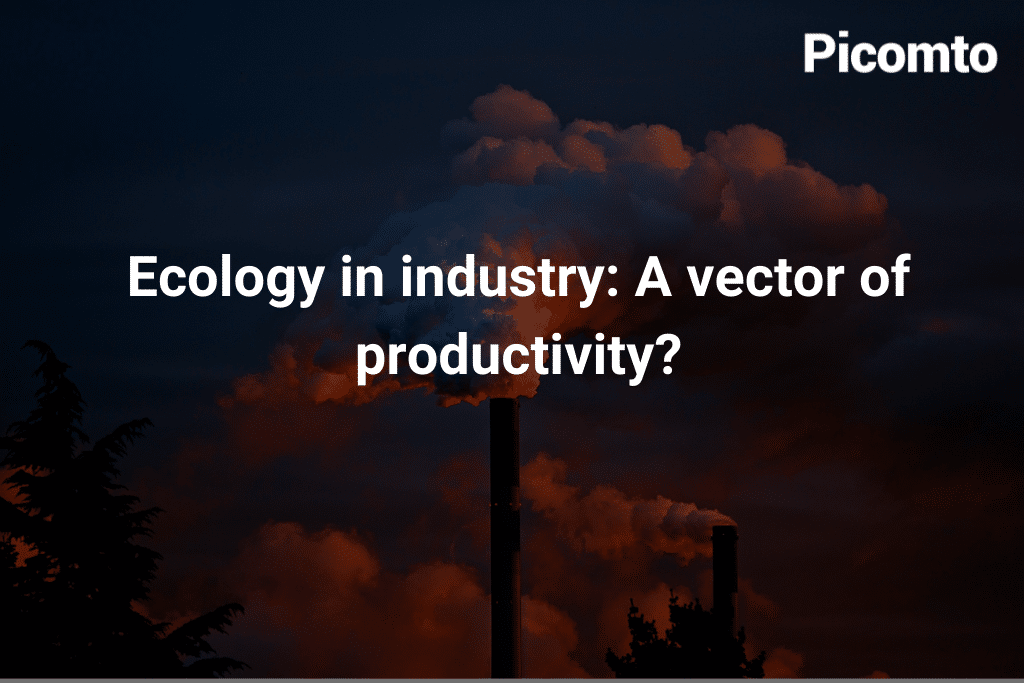
Industrial activity and environmental issues have long been considered irreconcilable. Factories do not only produce goods, but also generate waste, discharge and destruction of natural resources, some of which are non-renewable. These last years, however, major efforts have been deployed to reverse this tendency and make industry more ecological. An awareness of the seriousness of the environmental situation has urged a number of manufacturers to commit to sustainable development. A choice dictated by the alarming facts (harmful effects of greenhouse gases, depletion of resources, destruction of natural habitats of many living species, pollution…), but also by the benefits that the company can derive from such an approach especially in terms of productivity.
Making the factory more ecological implies the streamlining production
In order for the activity of the factory to align with the major principles of ecology and sustainable development, changes were made at the level of several aspects of production. Among other things, this is streamlined through the optimization of energy and material resource consumption, minimization of waste and its reuse either by the company itself or by another organization. The streamlining of production also implies the use of advanced technologies such as digital tools that replace paper. This is what is observed, among other things, with operating modes, which are easier to access, more practical and closer to the reality of business when they can be consulted on tablets and other terminals. This allows both efficiency gains and reduction of waste, paper in this case.
In this respect and in many others, the streamlining of production that is inclined towards a “greener” industry is part of a continuous improvement approach.
Significant savings
Restudying production to make it more ecological is also revising its supply system and its purchasing policy. More and more companies are making local raw material producers their priority which reduces the cost associated with the transportation of these materials and logistics in general.
Therefore, a significant amount of money is saved. But, it can also come from other measures, the main of which relates to the fight against waste. The 3 M method, for instance, aims to reduce waste and unnecessary capital assets. It identifies 3 types of waste:
- Deliberate waste (Muda)
- Irregularity of activity flows associated with buffer stocks (Mura)
- Excesses (Muri)
They comply with inflated stocks by estimation and appreciation errors. This waste exerts considerable pressure on the cash flow (fixed assets, overload and financial losses). Eliminating it saves the company valuable financial resources and provides a smoother and more efficient production line.
A healthier environment for the company’s stakeholders
It seems obvious that allowing employees to evolve in a healthy work environment can only have positive impact on their performance. Sources of pollution mustn’t be reduced only outside the factory (discharge, waste…). They must also be reduced within the workstations to preserve the health and well-being of operators. This makes them more effective and motivated while helping to fight against absenteeism due to health problems. Productivity of the company can only be improved.
About Picomto
Today, industry is linked to a major problem which is knowledge transfer. Formalization and knowledge sharing in a company are essential for its present and future. Age pyramid, good practices, obligation to follow precise procedures…
Picomto was born from this observation and offers the solution to capture and disseminate the industry’s know-how.
A web and mobile SaaS solution to create, manage, share and analyze operating modes, maintenance procedures, internal procedures and ASS support.
Picomto is part of the digitalization of industry #smartindustry#industry4.0, #paperless
For more information, consult Picomto website
Leave A Comment