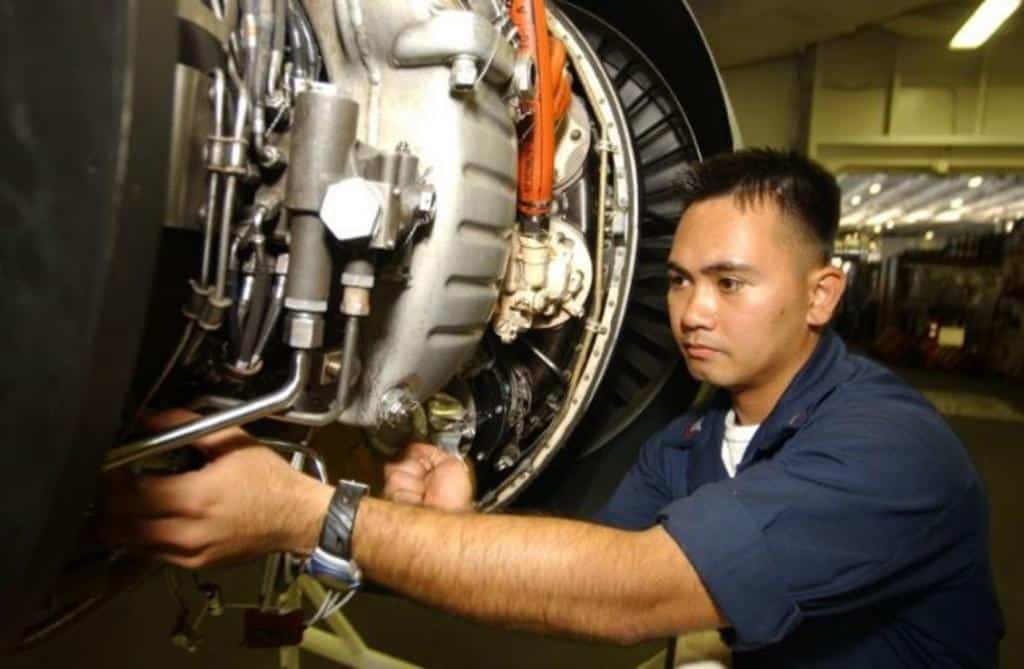
Preserving the operational capacities of the means of production is vital for any company. The quality and efficiency of maintenance are crucial to the smooth running of its production, particularly with regard to cost management and loss of revenue.
Maintenance: a guarantee of performance
When it is effective, maintenance ensures customer satisfaction, because we are then able to provide it on time and guarantee the quality of the product. At the same time, it also makes it possible to maintain the value of the means of production: machines see their lifespan extended, which reduces the need to invest in new equipment. To achieve this in an optimal way, the maintenance actions to be carried out must be listed in a maintenance range.
However, no equipment is totally immune to failure. When this occurs, corrective maintenance operations must be carried out as quickly as possible. This may be a formal repair or a breakdown service (temporary repair, which will necessarily lead to a subsequent repair). During the entire period from the occurrence of the failure to the end of the corrective maintenance operation, the defective machine is immobilized, which penalizes the company in its production capacities. Reducing machine downtime is a major challenge for the company, which benefits from opting for a proactive approach to protect itself against these risks. Priority is thus given to preventive maintenance, which reduces the need for corrective action.
Focus on prevention
To use the definition proposed by AFNOR, preventive maintenance “carried out at predetermined intervals or according to prescribed criteria and intended to reduce the probability of failure or deterioration in the functioning of an asset”. It consists in acting even before the failure or breakdown occurs.
One form of preventive maintenance is called systematic maintenance. This involves drawing up a provisional plan of the interventions (replacement of parts) to be carried out based on the operating time or the accumulated work units.
More expensive, but with proven efficiency, conditional (or predictive) preventive maintenance is more applicable to particularly expensive equipment whose downtime is detrimental to the company’s production capacity. Conditional preventive maintenance is based on the study of machine operating data. These parameters are collected by sensors, then analyzed and compared with reference values. If the measurements do not match or deviate from these, a failure is to be expected. The maintenance service is alerted and can therefore intervene early enough to prevent its occurrence. One of the main advantages of conditional preventive maintenance is therefore that it allows the initiative to be maintained: you can choose the time of the intervention, without affecting production.
Analysis and management tools for maintenance
Various assets are available to companies to enable them to carry out an effective maintenance policy. They can rely on the FMECA tool which, by analyzing machine failures, their causes and effects, makes it possible to establish a preventive maintenance plan for each piece of equipment. Failures are assessed through their frequency, severity and the quality of the detection system. Criticality is calculated on the basis of these 3 criteria.
Companies also have a CMMS (Computer Assisted Maintenance Management) software tool at their disposal for the operations of their maintenance services. It is a tool for analyzing, archiving and organizing maintenance missions integrated into their information systems. It includes, among other things, the organization of technical and human maintenance resources (spare parts, equipment, skills, etc.), the planning of interventions, the control of their costs and the collection of information concerning the maintenance work carried out (causes of breakdowns, duration of the intervention, observations of the technician in charge of maintenance, etc.).
More effective maintenance procedures
Picomto is a software solution to create digital step-by-step work instructions used in production and maintenance. Contact us for more detail.
Leave A Comment