Facing accelerated regulatory developments, how can your company adapt to new quality standards without compromising its performance? This crucial question now concerns all quality managers who must navigate a constantly evolving regulatory environment. Integrating new standards into quality processes represents a major challenge for modern enterprises. Indeed, the regulatory landscape evolves rapidly, driven by technological innovation and growing consumer requirements. This dynamic forces organizations to rethink their traditional methods and adopt more agile and digitalized approaches.
Non-compliance with new standards exposes companies to considerable financial, reputational, and operational risks. However, successful integration can transform these constraints into sustainable competitive advantages. Organizations that master this transformation benefit from better operational efficiency, cost reduction, and improved brand image.
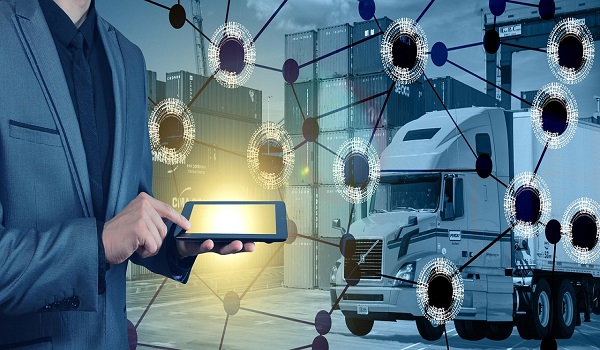
Key takeaways regarding the integration of new standards into quality processes:
- Strategic anticipation: Early identification of applicable standards enables optimal preparation and reduces adaptation costs
- Essential digitalization: Digital tools facilitate document management, procedure monitoring, and continuous compliance
- Collaborative training: Team involvement in the change process ensures successful adoption of new practices
- Methodical monitoring: Implementation of performance indicators enables effective compliance control and continuous improvement
- Continuous optimization: Standards integration must be accompanied by a permanent process improvement approach
Looking for concrete solutions to modernize your quality process?
Contact our experts for a personalized analysis of your needs.
1. What are the current challenges of integrating new standards?
Integrating new quality standards represents a true obstacle course for contemporary companies. The challenges are multiple and interconnected, requiring a systemic approach to be effectively overcome.
The growing complexity of regulations, coupled with their rapid evolution, creates an environment where adaptability becomes a key competence.
1.1. How to identify standards applicable to your sector?
Identifying relevant standards constitutes the first crucial step of your quality approach. This phase requires structured and methodical regulatory surveillance.
Effective identification methods:
- Monitoring sectoral standardization bodies
- Consulting professional associations
- Analyzing customer and contractual requirements
- Monitoring international regulatory developments
The systematic approach involves creating a comprehensive normative mapping. This mapping must identify mandatory, recommended, and emerging standards. Furthermore, evaluating the impact of each standard on your existing processes allows prioritizing actions to be undertaken.
1.2. What are the risks of non-compliance?
Non-compliance with new standards exposes your organization to serious and lasting consequences. These risks extend far beyond financial aspects to impact your entire business ecosystem.
Main identified risks:
- Financial sanctions and regulatory penalties
- Loss of certifications and accreditations
- Brand image and reputation deterioration
- Market and tender exclusion
- Civil and criminal liability of executives
Operational consequences also include business interruption, loss of strategic customers, and team demotivation. Moreover, post-facto compliance costs typically prove higher than a proactive approach.
1.3. Why has digitalization become essential?
Digitalization radically transforms quality process management and standards integration. This technological evolution offers unprecedented opportunities to simplify and optimize compliance.
Digitalization advantages:
- Automation of control and validation processes
- Complete traceability of actions and modifications
- Instant access to procedures and standards
- Reduction of human errors and delays
- Facilitation of audits and controls
Digitalization also enables better team collaboration and practice standardization. Additionally, analysis of collected data facilitates identification of improvement areas and continuous process optimization.
Discover how our clients have transformed their quality processes.
Check our case studies for inspiration.
2. How to effectively prepare for new standards integration?
Methodical preparation constitutes the foundation of successful new quality standards integration. This strategic phase largely determines your transformation success and minimizes failure risks.
Rigorous preparation involves in-depth analysis of your current situation, gap identification, and definition of a structured action plan.
2.1. What methodology to adopt for impact analysis?
Impact analysis represents the fundamental stage of your standards integration approach. This analysis must be exhaustive and methodical to guarantee identification of all concerned elements.
Key impact analysis steps:
- Mapping existing processes and their maturity
- Identifying gaps between current state and new requirements
- Evaluating resources needed for compliance
- Prioritizing actions according to criticality and feasibility
- Estimating implementation costs and timeframes
Impact analysis must also consider interdependencies between different processes. Consequently, a transversal approach allows identifying possible synergies and optimizing resource allocation.
2.2. How to mobilize teams around change?
Team mobilization constitutes a critical success factor in new standards integration. Change cannot succeed without adhesion and commitment from all concerned collaborators.
Effective mobilization strategies:
- Transparent communication on challenges and benefits
- Training adapted to specific needs of each team
- Involving collaborators in designing new procedures
- Recognition and valorization of individual contributions
- Implementation of feedback and continuous improvement systems
Resistance to change can be circumvented through a participatory approach. Indeed, team involvement in solution definition promotes appropriation and commitment. Moreover, personalized support for collaborators facilitates transition to new practices.
2.3. Which digital tools to choose for facilitating transition?
Digital tool selection directly influences your standards integration process efficiency. These tools must respond to your specific needs while integrating harmoniously into your technological ecosystem.
Essential selection criteria:
- Compatibility with existing systems
- Ease of use and team adoption
- Evolution and customization capabilities
- Data security and confidentiality
- Available technical support and training
Integrated platforms offer the advantage of centralized management and data consistency. Nevertheless, functionality evaluation must be done in regard to your real needs to avoid over-complexification.
3. What are the key steps for successful standards integration?
Successful integration of new quality standards requires a structured and progressive approach.
This methodical process minimizes risks, optimizes resources, and ensures smooth transition to new standards. Each step must be carefully planned and executed to guarantee overall transformation process efficiency.
3.1. How to create and standardize your new procedures?
Creating standardized procedures represents the core of new standards integration. This standardization ensures practice consistency and facilitates compliance control.
Procedure creation methodology:
- Detailed analysis of specific normative requirements
- Collaborative writing involving subject matter experts
- Validation by stakeholders and quality managers
- Pilot tests on restricted perimeters
- Adjustments based on experience feedback
Standardization must integrate existing best practices while respecting new requirements. Furthermore, using digital tools facilitates procedure creation, dissemination, and updating. Terminological consistency and instruction clarity guarantee uniform application by all users.
3.2. Which deployment strategy to adopt?
Strategic deployment determines new standards integration success. This critical phase requires rigorous planning and effective coordination between all involved actors.
Recommended deployment approaches:
- Progressive deployment by department or process
- Intensive team training before implementation
- Close support during transition phase
- Continuous performance indicator monitoring
- Real-time adjustments according to encountered difficulties
Wave deployment allows capitalizing on learnings and optimizing approaches. Moreover, identifying internal ambassadors facilitates adoption and operational problem resolution. Regular communication on progress maintains team motivation.
3.3. How to ensure continuous monitoring and compliance?
Compliance monitoring constitutes a permanent process that guarantees quality standards maintenance over time. This active surveillance allows rapid identification of deviations and implementation of necessary corrections.
Effective monitoring mechanisms:
- Key Performance Indicators (KPIs) specific to each standard
- Scheduled and unannounced internal audits
- Automated reporting of gaps and non-conformities
- Periodic reviews of processes and procedures
- Continuous updating of normative references
Continuous compliance requires a quality culture shared by all collaborators. Consequently, regular awareness and continuous training reinforce team commitment. Digital tools facilitate data collection and trend analysis.
Optimize your quality monitoring with our solutions.
Request a personalized demonstration of our monitoring tools.
4. How to optimize your quality process through digital solutions?
Digitalization revolutionizes quality process management by replacing traditional methods with intelligent solutions.
This transformation enables automating controls, centralizing documentation, and guaranteeing complete traceability. Companies now adopt integrated platforms to pilot their quality approach efficiently.
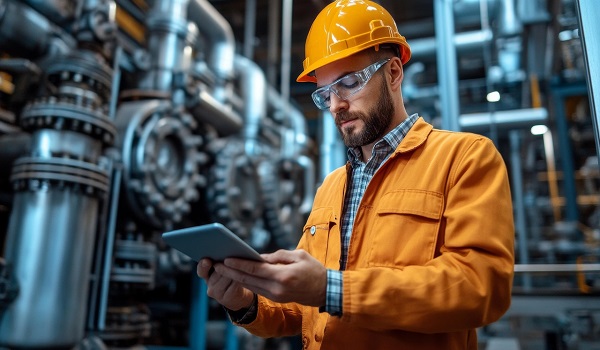
4.1. What advantages does a digital instruction management platform offer?
Digital platforms radically transform quality process management:
- Documentary centralization: All procedures are accessible from a single point
- Complete traceability: Every action is automatically recorded and timestamped
- Enhanced collaboration: Teams work simultaneously on the same documents
- Automated compliance: Compliance checks occur in real-time
- Predictive analysis: Collected data anticipates potential problems
This digital approach eliminates human errors and considerably accelerates processes. Moreover, it guarantees perfect consistency between different teams and production sites.
4.2. How does Picomto revolutionize quality procedure management?
Picomto offers a complete solution to digitalize your quality process:
- Interactive instructions: Step-by-step guides with integrated visual supports
- Automated controls: Instant verification of critical steps
- Real-time reporting: Dashboards to pilot performance
- ERP integration: Synchronization with existing systems
- Continuous training: Adaptive learning modules for your teams
This platform adapts to all industrial sectors, notably automotive, aerospace, and pharmaceutical. Its intuitive interface facilitates adoption by field operators.
4.3. Return on investment: what gains to expect?
Investment in a digital solution generates measurable benefits:
- Error reduction: Average decrease in non-conformities
- Time savings: Acceleration of control processes
- Documentary savings: Elimination of printing and distribution costs
- Continuous improvement: Optimization based on collected data
- Enhanced competitiveness: Facilitated certification and simplified audits
These results typically observe within six months following implementation. Initial investment amortization typically occurs between 12 and 18 months.
Conclusion
An optimized quality process constitutes the foundation of industrial operational excellence. Digitalization transforms this approach into a strategic competitive advantage, enabling achievement of unparalleled performance levels. Solutions like Picomto democratize access to professional tools, facilitating adoption by field teams.
Investment in a digital platform generates measurable returns short-term while preparing the company for future challenges. This transformation emerges as a necessity to maintain competitiveness in a constantly evolving industrial environment.
Ready to transform your quality process?
Request a personalized demonstration and discover your organization’s potential.
FAQ
What are process quality standards?
ISO 9001, ISO 14001, ISO 45001, and specific sectoral standards.
What are the steps to implement a quality process?
Diagnosis, planning, implementation, training, control, and continuous improvement.
What are quality-related standards?
ISO 9001, ISO 13485, ISO 14001, AS9100, and GMP.
What are the 4 pillars of quality?
Planning, control, assurance, and continuous improvement.
What is the main objective of the quality process?
Guarantee product conformity and satisfy customer requirements.
What are the 7 major principles of quality?
Customer orientation, leadership, personnel involvement, process approach, improvement, factual decisions, relationship management.
What is quality conformity?
Compliance with defined requirements and specifications for a product/service.
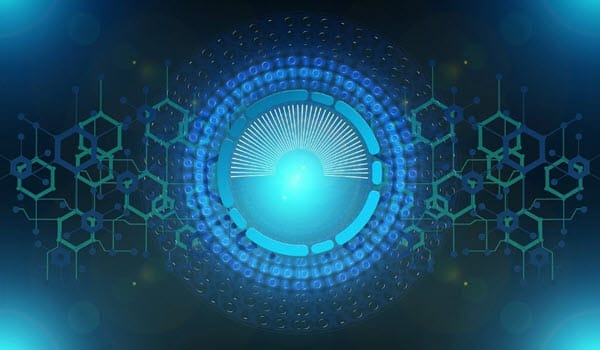
Leave A Comment