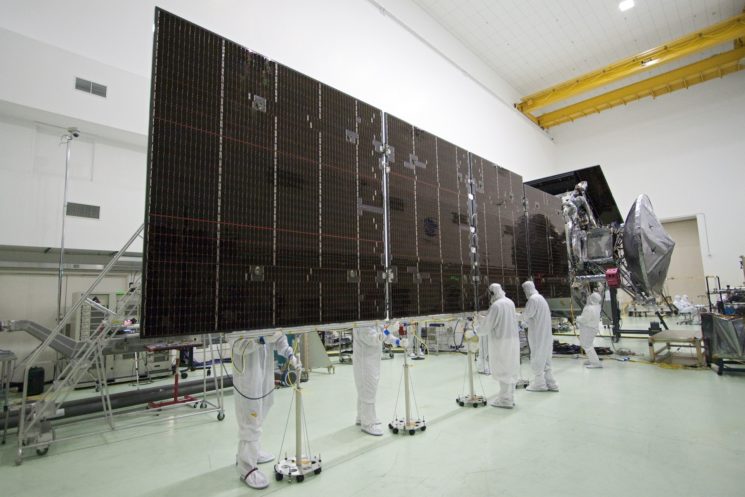
Lean and Six Sigma methods for industry are different in several respects, but they are not incompatible. When combined, these complementary approaches have many benefits for companies, particularly in terms of performance and customer satisfaction. As with any improvement initiative, its effectiveness depends on the quality of its organization and implementation.
Lean against worthless tasks and waste
Designed and implemented in Toyota factories four decades ago, the Lean method aims to eliminate waste (muda) and tasks with no added value for the customer, by improving clearly defined aspects: reducing lead times and costs, introducing a “just-in-time” industrial production system, increasing fluidity and flexibility.
When the Lean method is implemented under optimal conditions, it should enable the company to be more responsive to the variability of customer expectations.
The Six Sigma method for process reliability
The Six Sigma method was introduced a little later, in the 1980s, within the Motorola group. This organizational mode favors the reliability of processes by reducing their variability. By designing processes that are predictable and easily reproducible, Six Sigma is expected to bring the company closer to zero defects and customer satisfaction.
The application of this organization involves a five-step approach, grouped under the acronym DMAIC:
- Define (define the objective)
- Measure (measure customer expectations)
- Analysis (analyze problems, strengths and weaknesses)
- Improve (improve)
- Control (control quality).
Responsibility for its implementation rests with the Black Belt, responsible for project management and training of Green Belts, as well as the Champion (Deployment Director or Excellence System Director) and the Master Black Belt, who trains and supervises the black belts.
Two process- and customer-oriented methods
Both organizational methods are used to improve processes and customer satisfaction. They focus their efforts on activities that can create quality deficiencies and delays that can penalize production, and therefore the company’s performance.
By merging their principles to obtain Six Sigma Lean, we strive to eliminate scrap, retouching, defects and manufacturing errors, to transform or remove phases without added value from the process in the customer’s sense. Lean Six Sigma thus makes it possible to pursue a strategy of continuous improvement that takes into account customer expectations in terms of quality, but also deadlines and costs.
Objectives and prerequisites for an effective Lean Six Sigma approach
Lean Six Sigma aims to increase operational and financial performance by improving quality, lead times, costs and profit share. It also aims to satisfy customers, but also the company’s other partners: employees, suppliers, shareholders…
To achieve these objectives, it is recommended to act around several axes:
- Process optimization: simplify processes by improving information, production and decision-making flows, accelerate them through better resource management, define influential factors, reduce dispersion, eliminate dysfunctions
- Promote communication and collaboration between services
- Focus on the values defined by the client and the expectations of shareholders, as well as on the operational performance of employees (providing them with the means and tools for improvement, ensuring them improved working conditions)
This approach gives rise to major changes in the company’s organization, making it necessary to have a change management policy adapted to the situation.
About Picomto
Picomto is the web and mobile software solution for creating, managing, sharing, consulting and analyzing visual work instructions.
Leave A Comment