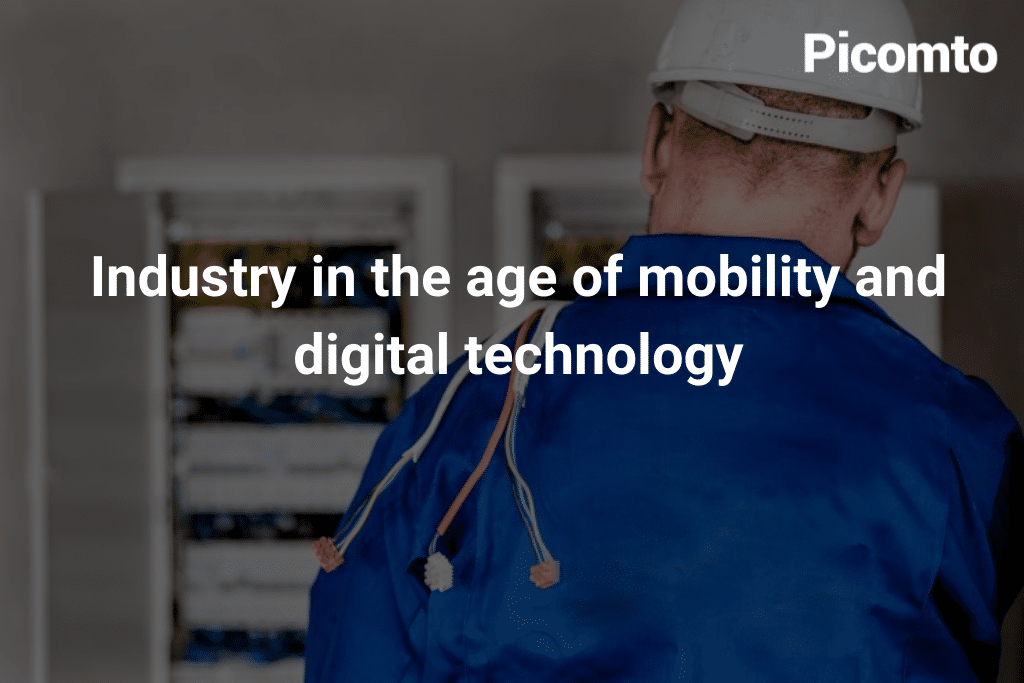
Industry benefits in many ways from mobility brought by new hardware and software tools. It gains in accessibility, efficiency and responsiveness. In addition, companies that integrate and use these new tools among others via tablets and smartphones help their employees to benefit from significant time saving.
Mobility: better accessibility, increased responsiveness and time saving
The fact that any team working in the company has immediate and simplified access to the data necessary to carry out their various operations inherent to its mission represents a considerable asset. Thanks to dedicated mobile applications, it can access the follow-up, work instructions, operating modes or even the procedures to follow in the event of an incident or malfunction. Similarly, thanks to these same integrated tools that are linked to the company’s information system which often includes additional functionalities, it is able to communicate within its department and with other actors of the company.
Consult our article on: the role of operating modes in industry
This last point is not just a detail among the advantages of mobility in industry. Exchange, pooling and harmonization of information that it allows to promote their real-time sharing while facilitating decision-making processes. This is the kind of asset the mobile ERP (Enterprise Resource Planning) promises.
Increasingly deployed in companies, these mobile ERP are accessible from smartphones or tablets. For example, they offer the possibility to inquire about the state of stocks, access a product catalog or inquire about delivery times while you are not in the office. It allows employees to have a unified data basis, have a tool that improves process management, enjoy functionalities adapted to their missions and gain in traceability of information.
Mobility is also an assistance service provided by equipment manufacturers via internet
Mobility in modern industry concerns all the actors of a company, whether they are internal or external. These include manufacturers of machines it uses in its production. This equipment corresponds to rather heavy investments, while maintaining their performance level represents an important challenge. This is because they determine the productivity of the company and quality.
To help ensure this, these manufacturers provide it with assistance and remote diagnosis services that are increasingly elaborate and adapted to field reality. These services take advantage of the possibilities offered by internet and mobile platforms.
For instance, Chiron, a specialist in machining centers, has developed the ePS network for his customers. In case of a breakdown of one of the machines used by a company, a message (e-mail or sms) is immediately sent to the relevant department within the company to establish an initial assessment of the severity of the incident. The customer is then contacted within fifteen minutes for a more accurate analysis and full assistance in order to organize a quick and efficient intervention.
About Picomto
Today, the industry is related to a huge problem that is the transmission of knowledge. Formalization and sharing knowledge in an industry is crucial for its present and future. Age pyramid, good practices, obligation to follow precise procedures…
Picomto was born from this observation and offers the solution to capture and disseminate the industry’s know-how.
A web and mobile software solution in Saas to create, manage, share and analyze operating modes, maintenance procedures and after sales support.
Picomto is part of the digitalization of industry, #SmartIndustrie #Industrie4.0, #Paperless
For more information, consult Picomto website.
Leave A Comment