermore, their combination enables the establishment of a robust and reactive steering system, capable of adapting to production uncertainties.
Consult our case studies to discover how companies like Veolia have optimized their production control.
1.3. Direct Impact on Industrial Performance
Effective production control generates measurable benefits:
- Productivity: increase of 15 to 25% depending on sectors
- Quality: defect reduction of 30 to 50%
- Deadlines: planning compliance improvement of 20%
- Costs: savings of 10 to 20% on operational costs
These results are explained by better activity coordination and waiting time reduction. Moreover, early problem identification limits their propagation and impact on the value chain.
2. What are the Key Stages of Effective Production Control?
Efficient industrial production control relies on a structured approach with several interdependent stages. This methodology ensures a global vision of operations while enabling precise steering of each productive system component.
The effectiveness of these stages largely depends on their integration and coordination. Thus, each phase feeds the next with essential data and information to optimize operational decisions.
2.1. Planning and Scheduling
Planning constitutes the foundation of production control:
- Demand analysis: customer needs evaluation and forecasting
- Capacity calculation: necessary resource dimensioning
- Scheduling: optimal task sequencing for production
- Supply management: supplier coordination
This stage determines the overall efficiency of the productive process. Indeed, faulty planning generates cascading dysfunctions that are difficult to correct during production.
2.2. Real-time Monitoring
Continuous monitoring enables rapid identification of deviations:
- Data collection: sensors, operator inputs, automated systems
- Dashboards: key indicator visualization
- Automatic alerts: critical deviation notifications
- Traceability: operation and decision history
This permanent surveillance promotes increased reactivity to uncertainties. Furthermore, it constitutes the database necessary for analysis and continuous improvement.
2.3. Analysis and Continuous Optimization
Exploitation of collected data enables identification of improvement areas:
- Performance analysis: comparison with set objectives
- Bottleneck identification: limiting constraint detection
- Action plans: corrective measure definition
- Capitalization: learning integration into processes
This continuous improvement approach progressively transforms performance. Additionally, it develops excellence culture within operational teams.
3. How to Successfully Digitalize Your Production Control?
Industrial production control digitalization represents today an obligatory passage to maintain competitiveness.
This transformation is not limited to technological tool acquisition but implies profound process and work method restructuring.
The challenge consists of leveraging digital technologies to create an integrated, reactive, and predictive steering system. This evolution requires a clear strategy and change management adapted to each organization’s specificities.
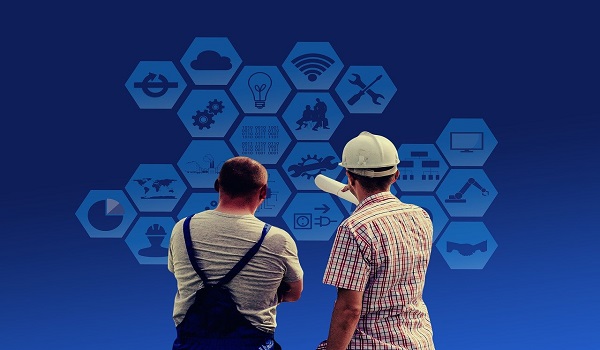
3.1. Digitalization Advantages
Digital transformation brings tangible benefits:
- Increased visibility: real-time access to production status
- Predictability: dysfunction anticipation through predictive analysis
- Enhanced collaboration: information sharing between teams
- Total traceability: automatic operation recording
- Flexibility: rapid adaptation to planning changes
These advantages translate into significant operational performance improvement. Furthermore, they enable teams to concentrate on higher value-added tasks.
3.2. Essential Digital Tools
The production control digital ecosystem includes:
- MES (Manufacturing Execution System): production operation steering
- ERP (Enterprise Resource Planning): integrated resource management
- IoT solutions: automatic machine data collection
- BI tools: performance analysis and visualization
- Mobile applications: nomadic access to critical information
Integration of these tools creates a coherent informational environment. However, their successful deployment requires a progressive approach and adapted user training.
3.3. Focus on Picomto as a Complete Solution
Picomto proposes an integrated production control approach:
- Digital work instructions: step-by-step operator guidance
- Integrated quality control: automated verifications and traceability
- Skills management: qualification and training monitoring
- Advanced analytics: personalized dashboards and indicators
- IoT compatibility: integration with industrial equipment
This solution unifies different production control aspects in an intuitive interface. Moreover, it adapts to each industrial sector’s specificities through configuration flexibility.
4. What are the Best Practices to Optimize Your Production Control?
Industrial production control optimization relies on adopting proven best practices by industrial leaders. These methods, derived from experience and continuous improvement, enable achieving operational excellence while maintaining flexibility necessary for market evolution.
Implementation of these practices requires strong management commitment and complete team adherence. However, obtained results largely justify efforts made to transform the organization.
4.1. Performance Indicators to Monitor
Appropriate KPI selection conditions steering effectiveness:
- OEE (Overall Equipment Effectiveness): global machine efficiency measure
- Cycle time: average production duration per unit
- Scrap rate: non-conforming product proportion
- Schedule adherence: on-time delivery percentage
- Inventory turnover: raw material flow velocity
- Hourly productivity: units produced per worked hour
These indicators must be aligned with strategic objectives. Consequently, their regular monitoring enables rapid deviation identification and necessary corrective action engagement.
4.2. Importance of Standardized Procedures
Standardization guarantees reproducibility and quality:
- Operating procedure formalization: clear and accessible documentation
- Systematic quality controls: critical point verifications
- Escalation procedures: structured incident management
- Preventive maintenance: rigorous intervention planning
- Internal audit: regular standard compliance verification
This approach significantly reduces variations and errors. Furthermore, it facilitates new employee integration and skill transfer.
4.3. Team Training and Support
The human factor remains determining in success:
- Technical training: tool and procedure mastery
- Objective awareness: objective understanding
- Operational coaching: field accompaniment
- Experience feedback: learning capitalization
- Recognition: best practice valorization
A structured training program maximizes new method adoption. Similarly, it develops team autonomy and adaptation capacity to technological evolution.
Conclusion
Industrial production control constitutes a major strategic lever for manufacturing companies wishing to maintain competitiveness in a demanding economic environment.
Through this guide, we have explored this discipline’s fundamentals, key stages, and best practices to optimize performance.
Digitalization appears as an unavoidable catalyst for this transformation. Indeed, digital tools enable reaching unprecedented performance levels in terms of reactivity, precision, and operational efficiency.
Adopting a structured approach, combined with adapted technological solutions like Picomto, opens the path toward industrial excellence. Companies that invest in production control optimization benefit from sustainable competitive advantages.
Contact us today to discover how Picomto can transform your production control and boost your industrial performance.
FAQ
What is production control?
Process of supervision and optimization of manufacturing activities to guarantee quality, deadlines, and costs.
What is an example of production control?
Overall Equipment Effectiveness (OEE) monitoring with automatic alerts in case of deviation.
How to control production?
Use of KPI indicators, MES systems, IoT sensors, and real-time dashboards.
How to measure industrial production?
Analysis of OEE, conformity rate, cycle time, and unit costs.
What are the two types of control?
Preventive control (anticipation) and corrective control (reaction to detected deviations).
What is the objective of control?
Optimize performance, guarantee quality, and respect production objectives.
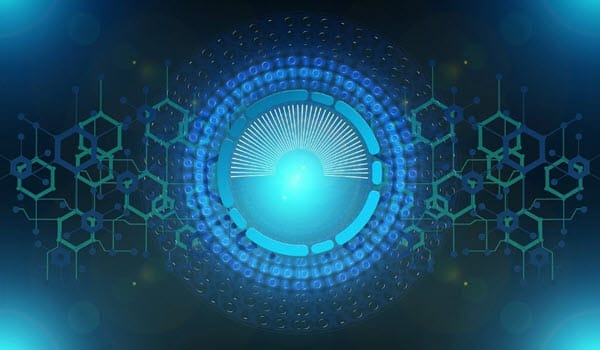
Leave A Comment